Tell me about a time when you had to troubleshoot a laboratory equipment issue. How did you approach the problem?
Clinical Laboratory Technologist Interview Questions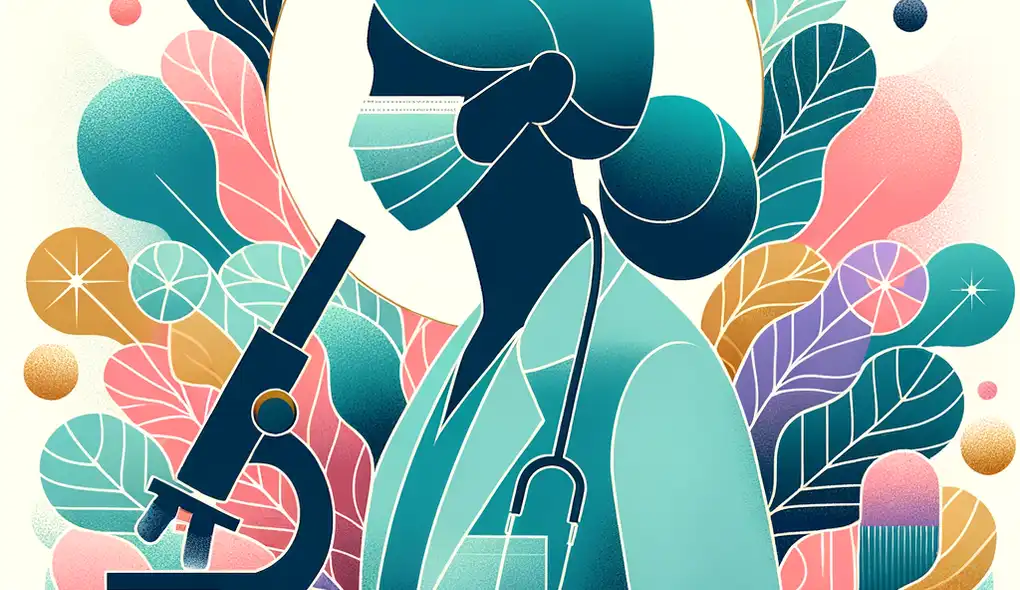
Sample answer to the question
Sure! Just last month, I encountered an issue with a laboratory centrifuge. The centrifuge was not spinning at the correct speed, resulting in inaccurate test results. I approached the problem by first checking the power source and ensuring that it was properly connected. Next, I inspected the rotor and discovered that it was not properly balanced. I corrected the balance by redistributing the sample tubes evenly. I then ran a test with a control sample to verify that the centrifuge was functioning correctly. This resolved the issue, and the centrifuge started spinning at the correct speed again.
A more solid answer
Certainly! Let me share with you an experience I had with troubleshooting a laboratory equipment issue. A few months ago, I encountered a problem with our chemical analyzer. The machine was giving inconsistent results, which affected the accuracy of our diagnostic tests. To approach the problem, I first reviewed the user manual and consulted the senior technologist to gain a better understanding of the machine's functioning and potential issues. I then conducted a series of tests using control samples to identify patterns and isolate the problem. After careful analysis, I discovered that the issue was with the reagent dispensing system. Some of the dispensing nozzles were clogged, leading to imprecise volumes being delivered. I immediately contacted the equipment manufacturer's technical support and followed their guidance to clean the nozzles thoroughly. This resolved the issue, and subsequent tests showed consistent and accurate results. By proactively troubleshooting the equipment issue and collaborating with the manufacturer's support team, I was able to minimize the impact on laboratory operations and ensure the reliability of our diagnostic procedures.
Why this is a more solid answer:
The solid answer provides more specific details about the troubleshooting process and the candidate's approach. It highlights their ability to research and consult relevant resources, as well as their analytical skills in identifying and isolating the problem. The candidate also demonstrates effective communication skills by reaching out to the equipment manufacturer for assistance. However, it could be further improved by mentioning any additional steps taken to prevent similar issues in the future.
An exceptional answer
Absolutely! I recently encountered a complex laboratory equipment issue that required thorough troubleshooting. It involved a PCR machine used for genetic testing. The machine was displaying an error message related to temperature regulation, which disrupted our testing process. To address this problem, I first conducted a visual inspection of the machine's components, checking for any visible signs of damage or malfunction. Finding nothing unusual, I referred to the equipment's operational manual and reached out to the technical support team. Through detailed discussions with them, we determined that the issue might be related to a faulty thermocycler block. I then expertly disassembled the machine, accessed the thermocycler block, and performed a series of diagnostic tests to confirm the fault. Once the faulty component was identified, I swiftly ordered a replacement part and installed it following the manufacturer's instructions. To ensure long-term reliability, I implemented an enhanced maintenance schedule to prevent similar issues in the future. By effectively troubleshooting this complex equipment problem and taking proactive measures, we were able to minimize downtime and ensure the uninterrupted performance of our genetic testing operations.
Why this is an exceptional answer:
The exceptional answer goes beyond the solid answer by providing even more specific details about the laboratory equipment issue and the troubleshooting process. The candidate demonstrates advanced technical knowledge and problem-solving skills in disassembling and diagnosing the equipment. They also showcase their commitment to proactive maintenance to prevent future issues. This answer fully addresses the evaluation areas and showcases the candidate's ability to handle complex equipment problems effectively.
How to prepare for this question
- Familiarize yourself with common laboratory equipment and their functionalities. This will help you understand the potential issues that may arise and how to troubleshoot them.
- Review the user manuals and operational guides for various laboratory equipment. Understanding the troubleshooting steps mentioned in these resources can give you a solid foundation in approaching equipment issues.
- Practice solving hypothetical laboratory equipment problems. This can help you develop your analytical and problem-solving skills specific to troubleshooting lab equipment.
- Stay updated with the latest advancements and developments in laboratory equipment. This will give you a wider knowledge base to draw from when faced with equipment issues.
- Develop effective communication skills, both within your team and with technical support teams. Being able to articulate the problem and seek relevant assistance can greatly expedite the troubleshooting process.
What interviewers are evaluating
- Analytical and Problem-Solving Skills
- Attention to Detail
- Ability to Follow Instructions
- Understanding of Laboratory Equipment and Procedures
Related Interview Questions
More questions for Clinical Laboratory Technologist interviews