The Practical Application of Lean Principles in Manufacturing
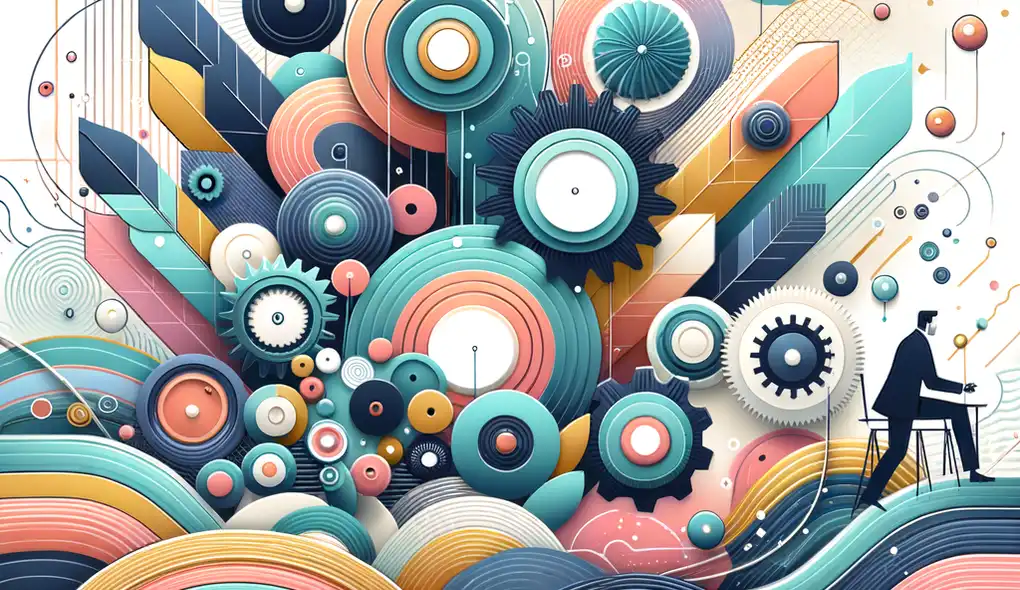
Lean manufacturing, otherwise known as lean production, is an approach to manufacturing that seeks to minimize waste without compromising productivity. It is founded on the Toyota Production System (TPS), developed by Toyota's engineers and executives to streamline production and improve efficiency. Lean principles focus on delivering maximum value to the customer while reducing non-value-adding activities. When applied correctly, these principles can revolutionize manufacturing processes and the roles of engineers who implement and maintain them. In this article, we will explore the practical applications of lean principles in manufacturing environments.
Value Stream Mapping
The first step towards implementing lean principles is to understand the value stream, which encompasses all activities, both value-added and non-value-added, that bring a product from concept to customer. Value Stream Mapping (VSM) is a tool that helps manufacturers visualize the entire production process and identify where waste occurs. Engineers use VSM to pinpoint redundancies, delays, and unnecessary steps in their production lines, then work to eliminate them to create a smoother, more efficient value stream.
For instance, an automotive manufacturer may use VSM to discover that parts are being transported inefficiently between assembly stations, leading to delays and increased handling. In response, the manufacturer might reorganize the floor layout for better flow or implement Just-In-Time (JIT) delivery systems to reduce waiting times and minimize inventory levels.
The Five S's of Lean
The second practical application of lean principles is the implementation of the 5S framework: Sort, Set in Order, Shine, Standardize, and Sustain. The 5S system promotes organization, cleanliness, and standardization, all of which are crucial for efficient operations.
An example of this can be seen in a machine shop where tools, parts, and information are often scattered. Introducing 5S can help improve workstation organization, allowing quicker changeover times, reducing the likelihood of mishandling or misplacing items, and ultimately improving productivity.
Continuous Improvement (Kaizen)
Central to lean manufacturing is the principle of continuous improvement, or Kaizen. This mentality encourages constant evaluation and improvement of processes by every member of the organization, from the shop floor to management. Engineers play a critical role in facilitating Kaizen by designing systems that allow for easy modifications and by leading cross-functional teams in problem-solving exercises.
A practical example of Kaizen in action is a manufacturer who observes that its packing process is the bottleneck in its production line. Engineers might work with workers to discuss possible solutions, leading to a redesigned workflow that improves packing speed without increasing errors or worker strain.
Pull Systems and Just-In-Time (JIT) Manufacturing
Rather than pushing products through to the next stage of production based on forecasts (push system), lean encourages a pull system approach, where products are only produced to meet actual demand. JIT is a strategy that aligns production schedules closely with customer orders, thereby reducing excess inventory. Pull systems and JIT rely on the concept of demand-driven production, which eliminates waste associated with overproduction and storage of unsold goods.
A practical application can be seen when a company introduces Kanban, a scheduling system for lean and JIT manufacturing. Kanban helps visualize work, limit work-in-progress, and ensure a new work is started only when there is demand for it. This has been particularly effective in reducing work-in-progress inventory and the associated holding costs.
Total Productive Maintenance (TPM)
Maintaining equipment in optimal condition is vital to ensure continuous and defect-free production. Total Productive Maintenance is a lean approach to maintenance that focuses on proactive and preventive maintenance to maximize the operational efficiency of equipment. Engineers are pivotal in implementing TPM by establishing regular maintenance routines and tracking equipment performance to foresee and prevent failures.
For example, an electronics assembly line could use TPM to ensure that all soldering stations are consistently operating within specified parameters, which reduces the risk of defects and downtime.
Cross-Training for Flexibility
Lean manufacturing requires a flexible workforce that can quickly adapt to changes in production demands. Cross-training employees enables a company to shift workforce efforts seamlessly whenever necessary. This not only reduces bottlenecks but also leads to a more skilled and engaged workforce.
