Overcoming Challenges in Product Quality Management: Strategies for Success
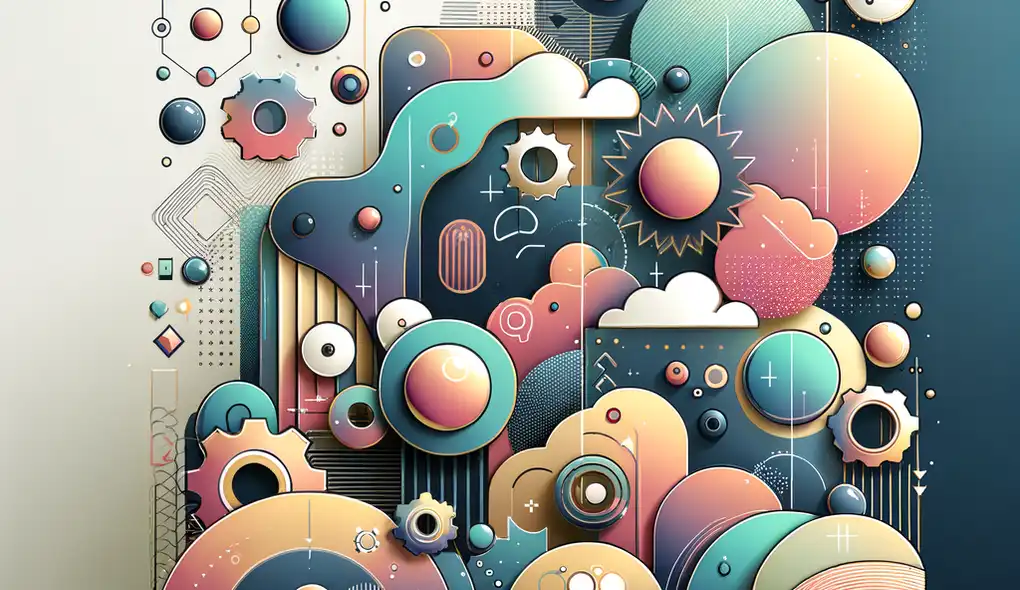
In the dynamic and competitive landscape of today’s business world, the importance of maintaining high product quality cannot be overstated. As organizations strive for efficiency and customer satisfaction, the role of Product Quality Managers becomes increasingly critical. However, this role comes with its own set of challenges, which if not effectively managed, can result in subpar products, diminished brand reputation, and financial losses. In this article, we will explore the common obstacles faced by Product Quality Managers and provide strategies for overcoming these challenges to thrive in the role.
Identifying and Understanding Common Challenges
The first step to effectively managing product quality is to recognize and understand the common obstacles that may arise. Here are some of the challenges that Product Quality Managers often encounter:
- Rapidly Changing Consumer Expectations: In a market driven by trends and innovation, consumer expectations are constantly evolving. Product Quality Managers must continuously adapt to these changes to ensure that products meet or exceed customer standards.
- Compliance with Regulatory Standards: Compliance with industry standards and regulatory requirements can be complex and time-consuming. Navigating through these regulations to ensure product quality is essential but challenging.
- Supplier and Vendor Management: Ensuring the quality of materials and components sourced from third parties is critical. However, managing multiple suppliers and their varying standards of quality presents a substantial challenge.
- Cross-Functional Collaboration: Quality management is not the sole responsibility of the quality department. Collaborating with other departments (R&D, production, marketing) while maintaining quality standards is a complex task that requires strong communication and coordination skills.
- Technological Adaptation: Integrating new technologies for quality management, such as automation and data analytics tools, while ensuring that staff are properly trained, can be a daunting task.
- Dealing with Defects and Improving Processes: Identifying defects, understanding their root causes, and improving processes to prevent them from recurring requires expertise and a systematic approach.
Strategies for Overcoming Challenges
After identifying the challenges, the following strategies will help in overcoming them and leading to successful product quality management:
- Embrace Continuous Improvement: Quality managers must promote a culture of continuous improvement where feedback is actively sought and acted upon. Utilizing methodologies like Six Sigma or Lean principles can aid in minimizing defects and optimizing processes.
