The Future of Welding Jobs: Trends and Predictions
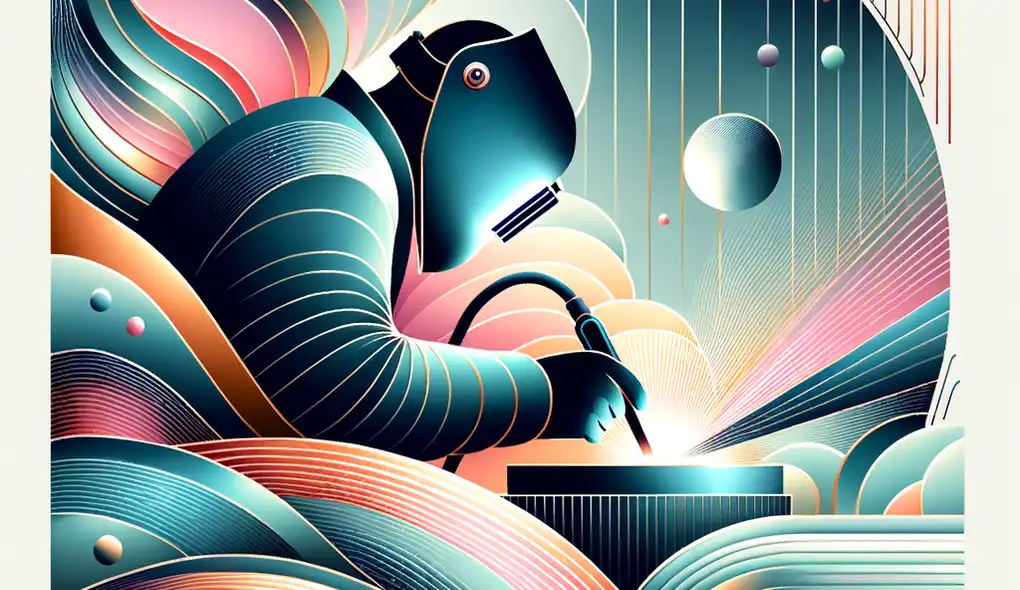
The field of welding has long been recognized as a cornerstone of industrial work, critical to the construction of everything from cars and ships to bridges and buildings. However, as technology progresses and industries evolve, the future of welding jobs is poised to undergo significant changes. This article examines the current trends and forecasts that are shaping the welding profession, offering insights into what future job prospects might look like for Welding Technicians.
Technological Advancements
The wave of technological innovation is reshaping the welding industry. Advancements such as automation and robotics are now integral parts of manufacturing and construction, and these technologies are altering the landscape for welders. The implementation of automated welding systems can perform repetitive tasks with precision over extended periods, potentially reducing the demand for manual welders. However, this doesn't necessarily spell the end for welding jobs. Instead, it highlights a shift where the role of the welding technician becomes more technical, with a focus on programming, operating, and maintaining automated systems.
In addition, new welding techniques and materials are being developed, such as laser welding and friction stir welding, creating niches that require specialized skills. Processing of advanced materials like high-strength steel and aluminum alloys in aerospace and automotive applications demands welders who are proficient with these new methods. Skilled technicians who can adapt to these advanced techniques will find themselves highly sought after in the job market.
Emerging Industries
Emerging industries, particularly in renewable energy sectors such as solar and wind power, are also creating new opportunities for welders. These industries require durable, high-quality welds to ensure the longevity and safety of their infrastructure. As the world continues to shift towards sustainable energy solutions, welders with the skills to work on these projects will enjoy growing demand.
Additionally, advancements in the maritime sector, including the development of new shipping technologies and underwater welding for repair and maintenance of offshore structures, offer fresh horizons for technical diversification in welding careers.
The Push for Education and Certification
There is an increasing emphasis on the importance of professional education and certification in the welding industry. Employers are looking for candidates who not only have the hands-on experience but also possess a strong theoretical understanding of metallurgy, physics, and engineering principles. Vocational schools, community colleges, and industry-sponsored programs have updated their curricula to encompass the latest technologies and safety standards, thus empowering the next generation of welding professionals with the knowledge they need.
Moreover, certifications from recognized bodies such as the American Welding Society (AWS) are becoming prerequisites for many welding positions. These certifications evidence a welder's skill level and commitment to quality, further enhancing job prospects.
The Role of Soft Skills
Soft skills, those interpersonal and cognitive abilities that allow individuals to effectively navigate their environment, work well with others, solve problems, and lead, are becoming increasingly important for welders. As team collaboration becomes more integrated with welding projects, particularly in complex fields like aerospace and construction, strong communication and teamwork skills are crucial.
