Adopting a Lean Mindset: Insights for Aspiring Manufacturing Engineers
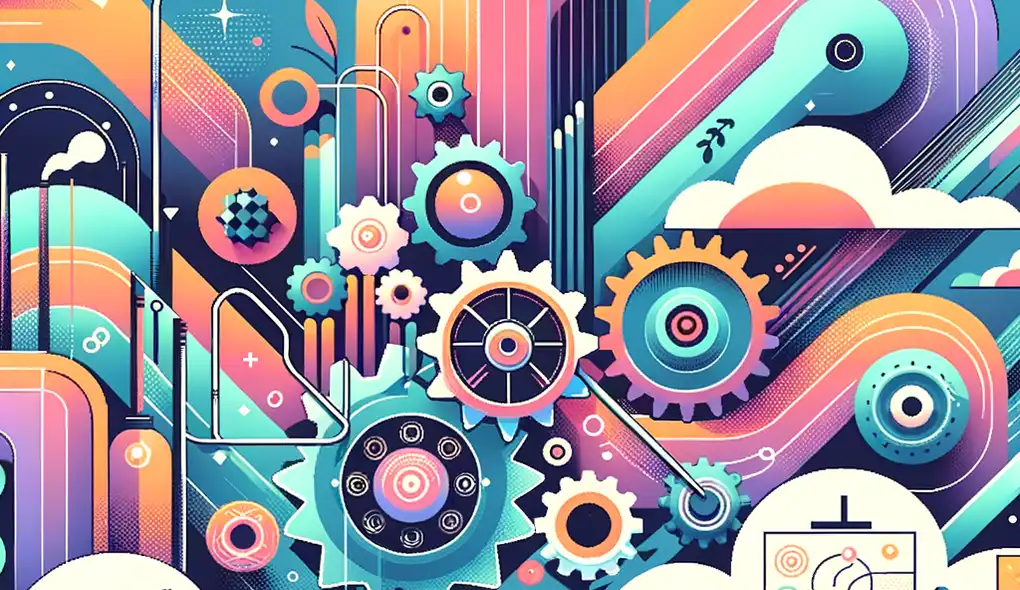
In the world of manufacturing, efficiency, cost reduction, and quality improvement are top priorities. These objectives are often addressed through a methodology known as Lean Manufacturing or Lean Production. Derived from the Toyota Production System, Lean principles have significantly influenced the manufacturing sector since their inception. An aspiring manufacturing engineer must develop a deep understanding of Lean thinking to become instrumental in creating more effective production systems. This article delves into the principles of Lean, explores how it shapes the mindset of successful manufacturing engineers, and provides insights into adopting a Lean mindset to excel in the field.
The Core Principles of Lean Thinking
Lean thinking is underpinned by a few core principles:
Identify Value
The starting point for Lean thinking is to identify what adds value from the customer's perspective. A product or service that does not meet the customer's needs is considered waste. Manufacturing engineers must focus on understanding customer requirements at a granular level and ensuring that every aspect of the manufacturing process is aligned with these needs.
Map the Value Stream
Mapping the value stream involves examining the entire production cycle and identifying every step from raw material to finished product. This analysis enables engineers to spot any non-value-adding activities. Eliminating these 'waste' activities is paramount as they contribute no value to the customer and inflate costs and lead times.
Create Flow
After removing waste, the next step is to ensure that the remaining value-adding steps flow smoothly without interruption. Bottlenecks and interruptions hinder productivity. Manufacturing engineers must design processes to allow for a continuous flow of materials, work-in-progress, and finished goods.
Establish Pull
'Pull' refers to a system where production is based on actual demand rather than forecasting. This just-in-time production approach minimizes inventory waste and streamlines operations. Engineers adopting a Lean mindset learn to implement pull systems effectively, ensuring that resources are conserved and the production is responsive to customer needs.
Seek Perfection
Lean thinking is not a set-and-forget approach; it is a continuous journey toward perfection. ‘Kaizen’ or continuous improvement is an integral part of this journey. Engineers are encouraged to constantly seek ways to reduce waste, streamline processes, and enhance quality, engaging all stakeholders in the improvement efforts.
Shaping the Mindset of the Manufacturing Engineer
Adopting a Lean mindset requires a shift in thought and behavior. For manufacturing engineers, it means:
- Valuing Simplicity: Complexity often hides inefficiencies. Lean thinking values simplicity and clarity in processes.
- Systematic Problem-Solving: Engineers with a Lean mindset approach problems systematically, using tools like root cause analysis to eliminate issues at their source.
- Fostering Collaboration: Recognizing that improvement ideas can come from anywhere, Lean-minded engineers promote teamwork and open communication.
- Being Adaptable to Change: Change is an inherent part of Lean. Engineers must be flexible and willing to implement new methods when required.
- Focusing on the Big Picture: While details are important, Lean engineering requires a broad view of the system to ensure that local optimizations don't detriment the overall flow.
- Taking Ownership of Results: A Lean mindset means being accountable for outcomes, whether it’s about quality improvement or cost reduction.
Implementing Lean in Manufacturing Engineering
The practical application of Lean principles involves a suite of tools and techniques. These may include Kanban boards for visual management, 5S for workplace organization, and Six Sigma for process improvement. For engineering graduates entering the field, engaging with these tools during their studies or internships can provide a solid grounding in Lean methods.
