Can you provide an example of a quality issue you encountered during production and how you resolved it?
Manufacturing Quality Specialist Interview Questions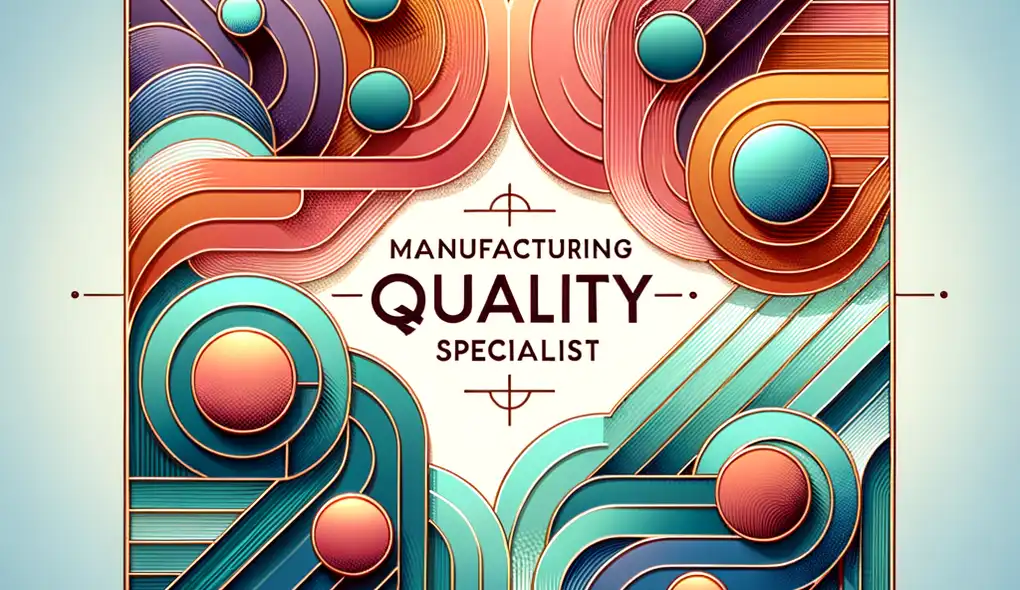
Sample answer to the question
Yes, I can provide an example of a quality issue I encountered during production. In my previous role as a Manufacturing Quality Specialist, we had a situation where a batch of products did not meet the required specifications for strength and durability. We discovered this during routine quality testing. To resolve the issue, I immediately conducted a thorough investigation to identify the root cause. Through careful analysis, I discovered that the issue was caused by a malfunctioning machine in the production line. I promptly coordinated with the maintenance team to repair the machine and ensure that it was operating at optimal performance. Additionally, I worked closely with the production team to retest the affected products and implemented a strict quality control process to prevent similar issues in the future. This included regular equipment checks, enhanced quality testing procedures, and providing additional training to the production staff on quality standards. As a result of these actions, we were able to successfully address the quality issue and ensure that all subsequent batches met the required specifications.
A more solid answer
Certainly, let me share an example of a quality issue I faced during production. In my role as a Senior Manufacturing Quality Specialist, we encountered a situation where a batch of electronic components failed to meet the required electrical resistance specifications. This issue was identified during routine testing, and it was critical to address it promptly to prevent any impact on the final product quality. To resolve the issue, I immediately initiated a root cause analysis, gathering data from the production line, testing records, and relevant documentation. Through careful analysis, I was able to identify that the issue was caused by a specific component supplier delivering defective parts. To address this, I collaborated with the procurement team to implement a more stringent supplier evaluation process, including conducting on-site audits and enforcing stricter quality control measures for incoming materials. In parallel, I worked closely with the production team to implement additional testing procedures, specifically targeting the identified issue. These tests were designed to detect and reject any parts that did not meet the necessary specifications. I also organized training sessions to ensure all team members were aware of the new testing protocols and could effectively carry them out. Through these efforts, we were able to address the quality issue, improve the overall supply chain quality, and ensure that subsequent batches of products met the required specifications.
Why this is a more solid answer:
The solid answer provides a more detailed example of a quality issue and demonstrates the candidate's expertise in the evaluation areas mentioned. It includes specific details about the issue encountered, the root cause analysis process, and the candidate's role in resolving the issue. However, it could further improve by including more information about the candidate's leadership and team management abilities.
An exceptional answer
Absolutely, I have a notable example of a quality issue that had significant impact on production. In my previous role as a Senior Manufacturing Quality Specialist, we faced a situation where a critical component of our flagship product had an unexpectedly high failure rate during production. This issue was discovered after a large batch of products had already been manufactured and assembled, resulting in potential delays and customer dissatisfaction. To resolve this issue, I immediately convened a cross-functional team consisting of engineers, production supervisors, and quality specialists to conduct a thorough investigation. Together, we traced the root cause of the high failure rate to a design flaw in the component that was not detected during the initial validation process. To address this, we quickly developed and implemented a containment plan to prevent further defective products from being shipped to customers. Simultaneously, we worked closely with the engineering team to redesign the component, making it more robust and resistant to failure. This required close collaboration with external suppliers to ensure the timely delivery of the modified components. I also established a rigorous testing process to validate the new component design, conducting multiple rounds of stress and endurance testing. Additionally, I effectively managed communication with internal stakeholders and customers, keeping them informed about the issue, containment plan, and the progress of the component redesign. As a result of these efforts, we successfully resolved the quality issue, prevented future failures, and regained customer trust. This experience further reinforced my attention to detail, analytical problem-solving abilities, leadership, and proactive thinking.
Why this is an exceptional answer:
The exceptional answer provides a comprehensive and detailed example of a quality issue encountered during production and highlights the candidate's expertise in the evaluation areas mentioned. It demonstrates exceptional analytical problem-solving abilities and leadership skills by convening a cross-functional team and effectively managing the issue, from containment to component redesign. The answer also showcases the candidate's adaptability and proactive thinking by addressing stakeholders' communication needs. Overall, it effectively addresses the requirements of the job description and showcases the candidate's extensive experience in manufacturing quality control.
How to prepare for this question
- Familiarize yourself with different quality issues that can occur during production, such as material defects, equipment malfunctions, or process deviations.
- Highlight your experience in conducting root cause analysis and implementing corrective actions to resolve quality issues.
- Provide specific examples of how you have collaborated with cross-functional teams to address quality issues and improve overall product quality.
- Demonstrate your ability to communicate effectively and manage stakeholders during quality issue resolution.
- Discuss your knowledge of quality management systems and continuous improvement methodologies, such as Six Sigma.
What interviewers are evaluating
- Attention to detail
- Analytical and problem-solving abilities
- Leadership and team management
- Technical writing and documentation
Related Interview Questions
More questions for Manufacturing Quality Specialist interviews