Key Skills Every Industrial Chemicals Coordinator Should Master
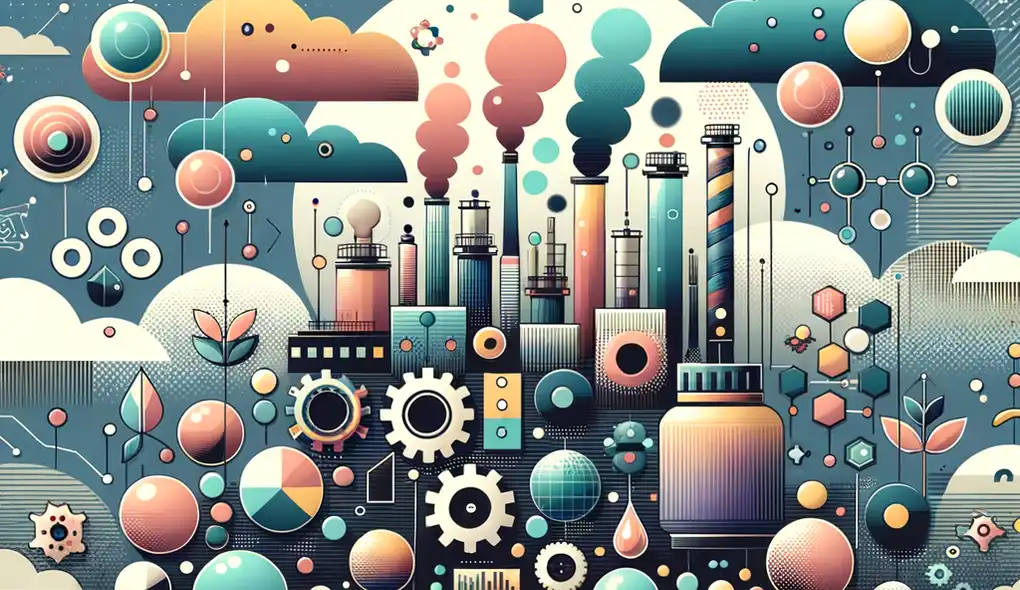
The role of an Industrial Chemicals Coordinator is fundamentally pivotal in the realm of chemical manufacturing and distribution. This dynamic and sometimes challenging position requires a professional who not only understands the complex nature of handling and coordinating chemicals but also possesses a diverse skill set that spans technical know-how, regulatory compliance, safety management, logistical coordination, and communication prowess. In this article, we'll explore the key skills every Industrial Chemicals Coordinator should master to succeed in this critical role within the industrial chemicals sector.
1. In-depth Knowledge of Chemical Properties and Processes
Proficiency in chemistry is the cornerstone of an effective Chemicals Coordinator. Understanding the physical and chemical properties of various substances, as well as their reactions and compatibilities, is crucial. Coordination involves the safe and efficient handling, storage, and transportation of chemicals, which requires a thorough knowledge of chemical processes. These professionals must also be abreast with the newest advancements and technologies in chemical production and be adept at applying this knowledge in practical scenarios.
2. Regulatory Compliance and Safety Standards Expertise
Given the potential hazards associated with industrial chemicals, coordinators must be experts on relevant laws and regulations. Mastery of safety standards and protocols such as the Occupational Safety and Health Administration (OSHA), the Environmental Protection Agency (EPA), and global regulations like REACH and GHS is essential. They must stay updated with the changing regulatory landscape to ensure company practices are compliant and to protect worker health and environmental safety.
3. Logistical and Operational Coordination Abilities
Industrial Chemicals Coordinators are responsible for the smooth flow of materials from one point to another. They need to have strong logistical skills, including inventory management, supply chain coordination, and the ability to troubleshoot any operational bottlenecks. The ability to forecast demand and ensure that inventory levels are maintained is crucial in avoiding production delays or excess inventory.
