Efficient Inventory Control: A Key to Distribution Center Management
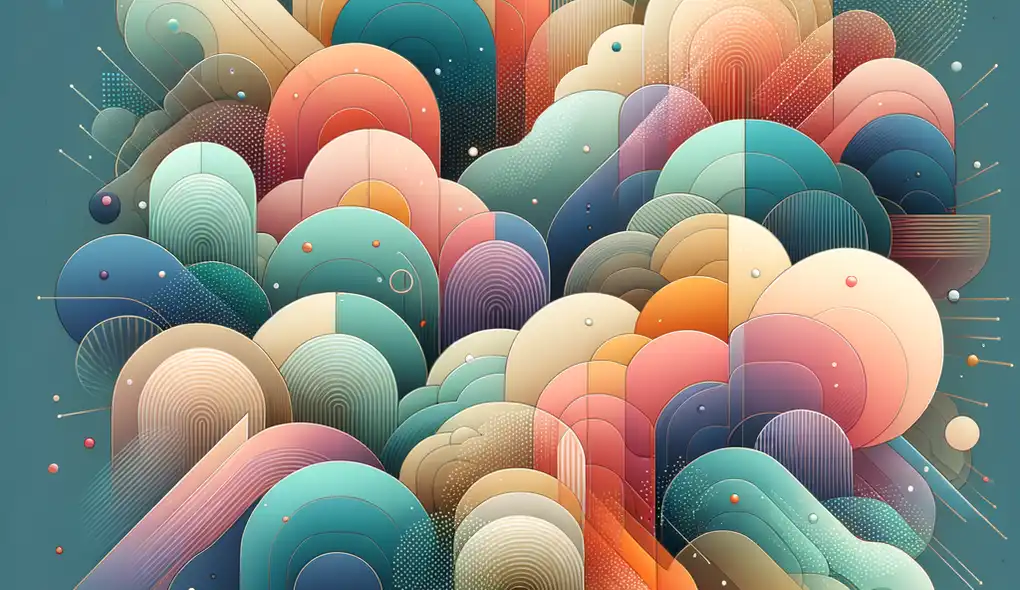
Efficient inventory control is the cornerstone of successful distribution center management. Not only does it enable organizations to meet customer demand with precision, but it also plays a crucial role in minimizing waste and enhancing overall performance. In today's competitive marketplace, where rapid fulfillment and lean operations are increasingly becoming standard benchmarks, mastering inventory control can be a significant competitive advantage.
Understanding Inventory Control
Inventory control refers to the processes and policies organizations use to manage their stock levels, from raw materials to finished goods. The goal is to maintain an ideal balance – having enough to meet customer demand without excessive overstock that ties up capital and leads to waste. Effective inventory control hinges on real-time data accuracy, efficient storage methods, and periodic reviews to ensure that the products on hand are sufficient, accessible, and align with projected demand.
Importance of Inventory Management in Distribution Centers
Distribution centers are pivotal nodes within supply chains, acting as the bridge between production and the final customer. Efficient inventory management within these facilities is vital to preventing both stockouts, which erode customer trust, and overstock, which squanders resources. By having a handle on inventory, distribution centers can improve their responsiveness, reduce carrying costs, improve space utilization, and lower the risk of obsolescence or deterioration of goods.
Inventory control is not just about having the right amount of stock; it's also about the strategic placement and turnover of that stock to ensure the most efficient use of resources and time. This requires the use of advanced tools and strategies to monitor and manage inventory effectively.
Essential Strategies for Efficient Inventory Control
Real-Time Data and Analytics
Incorporating real-time data and analytics into inventory management allows for immediate visibility into stock levels, demand patterns, and fulfillment status. Technologies such as RFID tags, Internet of Things (IoT) devices, and advanced inventory management software create an ecosystem that provides instant data for decision-making. This level of insight supports dynamic inventory adjustments and helps prevent issues before they arise.
Lean Inventory Practices
Adopting lean inventory practices involves eliminating excess and focusing on value-added activities. Techniques such as Just-In-Time (JIT) delivery and Kanban systems aim to reduce waste by receiving goods only when they are needed, thereby reducing the amount of inventory held at any given time. Additionally, regular review of inventory levels against actual demand helps to continuously refine stocking strategies.
Automation and Technology
Automation can vastly improve the accuracy and efficiency of inventory control. Automated storage and retrieval systems (AS/RS), robotic picking systems, and automated guided vehicles (AGVs) can all lead to more streamlined warehouse operations. When paired with inventory management software, these technologies can optimize the flow of goods through a distribution center, minimize manual errors, and reduce labor costs.
Cross-Docking and Flow-Through
Cross-docking is a practice where incoming shipments are directly transferred onto outbound vehicles, bypassing the need for long-term storage. This method is ideal for time-sensitive or perishable goods, as it reduces handling times and improves product freshness. Flow-through distribution strategies align incoming goods with immediate outbound orders, ensuring that inventory does not become stagnant.
