Ensuring Safety: Best Practices in Material Handling
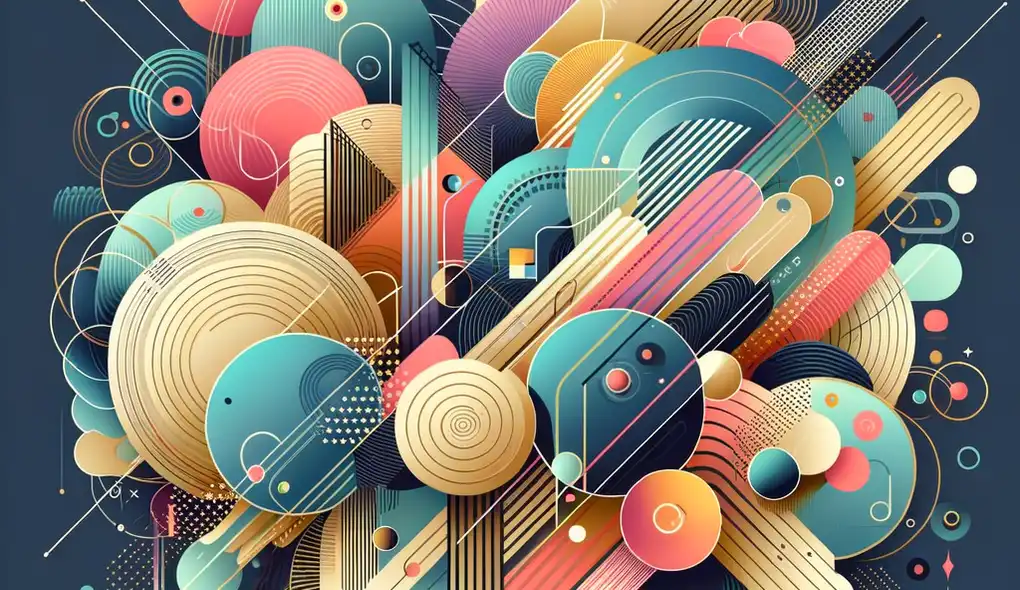
Material handling is a crucial operation in various industries such as manufacturing, construction, warehousing, and logistics. It involves the movement, protection, storage, and control of materials and products throughout manufacturing, warehousing, distribution, consumption, and disposal. As vital as it is to the supply chain, material handling also presents numerous safety challenges. Ensuring the safety of workers during material handling is imperative to prevent injuries, fatalities, and to maintain a productive working environment. This article outlines the best practices and safety guidelines that should be followed by material handlers to stay safe on the job.
Understanding the Risks
Material handling can involve the manual handling of objects, the use of machinery like forklifts and conveyors, and managing hazardous materials. Understanding the inherent risks in these activities is the first step towards mitigating them. Common risks include:
- Heavy lifting and repetitive motions that can lead to musculoskeletal disorders.
- Slips, trips, and falls due to uneven or slippery surfaces.
- Accidents involving material handling equipment, such as forklift collisions.
- Exposure to hazardous materials that can cause health issues.
- Falling objects and loads that are not properly secured.
Establishing Safety Protocols
The foundation of safety in material handling lies in establishing and following strict safety protocols. These protocols often include:
- Conducting regular safety training for all employees involved in material handling.
- Regular maintenance and inspection of all handling equipment.
- Using personal protective equipment (PPE) such as gloves, hard hats, safety shoes, and eyewear.
- Ensuring clear marking of aisles and passageways.
- Implementing proper procedures for the storage and disposal of hazardous materials.
Training and Education
Safety training is crucial to ensure that workers are aware of the hazards and know how to avoid them. Training programs should cover:
- Proper lifting techniques to minimize the risk of injury.
- The use of mechanical aids like trolleys, hoists, and forklifts.
- Safety procedures for operating material handling equipment.
- Emergency response procedures, including first aid and fire safety.
- Specific training for handling hazardous materials safely.
Maintaining Equipment
Poorly maintained equipment is a significant risk factor in material handling. To ensure safety:
- Carry out regular maintenance checks on all equipment.
- Remove any defective equipment from service until it is repaired or replaced.
- Keep a log of maintenance and repairs for each piece of equipment.
- Ensure that operators are trained to perform basic inspections before use.
Personal Protective Equipment (PPE)
Using the correct PPE can dramatically reduce the risk of injury in material handling. Essential PPE includes:
- Gloves to protect hands from sharp edges and hazardous substances.