To further embed Lean thinking, engineers can:
- Participate in Lean workshops or simulations.
- Work on cross-functional teams to gain perspective on how Lean applies across different departments.
- Mentor and be mentored in Lean philosophies and applications.
- Engage in continuous learning, keeping abreast of new Lean methodologies and technologies.
Conclusion
Lean thinking is not just a set of tools or methodologies; it’s a mindset that once adopted, can lead manufacturing engineers to deliver incredible value to their organizations and customers. For those aspiring to excel in manufacturing engineering, embracing a Lean mindset is indispensable. It equips them with the perspective and skills required to not just participate in, but to actively drive the evolution and efficiency of modern manufacturing environments.
By espousing the principles of Lean, engineers can ensure they are invaluable assets to their teams, problem solvers par excellence, and champions of process optimization. The future of manufacturing relies heavily on the implementation of these Lean strategies, and the engineers who understand and embody this philosophy will undoubtedly be at the forefront of shaping that future.
Frequently Asked Questions
Frequently Asked Questions
1. What is Lean Manufacturing?
Lean Manufacturing is a methodology that focuses on reducing waste and improving efficiency in production processes. It emphasizes delivering value to customers by eliminating non-value-adding activities.
2. How does Lean Manufacturing benefit the manufacturing sector?
Lean Manufacturing helps manufacturing companies reduce costs, improve quality, increase productivity, and respond more effectively to customer demands. It fosters a culture of continuous improvement and optimization.
3. What are the key principles of Lean Thinking?
The core principles of Lean Thinking include identifying value, mapping the value stream, creating flow, establishing pull systems, and seeking perfection through continuous improvement.
4. How can aspiring manufacturing engineers develop a Lean mindset?
Aspiring manufacturing engineers can develop a Lean mindset by valuing simplicity, embracing systematic problem-solving approaches, fostering collaboration, being adaptable to change, focusing on the big picture, and taking ownership of results.
5. What tools and techniques are used in Lean Manufacturing?
Tools and techniques commonly used in Lean Manufacturing include Kanban boards for visual management, 5S for workplace organization, and Six Sigma for process improvement. Engaging with these tools during studies or internships helps in gaining practical experience.
6. How can engineers further enhance their Lean thinking skills?
Engineers can enhance their Lean thinking skills by participating in Lean workshops or simulations, working on cross-functional teams, mentoring and being mentored in Lean philosophies, and engaging in continuous learning to stay updated on new Lean methodologies and technologies.
7. Why is Lean thinking essential for the future of manufacturing engineering?
Lean thinking is crucial for the future of manufacturing engineering as it drives efficiency, innovation, and adaptability in production processes. Engineers with a Lean mindset are well-equipped to lead the evolution of modern manufacturing environments.
8. How can Lean strategies contribute to a manufacturing engineer's success?
Embracing Lean strategies can make manufacturing engineers invaluable assets to their teams by enabling them to solve problems effectively, optimize processes, and deliver significant value to their organizations and customers.
Resources
Further Resources
For individuals interested in diving deeper into Lean Manufacturing and enhancing their understanding of Lean principles, there are a wealth of resources available to explore. Whether you are an aspiring manufacturing engineer looking to sharpen your skills or a seasoned professional seeking to stay updated with the latest trends in Lean thinking, these resources can offer valuable insights and guidance.
Books
- Lean Thinking: Banish Waste and Create Wealth in Your Corporation by James P. Womack and Daniel T. Jones - This foundational book explores the core principles of Lean thinking and provides a roadmap for implementing Lean practices in various industries.
- The Toyota Way: 14 Management Principles from the World's Greatest Manufacturer by Jeffrey K. Liker - Delve into the philosophy and management principles that have driven Toyota's success and shaped Lean Manufacturing.
- Creating a Lean Culture: Tools to Sustain Lean Conversions by David Mann - Learn how to foster a culture of continuous improvement and sustain Lean transformations within organizations.
Online Courses
- Lean Manufacturing Foundations on LinkedIn Learning - This comprehensive course covers the basics of Lean Manufacturing and how to apply Lean principles to enhance efficiencies.
- Six Sigma and Lean: Quantitative Tools for Quality and Productivity on Coursera - Explore the intersection of Lean and Six Sigma methodologies to drive quality and productivity improvements.
- Gemba Academy - A platform offering a range of Lean and Six Sigma training courses, webinars, and resources for continuous learning.
Tools and Software
- Trello - A popular project management tool that can be used to implement Kanban boards for visualizing workflow and managing tasks in a Lean environment.
- Minitab - Statistical software commonly used for data analysis and process improvement in Lean and Six Sigma projects.
- LeanKit - A digital Kanban tool designed to facilitate Lean project management and streamline workflows.
Organizations and Associations
- Lean Enterprise Institute - A nonprofit organization dedicated to advancing Lean principles and practices across industries through research, education, and networking.
- Association for Manufacturing Excellence (AME) - An organization focused on promoting operational excellence and continuous improvement in manufacturing through Lean methodologies.
- Institute of Industrial and Systems Engineers (IISE) - A professional association that offers resources and networking opportunities for industrial engineers involved in Lean Manufacturing.
By exploring these resources, individuals can deepen their knowledge of Lean principles, gain practical insights into Lean implementation, and stay informed about the latest developments in Lean Manufacturing practices.