- Stay Current with Market Trends: By keeping abreast of consumer trends and expectations, quality managers can anticipate changes and adapt products accordingly. Engaging in continuous learning and research is vital to staying ahead.
- Ensure Compliance: Establish comprehensive systems to regularly monitor and ensure compliance with all relevant regulations. Invest in training for team members to remain informed about these requirements.
- Strengthen Supplier Relationships: Building strong relationships with suppliers and conducting regular audits can ensure consistent quality of materials and components. Clear communication about quality expectations is necessary.
- Foster Team Collaboration: Encourage cross-departmental dialogue and cooperation to ensure quality is a shared responsibility. Regular meetings and integrated systems can help maintain alignment across different departments.
- Leverage Technology: Adopt advanced quality management systems and technologies that can provide insights through data analytics and improve efficiency through automation. Ensure staff are trained and comfortable with these technologies.
- Implement Effective Root Cause Analysis: Invest in training for problem-solving and root cause analysis techniques. Having a structured approach to identifying and addressing defects can prevent repeat issues and improve overall product quality.
- Handle Defects Proactively: Set up processes that allow for timely identification and resolution of defects. Taking a proactive stance on dealing with quality issues can minimize the impact on customers and the business.
Conclusion
Overcoming the challenges in product quality management requires a strategic approach, effective communication, and a commitment to continuous improvement. By applying these strategies, Product Quality Managers can navigate the obstacles they face and contribute significantly to their organization’s success. The role is challenging but also rewarding, as high-quality products lead to satisfied customers and a strong market position.
- Rapidly Changing Consumer Expectations: In a market driven by trends and innovation, consumer expectations are constantly evolving. Product Quality Managers must continuously adapt to these changes to ensure that products meet or exceed customer standards.
- Compliance with Regulatory Standards: Compliance with industry standards and regulatory requirements can be complex and time-consuming. Navigating through these regulations to ensure product quality is essential but challenging.
- Supplier and Vendor Management: Ensuring the quality of materials and components sourced from third parties is critical. However, managing multiple suppliers and their varying standards of quality presents a substantial challenge.
- Cross-Functional Collaboration: Quality management is not the sole responsibility of the quality department. Collaborating with other departments (R&D, production, marketing) while maintaining quality standards is a complex task that requires strong communication and coordination skills.
- Technological Adaptation: Integrating new technologies for quality management, such as automation and data analytics tools, while ensuring that staff are properly trained, can be a daunting task.
- Dealing with Defects and Improving Processes: Identifying defects, understanding their root causes, and improving processes to prevent them from recurring requires expertise and a systematic approach.
Strategies for Overcoming Challenges
After identifying the challenges, the following strategies will help in overcoming them and leading to successful product quality management:
- Embrace Continuous Improvement: Quality managers must promote a culture of continuous improvement where feedback is actively sought and acted upon. Utilizing methodologies like Six Sigma or Lean principles can aid in minimizing defects and optimizing processes.
- Stay Current with Market Trends: By keeping abreast of consumer trends and expectations, quality managers can anticipate changes and adapt products accordingly. Engaging in continuous learning and research is vital to staying ahead.
- Ensure Compliance: Establish comprehensive systems to regularly monitor and ensure compliance with all relevant regulations. Invest in training for team members to remain informed about these requirements.
- Strengthen Supplier Relationships: Building strong relationships with suppliers and conducting regular audits can ensure consistent quality of materials and components. Clear communication about quality expectations is necessary.
- Foster Team Collaboration: Encourage cross-departmental dialogue and cooperation to ensure quality is a shared responsibility. Regular meetings and integrated systems can help maintain alignment across different departments.
- Leverage Technology: Adopt advanced quality management systems and technologies that can provide insights through data analytics and improve efficiency through automation. Ensure staff are trained and comfortable with these technologies.
- Implement Effective Root Cause Analysis: Invest in training for problem-solving and root cause analysis techniques. Having a structured approach to identifying and addressing defects can prevent repeat issues and improve overall product quality.
- Handle Defects Proactively: Set up processes that allow for timely identification and resolution of defects. Taking a proactive stance on dealing with quality issues can minimize the impact on customers and the business.