Demand Forecasting
Accurate demand forecasting is critical to managing inventory levels effectively. By utilizing historical sales data, market trends, and predictive analytics, distribution centers can anticipate customer needs and adapt their inventory accordingly. This foresight offers a buffer against market fluctuations and assists in maintaining optimal stock levels.
Vendor Managed Inventory (VMI)
Vendor Managed Inventory arrangements allow suppliers to take responsibility for maintaining an agreed inventory level within a distribution center. This partnership can streamline replenishment processes, reduce administrative burdens, and offer more flexibility in managing stock.
Challenges in Inventory Control Management
Despite the various strategies available, inventory control management is not without its challenges. Fluctuations in demand, supply chain disruptions, and technological integration are factors that can complicate inventory dynamics. Frequent cycle counts, embracing continuous improvement philosophies, and investing in employee training can help mitigate these challenges.
Conclusion
Mastering efficient inventory control is a multifaceted undertaking that hinges on a combination of accurate data, lean practices, technological advancement, and strategic partnerships. Distribution centers that harness these elements effectively can not only reduce waste and improve performance but also deliver greater value to customers. With the right approach, inventory control can be transformed from a logistical challenge into a source of strategic leverage—propelling distribution center operations to new heights of operational excellence.
Frequently Asked Questions
Frequently Asked Questions
- What is the difference between inventory control and inventory management?
Inventory control focuses on the processes and policies that govern stock levels to ensure optimal balance and efficiency in meeting customer demand. On the other hand, inventory management encompasses a broader scope, including planning, organizing, and overseeing all aspects of inventory handling from procurement to distribution.
- How can real-time data improve inventory control in distribution centers?
Real-time data provides immediate visibility into stock levels, demand patterns, and fulfillment status, enabling quick decision-making and proactive adjustments to optimize inventory levels. Technologies like RFID tags and advanced inventory management software facilitate real-time data integration for enhanced control.
- What are the benefits of lean inventory practices?
Lean inventory practices help reduce waste, minimize excess stock, and enhance operational efficiency by focusing on value-added activities. Just-In-Time (JIT) delivery and Kanban systems are examples of lean practices that streamline inventory replenishment and storage processes.
- How does automation contribute to efficient inventory control?
Automation enhances inventory control by improving accuracy, efficiency, and reducing manual errors in storing, picking, and moving inventory. Automated systems such as AS/RS and AGVs optimize warehouse operations, leading to cost savings and streamlined workflows.
- What is cross-docking and how does it benefit distribution centers?
Cross-docking involves transferring incoming shipments directly to outbound vehicles without storing them, reducing handling times and improving supply chain responsiveness. This practice is ideal for time-sensitive goods and helps in maintaining product freshness and reducing storage costs.
- Why is demand forecasting important in inventory management?
Demand forecasting helps distribution centers anticipate customer needs, adjust inventory levels accordingly, and mitigate the risks of stockouts or overstock. By analyzing historical data and market trends, accurate demand forecasting supports efficient inventory planning and stocking strategies.
- What are the advantages of Vendor Managed Inventory (VMI) arrangements?
VMI allows suppliers to take charge of inventory replenishment, leading to streamlined processes, reduced administrative tasks for distributors, and improved flexibility in managing stock levels. This collaborative approach optimizes inventory control and enhances supply chain efficiency.
Resources
Further Resources
For readers interested in delving deeper into the realm of efficient inventory control and distribution center management, the following resources provide valuable insights and guidance:
- Inventory Management Best Practices: This comprehensive guide outlines essential best practices for effective inventory management, including real-time data utilization and lean inventory strategies.
- The Role of Technology in Inventory Control: Explore the transformative impact of technology on inventory control through this insightful article, highlighting the benefits of automation and data analytics.
- Supply Chain Optimization Techniques: Learn about advanced supply chain optimization techniques that enhance inventory management efficiency and streamline distribution center operations.
- Inventory Forecasting and Demand Planning: Dive into the intricacies of demand planning and inventory forecasting with this resource, offering practical tips for maintaining optimal stock levels.
- Warehouse Automation Trends: Stay updated on the latest warehouse automation trends that can revolutionize inventory control and enhance distribution center efficiency.
- Vendor Managed Inventory (VMI) Guide: Explore the concept of Vendor Managed Inventory (VMI) and its benefits in streamlining inventory replenishment processes within distribution centers.
- Effective Inventory Control Strategies: Gain insights into proven inventory control strategies that optimize stock levels, minimize waste, and improve operational performance.
These resources offer a wealth of knowledge and practical advice for enhancing inventory control practices and elevating distribution center management to new levels of efficiency and effectiveness. Happy reading and continued success in optimizing your inventory operations!