What steps do you take to troubleshoot and resolve issues with sterilization equipment?
Sterile Processing Tech Interview Questions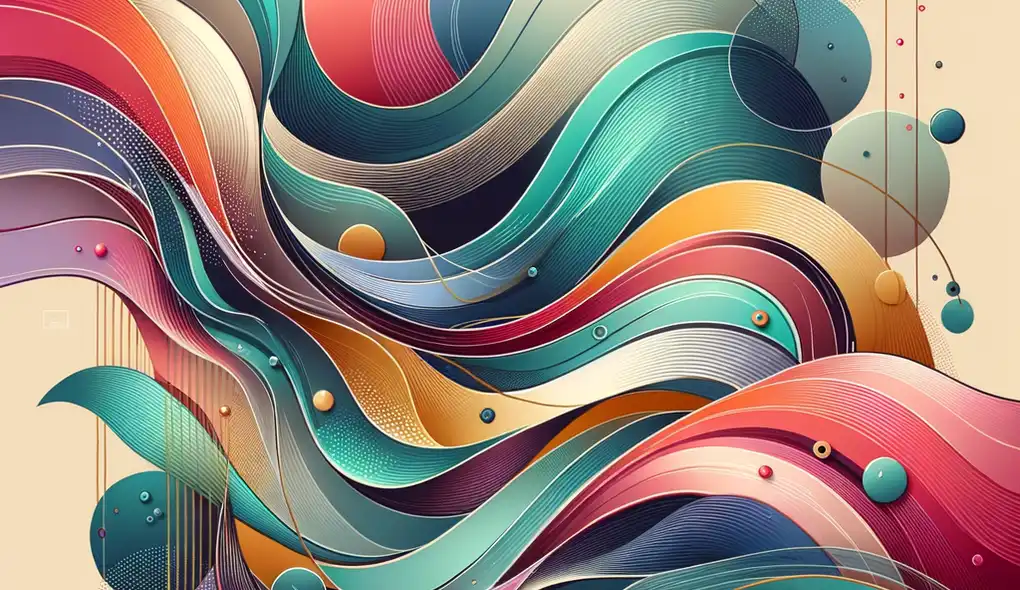
Sample answer to the question
When troubleshooting and resolving issues with sterilization equipment, I follow a systematic approach. First, I identify the problem by observing any error messages or abnormal behavior. Then, I check the equipment's settings and compare them to the manufacturer's recommendations. If needed, I consult the equipment manual or contact the manufacturer for guidance. I also perform basic maintenance tasks like cleaning filters and ensuring proper ventilation. In case the issue persists, I escalate it to my supervisor or the maintenance team for further investigation and repairs.
A more solid answer
When troubleshooting and resolving issues with sterilization equipment, I take several steps to ensure efficient resolution. First, I carefully observe the equipment for any error messages or unusual behavior, paying close attention to details. Then, I refer to the equipment's manual to identify the recommended settings and compare them to the current settings. If necessary, I perform basic maintenance tasks like cleaning filters and checking ventilation. Additionally, I consult with my colleagues who have expertise in equipment troubleshooting for their insights and suggestions. In case the issue persists, I escalate it to my supervisor or the maintenance team, providing them with a detailed report of the problem, steps taken, and any relevant observations. By following this systematic approach and maintaining clear communication, I have successfully resolved various issues with sterilization equipment in the past.
Why this is a more solid answer:
The solid answer provides a more comprehensive explanation of the steps taken to troubleshoot and resolve issues with sterilization equipment. It includes specific details such as observing error messages, referring to the equipment manual, performing basic maintenance tasks, consulting colleagues, and escalating the issue with a detailed report. This answer demonstrates the candidate's attention to detail, technical aptitude, problem-solving skills, communication skills, and organizational skills. However, it can be further improved by providing specific examples of past experiences in troubleshooting and resolving issues with sterilization equipment.
An exceptional answer
Troubleshooting and resolving issues with sterilization equipment is a critical task that requires a systematic and comprehensive approach. When faced with an issue, I first gather all the necessary information, including equipment logs, error messages, and observations. I analyze the data to identify common patterns or potential causes of the problem. Based on my analysis, I develop a troubleshooting plan that includes specific steps and procedures tailored to the equipment at hand. For example, if the issue is related to inconsistent sterilization cycles, I might check the water quality, review the maintenance records, and calibrate the equipment if needed. Throughout the troubleshooting process, I maintain detailed documentation of my actions, noting any changes made and their impact. If necessary, I collaborate with the maintenance team or contact the equipment manufacturer for specialized guidance. Once the issue is resolved, I conduct follow-up tests and observations to ensure the equipment operates correctly and meets the required standards. By following these comprehensive steps and leveraging my attention to detail, technical aptitude, problem-solving abilities, communication skills, and organizational skills, I have successfully resolved various issues with sterilization equipment, contributing to the efficient and safe operation of healthcare facilities.
Why this is an exceptional answer:
The exceptional answer goes above and beyond the solid answer by providing a more detailed and thorough explanation of the steps taken to troubleshoot and resolve issues with sterilization equipment. It includes additional elements such as gathering information, analyzing data, developing a tailored troubleshooting plan, maintaining documentation, collaborating with the maintenance team or manufacturer, conducting follow-up tests, and ensuring compliance with standards. This answer demonstrates the candidate's exceptional attention to detail, technical aptitude, problem-solving skills, communication skills, and organizational skills. It also showcases their ability to adapt and apply their knowledge and experience to resolve complex issues. The addition of specific examples would further enhance the answer.
How to prepare for this question
- Familiarize yourself with the different types of sterilization equipment commonly used in healthcare settings, such as autoclaves, sonic washers, and sterilizer machines.
- Review the basics of equipment troubleshooting, including common issues and their potential causes.
- Stay updated on the latest guidelines and best practices for sterilization and infection control.
- Practice documenting your troubleshooting steps and observations in a clear and organized manner.
- Consider examples from your past experience where you successfully resolved issues with sterilization equipment and be prepared to discuss them during the interview.
What interviewers are evaluating
- Attention to detail
- Technical aptitude
- Problem-solving
- Communication
- Organizational skills
Related Interview Questions
More questions for Sterile Processing Tech interviews