Conclusion
Overcoming the challenges in product quality management requires a strategic approach, effective communication, and a commitment to continuous improvement. By applying these strategies, Product Quality Managers can navigate the obstacles they face and contribute significantly to their organization’s success. The role is challenging but also rewarding, as high-quality products lead to satisfied customers and a strong market position.
Frequently Asked Questions
Frequently Asked Questions
Q: What qualifications are necessary to become a Product Quality Manager?
A: Qualifications for a Product Quality Manager typically include a bachelor's degree in a relevant field such as engineering, quality management, or business administration. Additionally, certifications such as Six Sigma or Quality Management are advantageous. Experience in quality control, supplier management, and process improvement is also valuable.
Q: How can Product Quality Managers ensure compliance with changing regulatory standards?
A: Product Quality Managers can stay up-to-date with regulatory changes by actively engaging in industry associations, attending conferences, and subscribing to regulatory update services. Establishing a systematic approach to monitoring and implementing changes, conducting regular audits, and providing team training on new regulations are effective strategies.
Q: What are some effective methods for managing supplier relationships?
A: Building strong supplier relationships involves clear communication of quality expectations, regular performance evaluations, and conducting on-site audits. Implementing supplier quality agreements, setting clear standards, and collaborating on continuous improvement initiatives can foster long-term partnerships.
Q: How important is technological adoption in product quality management?
A: Technological adoption is crucial in modern product quality management. Advanced quality management systems and tools enhance efficiency, enable data-driven decision-making, and facilitate continuous improvement. Training staff on new technologies ensures effective implementation and utilization.
Q: What role does cross-functional collaboration play in maintaining product quality?
A: Cross-functional collaboration is essential for maintaining product quality as it involves coordinating efforts across departments like R&D, production, and marketing. Ensuring clear communication, shared accountability, and integrated systems promote alignment and consistency in quality standards.
Q: How can Product Quality Managers handle defects and prevent their recurrence?
A: Product Quality Managers can handle defects by implementing robust root cause analysis techniques, establishing corrective and preventive action plans, and fostering a culture of continuous improvement. By identifying underlying causes and implementing systemic changes, they can prevent defects from recurring.
Q: What are the benefits of investing in training for quality improvement?
A: Investing in training for quality improvement enhances team skills, fosters a culture of quality consciousness, and promotes adherence to best practices. Well-trained staff are better equipped to identify issues, implement preventive measures, and contribute to overall product quality.
For more in-depth insights and resources on product quality management, check out the following recommended articles and websites:
- Quality Management Magazine
- American Society for Quality (ASQ) - Product Quality
- Lean Six Sigma Institute - Certification and Training
Explore these resources to deepen your knowledge and stay informed about the latest trends and best practices in product quality management.
Resources
Further Resources
For further exploration and enhancement of your understanding of product quality management and the strategies mentioned in this article, here are some valuable resources:
- Books:
- The Lean Six Sigma Pocket Toolbook: A Quick Reference Guide to Nearly 100 Tools for Improving Quality and Speed by Michael L. George
- Quality Management for Organizational Excellence: Introduction to Total Quality by David L. Goetsch and Stanley Davis
- Online Courses:
- Coursera offers courses like Six Sigma Green Belt Certification and Quality Engineering and Management
- Udemy provides courses on Quality Management Basics and Root Cause Analysis
- Websites and Portals:
- ASQ (American Society for Quality) - A valuable resource for quality professionals with articles, webinars, and certification programs
- Quality Digest - An online resource for quality management news, articles, and insights
- Associations and Forums:
- Join the American Society for Quality (ASQ) to connect with quality management professionals and access industry resources
- Participate in quality management forums like iSixSigma for discussions, best practices, and networking opportunities
- Tools and Software:
- Invest in quality management tools like Minitab, JMP, and QI Macros for statistical analysis and process improvement
- Utilize software systems like SAP QM and MasterControl for streamlining quality processes and documentation
- Podcasts and Webinars:
- Tune in to podcasts like Quality Matters and Quality Digest for industry insights and discussions on quality management
- Attend webinars by ASQ and other quality organizations to stay updated on the latest trends and practices in quality management
- Case Studies and Whitepapers:
- Explore case studies on successful quality management implementations in various industries to learn from real-world examples
- Access whitepapers from quality management experts and organizations for in-depth analysis and thought leadership