- Safety shoes to protect feet from heavy objects.
- Hard hats to protect heads from falling objects.
- Safety glasses or face shields to protect against flying debris and chemical splashes.
Ergonomics
Practicing good ergonomics is key to preventing musculoskeletal disorders. This includes:
- Designing workstations to reduce awkward postures or movements.
- Providing adjustable equipment to accommodate different sizes and strengths of workers.
- Teaching workers to take frequent breaks and to stretch.
- Ensuring that heavy objects are stored at waist level to minimize lifting.
Environmental Controls
Maintaining a safe work environment is essential for material handling safety. This involves:
- Keeping floors clean and free of debris.
- Ensuring adequate lighting in all areas.
- Managing noise levels to prevent hearing damage.
- Ventilating areas where fumes or dust are present.
Material Storage and Disposal
Proper storage and disposal methods are critical to preventing accidents:
- Store materials at a low height to minimize the risk of falling objects.
- Use proper containers and labeling for hazardous materials.
- Follow all local, state, and federal regulations for material disposal.
Organizational Culture
Promoting a culture of safety within the organization encourages everyone to take responsibility for their safety and that of their colleagues. This can be achieved by:
- Encouraging reporting and open discussion of safety concerns.
- Recognizing and rewarding safe work practices.
- Implementing a zero-tolerance policy for safety violations.
Conclusion
Safety in material handling is a collective responsibility that requires commitment from all levels of an organization. By understanding the risks, establishing safety protocols, providing regular training, maintaining equipment, using appropriate PPE, and fostering a culture of safety, businesses can protect their workers and ensure a safe and efficient operation. Regular review and improvement of safety practices are also necessary to keep pace with changing conditions and regulations. Ultimately, safety is not just about compliance; it's about ensuring that every worker ends the day as healthy as they started it.
Frequently Asked Questions
Frequently Asked Questions
Q: What are the common risks associated with material handling?
A: Common risks in material handling include heavy lifting leading to musculoskeletal disorders, slips and falls, accidents with handling equipment, exposure to hazardous materials, and falling objects.
Q: How can safety be ensured in material handling?
A: Safety in material handling can be ensured by establishing safety protocols, providing adequate training, maintaining equipment, using personal protective equipment, and promoting a culture of safety within the organization.
Q: What equipment is essential for personal protective equipment (PPE) in material handling?
A: Essential PPE for material handling includes gloves, safety shoes, hard hats, and safety glasses or face shields.
Q: Why is ergonomics important in material handling?
A: Ergonomics is crucial in material handling to prevent musculoskeletal disorders by designing workstations, providing adjustable equipment, encouraging breaks, and storing heavy objects at waist level.
Q: How can organizations promote a culture of safety in material handling?
A: Organizations can promote a safety culture by encouraging reporting of safety concerns, rewarding safe practices, and implementing a zero-tolerance policy for safety violations.
Q: Why is regular review and improvement of safety practices important in material handling?
A: Regular review and improvement of safety practices are essential to adapt to changing conditions and regulations, ensuring that the workplace remains safe and compliant with standards.
Resources
Further Resources
For readers looking to delve deeper into the topic of safety in material handling, here are some valuable resources:
- Occupational Safety and Health Administration (OSHA) Material Handling Guidelines
- OSHA provides detailed information on best practices, regulations, and training resources related to material handling safety.
- National Institute for Occupational Safety and Health (NIOSH) - Ergonomics and Musculoskeletal Disorders
- NIOSH offers insights into ergonomics, musculoskeletal disorders, and the prevention of workplace injuries related to material handling.
- Material Handling Industry (MHI) Safety Resources
- MHI offers a range of safety resources, including webinars, guides, and safety standards for material handling operations.
- American Society of Safety Professionals (ASSP) - Material Handling Safety
- ASSP provides information on creating a safe work environment, implementing safety programs, and promoting a culture of safety in material handling.
- Canadian Centre for Occupational Health and Safety (CCOHS) - Warehouse Safety Tips
- CCOHS offers practical tips and guides specifically tailored to warehouse safety and material handling practices.
- Material Handling & Logistics Conference
- Attend industry conferences like MHLC to stay updated on the latest trends, technologies, and best practices in material handling and logistics.
These resources cover a wide range of topics related to material handling safety, providing essential information and guidance for employers, employees, and safety professionals.