Mastering Failure Analysis Techniques: Essential Know-How for Engineers
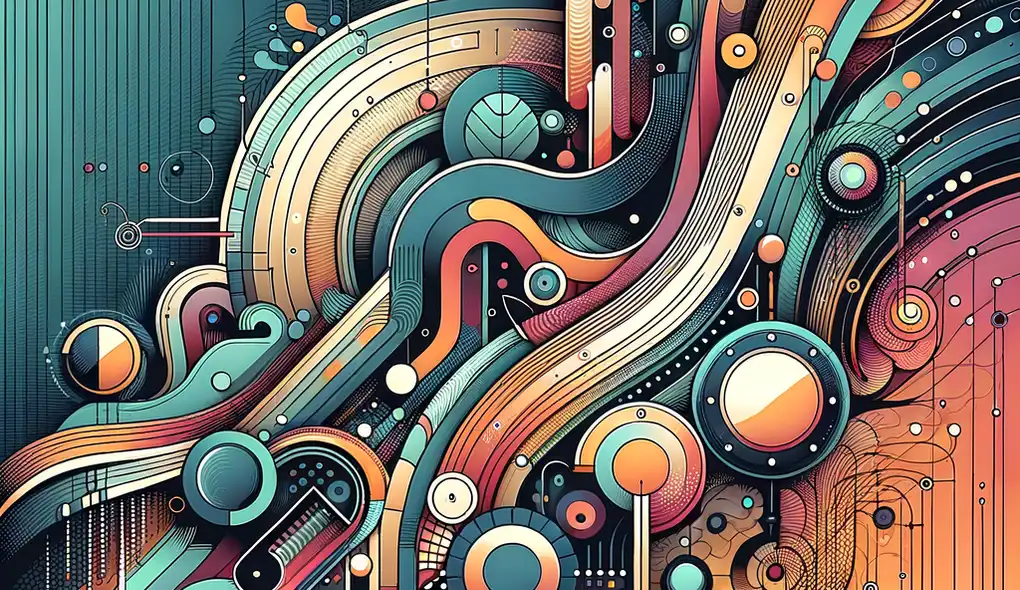
Failure analysis is a critical discipline within engineering, focused on identifying the root causes behind the malfunction or breakdown of components, materials, systems, or structures. For engineers looking to specialize in this niche field, mastering the various techniques of failure analysis is not just beneficial; it's essential for ensuring safety, improving product design, and preventing future failures. In this article, we dive deep into the essential failure analysis techniques that every aspiring engineer should equip themselves with to excel in this demanding yet rewarding domain.
Understanding Failure Analysis
Before delving into the techniques, it's important to understand what failure analysis is and why it's crucial. Failure analysis is the process used to determine how and why a component or system has failed. The information gleaned from this process is used to prevent future failures, leading to safer products and systems, economic savings, and sometimes even saving lives.
Visual Inspection
The first step in any failure analysis is a thorough visual inspection of the failed component. Engineers look for signs of damage, deformation, corrosion, and any other abnormalities. This step often utilizes magnification tools, photography, and video recording to document findings meticulously. Visual inspection might seem simple, but it can reveal a wealth of information.
Mechanical Testing
Following inspection, mechanical testing may be conducted to better understand the strength and ductility of the material. This can involve tensile tests, hardness tests, and impact tests. These tests simulate stresses the component may have experienced and can provide insight into how it might have failed under different conditions.
Chemical Analysis
Chemical analysis is crucial for identifying the material composition and detecting any contaminants or unexpected elements that may have contributed to the failure. Techniques like spectroscopy, chromatography, and metallography are commonly used for these purposes.
Fractography
One of the most telling techniques in failure analysis is fractography, which involves the study of fracture surfaces. Through fractography, engineers can identify the type of fracture (e.g., ductile, brittle, fatigue) and the direction of crack propagation, which often points to the root cause of the failure.
Nondestructive Testing (NDT)
NDT methods allow engineers to examine components without causing further damage. Common NDT techniques include ultrasonic testing, radiography, magnetic particle testing, and dye penetrant inspection. These methods can often identify flaws or cracks that are not visible to the naked eye.
Computational Analysis
With advancements in technology, computational tools like finite element analysis (FEA) and computational fluid dynamics (CFD) have become essential in failure analysis. These methods simulate real-world conditions and forecast how a component might behave, helping to identify potential weak points.
Root Cause Analysis (RCA)
RCA is a systematic approach used to determine the underlying causes of failures. Methods like the Five Whys, fault tree analysis, and cause and effect diagrams help to peel back the layers and uncover why a failure occurred. This step is critical to develop solutions that prevent recurrence.
Metallurgical Analysis
Metallurgical analysis examines the microstructure of metals to understand the history of a component, including its production process, heat treatment, and any subsequent degradation. Microscopes and scanning electron microscopes (SEM) are essential tools for this analysis.