4. Strong Attention to Detail
Attention to detail is a non-negotiable trait for coordinators. Mistakes in this field can have major consequences, so being meticulous is necessary. This involves careful oversight of chemical labeling, documentation, and ensuring that protocols are meticulously followed at each stage of the coordination process.
5. Effective Communication and Interpersonal Skills
Success in this role also depends heavily on the ability to communicate effectively with individuals at all levels - from laboratory technicians to high-level management. Coordinators must convey complex information in understandable terms, lead teams, resolve conflicts, and liaise between different departments or organizations. Interpersonal skills are also crucial for building relationships with suppliers and customers.
6. Problem-Solving and Decision-Making Capabilities
A Chemicals Coordinator must be adept at problem-solving. This includes the capacity to identify issues promptly and develop practical solutions when unexpected challenges arise, such as supply disruption or a safety incident. Being able to make critical decisions under pressure is vital to mitigate risks and maintain operations.
7. Technological Proficiency
Today's industrial landscape is driven by technology, so coordinators should be proficient with the various tools and software used for chemical management, data analysis, and logistical tracking. Understanding how to leverage technological advancements can increase efficiency and accuracy in managing the chemical supply chain.
8. Project Management Skills
Coordinators often take on projects that require planning, scheduling, budgeting, and overseeing project delivery. The ability to manage projects from start to finish, ensuring deadlines are met and objectives are achieved, is fundamental. Knowledge of project management methodologies and tools can enhance effectiveness in this area.
9. Flexibility and Adaptability
The industrial chemicals sector is fast-paced and constantly evolving. Coordinators need to be flexible and adaptable to accommodate changing conditions and technological advancements. This could mean adapting to new regulatory requirements, adjusting to market demands, or altering processes based on new scientific data.
10. Leadership and Team Building
Lastly, strong leadership qualities are necessary for coordinators who oversee teams or entire departments. This means fostering a positive work environment, motivating staff, and enlisting the cooperation and respect of peers and subordinates alike. Developing team building skills can help create a cohesive unit that is efficient, knowledgeable, and safety-conscious.
These ten skills form the basis of a robust competency framework for Industrial Chemicals Coordinators. By mastering these areas, professionals can ensure the safe, efficient, and compliant operations of chemical manufacturing and distribution processes, contributing to the success of the company and the safety of its employees and the public. It's clear that a career as an Industrial Chemicals Coordinator is neither for the faint of heart nor the skill-deficient; it is a career that rewards precision, foresight, and ongoing personal and professional development.
Frequently Asked Questions
Frequently Asked Questions
1. What qualifications are required to become an Industrial Chemicals Coordinator?
To become an Industrial Chemicals Coordinator, a minimum of a bachelor's degree in chemistry, chemical engineering, or a related field is typically required. Additionally, relevant certifications in safety management, regulatory compliance, and project management can enhance your credentials for this role.
2. How important is regulatory compliance in the role of an Industrial Chemicals Coordinator?
Regulatory compliance is paramount in the role of an Industrial Chemicals Coordinator due to the potential hazards associated with industrial chemicals. Ensuring adherence to laws and safety standards such as OSHA, EPA, REACH, and GHS is crucial to maintain the safety of personnel and the environment.
3. What are the typical daily responsibilities of an Industrial Chemicals Coordinator?
Daily responsibilities may include overseeing chemical inventory, coordinating shipments and deliveries, ensuring safety protocols are followed, maintaining regulatory compliance, communicating with suppliers and internal teams, and troubleshooting operational issues to ensure smooth production processes.
4. How can Industrial Chemicals Coordinators stay updated with industry advancements?
Industrial Chemicals Coordinators can stay updated with industry advancements by attending conferences, participating in relevant training programs, subscribing to industry publications, networking with professionals in the field, and continuously seeking professional development opportunities.
5. What are the career advancement opportunities for Industrial Chemicals Coordinators?
Career advancement opportunities for Industrial Chemicals Coordinators may include progressing to higher-level managerial roles, specializing in a specific area of chemical coordination, transitioning to roles in regulatory affairs or environmental health and safety, or pursuing consulting opportunities in the industry.