Essential Skills Every Quality Control Manager Must Have
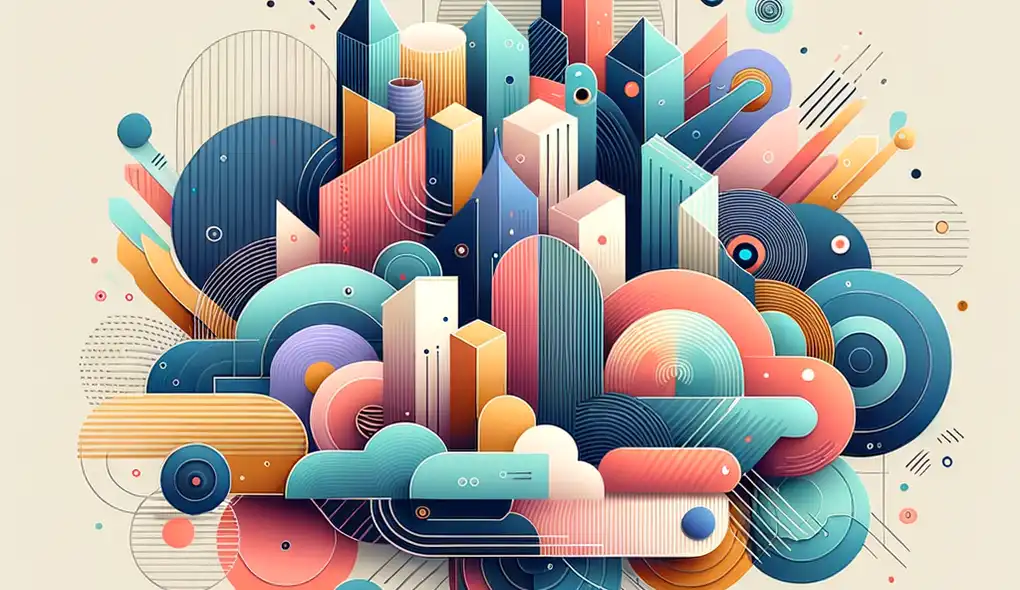
In the fast-paced world of production and services, quality control managers play a pivotal role in ensuring that the outputs of a business meet the highest standards. As guardians of standards, these professionals must possess a diverse skill set that enables them to maintain quality efficiently and effectively. Let's delve into the essential skills that set top-notch quality control managers apart in the competitive job market.
Analytical Skills
Quality control managers must routinely analyze data and processes to identify areas for improvement. They should be adept at using statistical tools and methodologies to assess product specifications and look for trends in the production process that may lead to defects. An understanding of Six Sigma, Kaizen, and other quality management systems is often necessary to dissect and solve complex problems.
Attention to Detail
A discerning eye for detail is non-negotiable. Because the devil often lies in the details, quality control managers must be thorough in their review of products and processes. This means examining items on a granular level and not allowing minor defects to slide by, as they can accumulate and lead to larger issues over time.
Communication Skills
Effective communication is essential for any manager, but for those in quality control, it's particularly critical. They must be able to convey quality standards and expectations clearly to their team, upper management, and sometimes to customers or regulatory bodies. The ability to listen and take constructive feedback is also key to iterative improvement in quality assurance.
Technical Expertise
While overseeing quality, managers must understand the technical aspects of the products or services their company offers. This includes knowledge of manufacturing processes, materials science, and engineering principles applicable to their sector. Such expertise enables them to pinpoint where in the production process quality might be compromised.
Leadership and People Management
Quality control isn't just a mechanical process; it involves leading a team to achieve stringent standards. Good leadership skills help quality control managers to motivate their teams, delegate tasks effectively, and enforce a culture of continual improvement. They must also manage conflicts and handle performance issues constructively.
Risk Management
In many industries, the stakes of producing subpar quality are high. Quality control managers need a keen understanding of risk management to weigh the costs and benefits of quality assurance activities. They should be able to anticipate potential issues and plan for contingencies to mitigate risks.
Project Management
Quality control is often project-based, with managers overseeing specific quality initiatives or the launch of new products. Project management skills, such as planning, scheduling, budgeting, and resource allocation, are essential to carry out these initiatives successfully and meet deadlines without compromising quality.
Problem-Solving
Unforeseen issues are par for the course in quality control. Managers must be quick to identify problems and even quicker to devise and implement effective solutions. Decision-making involves a balance of intuition and logical reasoning, often under pressure.
Adaptability
The ability to adapt to changing circumstances is crucial. Quality control managers may need to rapidly adjust their strategies in response to new regulations, shifting consumer demands, or technological advancements. A flexible approach enables them to maintain quality regardless of external factors.
Continuous Learning
The field of quality control is constantly evolving. Staying abreast of the latest quality standards, tools, and techniques is vital. Quality control managers should be committed to ongoing professional development to enhance their knowledge and stay competitive.
In conclusion, quality control managers are a linchpin in the pursuit of excellence within an organization. As we've explored, the qualifications for excelling in this role extend beyond the technical and into realms of leadership, risk assessment, adaptability, and continuous improvement. These skills, when harmonized, can create a robust quality assurance process that not only mitigates risks but also drives a business toward greater innovation and customer satisfaction.
Frequently Asked Questions
Frequently Asked Questions
What are the typical responsibilities of a quality control manager?
Quality control managers are responsible for overseeing and ensuring the quality of products and processes within a business. This includes establishing quality standards, implementing quality control measures, analyzing data for improvements, and leading quality initiatives.
What qualifications are required to become a quality control manager?
Typically, quality control managers are expected to have a bachelor's degree in a relevant field such as quality management, industrial engineering, or a related discipline. Previous experience in quality control or a related field is also desirable. Certification in quality management systems like Six Sigma or ISO standards can enhance your credentials.
How important are communication skills for a quality control manager?
Communication skills are crucial for quality control managers as they need to effectively convey quality standards, provide feedback to their team, and communicate with stakeholders. Clear communication helps in ensuring that quality expectations are understood and met throughout the organization.
What are some common challenges faced by quality control managers?
Quality control managers may face challenges such as resistance to quality initiatives, balancing quality with production efficiency, adapting to new technologies, and maintaining consistent quality standards across diverse products or processes. Overcoming these challenges requires problem-solving skills and a proactive approach to quality management.
How can quality control managers stay updated with industry trends and best practices?
To stay informed about industry trends and best practices, quality control managers can attend conferences, workshops, and seminars related to quality management. Subscribing to industry publications, joining professional organizations, and networking with peers can also help in staying updated with the latest developments in quality control.
What strategies can quality control managers implement to improve product quality?
Quality control managers can implement strategies such as conducting regular quality audits, providing training to employees on quality standards, implementing quality improvement projects, and adopting quality management tools and technologies. Continuous monitoring, feedback loops, and incorporating customer feedback are also effective methods for improving product quality.
How does quality control contribute to the overall success of a business?
Quality control plays a significant role in enhancing customer satisfaction, reducing rework and waste, improving product reliability, and maintaining a positive brand reputation. By ensuring consistent quality, quality control contributes to operational efficiency, cost savings, and long-term success for the business.
Resources
Further Resources
For further reading and development of essential skills for quality control managers, the following resources are highly recommended:
- Analytical Skills
- Attention to Detail
- Communication Skills
- Technical Expertise
- Leadership and People Management
- Risk Management
- Project Management
- Problem-Solving
- Adaptability
- Continuous Learning