In a practical sense, engineers may design workstations and processes that are easy for multiple workers to operate, and develop training programs that ensure workers are able to perform a variety of tasks within a production environment.
Conclusion
The practical applications of lean principles in manufacturing are vast and impact many facets of the production process. By focusing on waste reduction and continuous improvement, manufacturers realize significant gains in efficiency and cost savings. Engineers play a fundamental role in implementing lean strategies, capacity planning, and ensuring that flexibility and responsiveness are built into the manufacturing process. Embracing lean principles is not just about making incremental changes; it's about instilling a culture of excellence and efficiency that can give a manufacturing company a strong competitive edge in the market.
Frequently Asked Questions
Frequently Asked Questions
What is Lean Manufacturing?
Lean manufacturing, also known as lean production, is a methodical approach to manufacturing that aims to reduce waste while maintaining or increasing productivity. It focuses on providing maximum value to the customer by eliminating non-value-adding activities from the production process.
How Did Lean Manufacturing Originate?
Lean manufacturing originated from the Toyota Production System (TPS), which was developed by Toyota's engineers and executives to optimize production processes and enhance efficiency. The principles of lean manufacturing have since been adopted by many industries worldwide.
What Are the Key Principles of Lean Manufacturing?
The key principles of lean manufacturing include continuous improvement (Kaizen), value stream mapping, the 5S framework (Sort, Set in Order, Shine, Standardize, Sustain), pull systems, and Just-In-Time (JIT) manufacturing, total productive maintenance (TPM), and cross-training for flexibility.
How Can Lean Principles Benefit a Manufacturing Environment?
Lean principles can benefit a manufacturing environment by reducing waste, improving efficiency, enhancing quality, reducing lead times, increasing productivity, and fostering a culture of continuous improvement. These benefits ultimately lead to cost savings and a more competitive position in the market.
What Role Do Engineers Play in Implementing Lean Manufacturing?
Engineers play a crucial role in implementing lean manufacturing by analyzing processes, identifying areas of improvement, designing efficient systems, leading Kaizen events, optimizing workflows, and ensuring equipment maintenance. Their expertise is instrumental in driving lean initiatives and achieving operational excellence.
How Can Companies Measure the Success of Lean Implementation?
Companies can measure the success of lean implementation through key performance indicators (KPIs) such as cycle time reduction, defect rate improvement, inventory turnover, lead time reduction, cost savings, employee engagement, and customer satisfaction levels. These metrics provide insights into the effectiveness of lean practices and their impact on overall performance.
What Challenges Might Companies Face When Implementing Lean Principles?
Some common challenges that companies may face when implementing lean principles include resistance to change, lack of employee buy-in, inadequate training, difficulties in sustaining improvements, cultural barriers, and the need for ongoing commitment from leadership. Overcoming these challenges requires perseverance, communication, and a strong organizational culture conducive to continuous improvement.
How Can Employees Be Engaged in Lean Manufacturing Initiatives?
Engaging employees in lean manufacturing initiatives involves fostering a culture of collaboration, providing training and development opportunities, empowering employees to contribute ideas for improvement, recognizing and rewarding efforts, and promoting transparency in communication. Building a team that is invested in the success of lean practices is essential for sustaining long-term improvements.
What Industries Can Benefit from Implementing Lean Manufacturing Principles?
While lean principles originated in the manufacturing sector, industries beyond manufacturing, such as healthcare, services, construction, and software development, can also benefit from implementing lean practices. The concepts of waste reduction, process optimization, and continuous improvement are applicable in various organizational contexts to drive efficiency and performance.
How Does Lean Manufacturing Contribute to Sustainability?
Lean manufacturing contributes to sustainability by reducing waste generation, minimizing energy consumption, optimizing resource utilization, improving process efficiency, and promoting environmental awareness. By aligning with sustainable practices, lean manufacturing not only enhances operational efficiency but also contributes to a more environmentally conscious approach to production.
Resources
Further Resources
For readers interested in delving deeper into lean principles and their practical applications in manufacturing, the following resources provide valuable insights and additional learning opportunities:
- Lean Enterprise Institute: The Lean Enterprise Institute is a leading resource for lean thinking and practices. Their website offers articles, case studies, workshops, and resources to help organizations implement lean methodologies effectively.
- Gemba Academy: Gemba Academy provides online lean and Six Sigma training for individuals and organizations. Their courses cover a wide range of topics, including value stream mapping, 5S, Kaizen, and more.
- Toyota Production System Guide: Explore the official Toyota Production System (TPS) guide to understand the origins and key principles of lean manufacturing as developed by Toyota.
- The Kaizen Institute: The Kaizen Institute specializes in supporting organizations worldwide in implementing lean principles, Kaizen events, and lean management practices. Their site offers resources, training, and case studies for continuous improvement.
- Harvard Business Review - Lean Management: Access articles and insights on lean management from Harvard Business Review, a reputable source for business and management strategies.
- Shingo Institute: The Shingo Institute provides training and certifications in operational excellence, including lean principles, value stream mapping, and continuous improvement practices.
- Lean Six Sigma Institute: For those looking to combine lean principles with Six Sigma methodologies, the Lean Six Sigma Institute offers training programs, certifications, and resources for process improvement.
- IndustryWeek - Lean Manufacturing: IndustryWeek offers insights, articles, and case studies on lean manufacturing practices in diverse industries, providing practical examples and success stories.
These resources serve as excellent guides for professionals seeking to enhance their understanding of lean manufacturing and implement effective strategies for waste reduction and process optimization in their organizations.