Leadership ability and project management skills are also in demand, as technicians often need to supervise teams, manage resources, and ensure projects adhere to timelines and budgets. In the future, welders will not only be evaluated on their technical capabilities but also on their soft skills.
Safety and Sustainability
Within the sphere of welding, the focus on safety has never been higher. Improved safety equipment, stricter regulations, and better training are all contributing to safer workplaces. Welders proficient in current safety practices have an edge in the job market.
Alongside safety, sustainability efforts are influencing the field as companies seek to minimize their environmental footprint. Techniques that reduce waste, energy consumption, and hazardous material use are favored, and welders acquainted with these practices will be competitive job contenders.
Conclusion
As we look to the future, welding jobs are evolving to meet the challenges and opportunities of a changing world. Technology will continue to redefine the skills needed by welding technicians, but rather than replacing human workers, these changes will augment the role of the welder. Those who embrace lifelong learning, adapting to new tools, techniques, and standards, can look forward to a robust and rewarding career. Emerging sectors, combined with a focus on safety and sustainability, are creating a dynamic environment for welding professionals who are prepared to grow with the industry and lead its progression into the future.
Frequently Asked Questions
Frequently Asked Questions
Q: What are the key technological advancements impacting the future of welding jobs?
A: Technological advancements such as automation, robotics, laser welding, and friction stir welding are significantly reshaping the welding industry. Automation and robotics are reducing the demand for manual welders but are also creating opportunities for welders to specialize in programming and operating automated systems. New welding techniques and materials require welders to adapt and acquire specialized skills to remain competitive in the job market.
Q: Which emerging industries are creating new opportunities for welders?
A: Emerging industries, particularly in renewable energy sectors like solar and wind power, as well as advancements in the maritime sector, offer new opportunities for welders. The demand for durable, high-quality welds in renewable energy projects and the need for underwater welding in maritime developments present growing job prospects for welders with the right skills.
Q: How important is professional education and certification in the welding industry?
A: Professional education and certification are increasingly important in the welding industry. Employers seek candidates with a solid theoretical understanding of metallurgy, physics, and engineering principles along with hands-on experience. Certifications from recognized bodies like the American Welding Society (AWS) have become prerequisites for many welding positions, demonstrating a welder's competency and commitment to quality.
Q: What role do soft skills play in the future of welding jobs?
A: Soft skills such as communication, teamwork, leadership, and project management are becoming more crucial for welders as team collaboration in welding projects becomes common. Welders are evaluated not only on their technical abilities but also on their interpersonal and cognitive skills. Strong communication and leadership skills are essential for success in complex welding projects.
Q: How are safety and sustainability trends influencing the welding industry?
A: Safety standards are continuously improving in the welding industry to create safer workplaces for welders. Compliance with safety regulations and proficiency in safety practices are essential for job seekers. Sustainability efforts, including waste reduction, energy efficiency, and environmentally-friendly practices, are also shaping the field of welding. Welders who are knowledgeable about sustainable welding techniques will have a competitive edge in the job market.
Resources
Further Resources
For further exploration into the future of welding jobs and how to stay competitive in the evolving industry, the following resources provide valuable insights and opportunities for professional growth:
- American Welding Society (AWS): The AWS offers a wide range of certification programs, educational resources, and industry updates to enhance your welding career.
- The Fabricator: Stay updated with the latest news, articles, and trends in welding and metal fabrication through The Fabricator's comprehensive coverage.
- Welding Journal: Access a wealth of research articles, technical papers, and industry developments in welding by subscribing to the Welding Journal.
- Miller Welds Resources: Explore welding tips, welding projects, and product information to improve your skills and knowledge in the welding field.
- Lincoln Electric Education Resources: Lincoln Electric provides welding education resources, virtual reality welding simulation, and training materials for students and professionals.
- O*NET Online - Welders, Cutters, Solderers, and Brazers: Understand the occupational outlook, job duties, and required skills for welders through the detailed information provided by O*NET Online.
- National Center for Construction Education & Research (NCCER): Enhance your construction craft skills, including welding, through accredited training programs and certifications offered by NCCER.
- AWS WeldLink: Network with industry professionals, explore job opportunities, and access career development resources on AWS WeldLink platform.
By utilizing these resources, staying informed about industry trends, and continuously upgrading your skills, you can navigate the evolving landscape of welding jobs with confidence and excel in your career endeavors.