Case Study and Collaborative Approaches
Learning from historical failures and collaborating with experts across different disciplines can provide unique insights. Reviewing case studies of past failures brings to light patterns and lessons that can be applied to current issues. Collaborative efforts often result in more comprehensive failure analysis, combining various perspectives and expertise.
Learning from Failures
An important aspect of becoming adept at failure analysis is the mindset of learning from failures. This approach encourages systematic investigation, openness to new ideas, and continual knowledge building. It's not enough to simply identify what went wrong; engineers must also learn how to adapt and apply this knowledge to future designs and practices.
Conclusion
In conclusion, mastering the techniques of failure analysis is a journey that involves a blend of technical skills, critical thinking, and a proactive learning stance. Engineers equipped with these skills will not only help prevent failures but also drive innovation and enhance the reliability of engineering projects. As technology evolves, so, too, will the techniques of failure analysis, and staying ahead means being committed to lifelong learning and adaptation in this dynamic field.
Frequently Asked Questions
Frequently Asked Questions
Failure analysis is a complex and intriguing field within engineering, raising various questions for both beginners and seasoned professionals. Here, we address some of the frequently asked questions related to failure analysis to provide clarity and insight into this critical discipline.
What is the Importance of Failure Analysis in Engineering?
Failure analysis plays a crucial role in engineering by helping to identify the root causes of component failures. By understanding why failures occur, engineers can prevent future issues, enhance product reliability, and ensure safety in various applications. It is an essential tool for improving design, materials selection, and manufacturing processes.
How Does Failure Analysis Benefit Engineering Industries?
Failure analysis benefits engineering industries in several ways. It helps in improving product quality, reducing downtime due to unexpected failures, enhancing safety standards, and optimizing maintenance procedures. Additionally, failure analysis can lead to cost savings by addressing issues proactively and preventing catastrophic failures.
What Are the Common Challenges Faced in Failure Analysis?
Failure analysis can present challenges due to the complexity of modern engineering systems, the interplay of multiple factors leading to failures, and the need for specialized expertise and advanced testing techniques. Lack of access to relevant information, time constraints, and limited resources can also pose challenges in conducting thorough failure investigations.
Which Industries Rely Heavily on Failure Analysis Techniques?
Several industries rely heavily on failure analysis techniques, including aerospace, automotive, oil and gas, electronics, and manufacturing. These industries deal with high-performance components and systems where failure can have significant consequences. Failure analysis is integral to improving product performance, ensuring regulatory compliance, and meeting customer expectations.
How Can Engineers Enhance Their Skills in Failure Analysis?
Engineers can enhance their skills in failure analysis by pursuing specialized training courses, gaining practical experience in conducting failure investigations, staying updated on industry developments, and collaborating with experts in the field. Continuous learning, critical thinking, and attention to detail are key to mastering the intricacies of failure analysis.
What Role Does Documentation Play in Failure Analysis?
Documentation is essential in failure analysis as it helps in recording observations, test results, analysis findings, and conclusions. Thorough documentation ensures that the entire investigative process is well-documented, allowing for traceability, peer review, and future reference. Clear and detailed documentation forms the basis for informed decision-making and effective communication of findings.
How Can Failure Analysis Contribute to Product Innovation?
Failure analysis can contribute to product innovation by providing valuable insights into the performance limitations of existing designs, materials, and processes. By understanding the failure mechanisms, engineers can innovate new solutions that address vulnerabilities, enhance product durability, and meet evolving market demands. Failure analysis serves as a catalyst for continuous improvement and innovation in engineering.
Is Failure Analysis Only Relevant for Investigating Catastrophic Failures?
While failure analysis is commonly associated with investigating catastrophic failures, its relevance extends beyond such instances. Failure analysis is essential for understanding the performance limits of components under various conditions, identifying potential weaknesses in designs, and improving overall product reliability. Conducting failure analysis proactively, even for minor failures, can prevent larger issues from occurring in the future.
What Are the Ethical Considerations in Failure Analysis?
Ethical considerations in failure analysis include maintaining confidentiality of sensitive information, respecting intellectual property rights, ensuring transparency in reporting findings, and upholding professional standards of conduct. Engineers involved in failure analysis must adhere to ethical guidelines, prioritize safety and integrity, and communicate findings objectively and responsibly.
How Can Failure Analysis Help in Legal and Liability Matters?
Failure analysis can provide valuable evidence in legal and liability matters by establishing the causes of failures, determining responsibilities, and supporting claims related to product defects or accidents. In legal proceedings, failure analysis reports and expert testimony can strengthen the credibility of arguments, facilitate dispute resolution, and ensure accountability for engineering failures.
For further insights and resources on failure analysis techniques, consult industry publications, attend specialized workshops and conferences, and engage with professional organizations dedicated to failure analysis and materials engineering.
Resources
Further Resources
For readers interested in delving deeper into the field of failure analysis and expanding their knowledge beyond the fundamentals covered in this article, the following resources are highly recommended:
- Books:
- Failure Analysis of Engineering Structures: This comprehensive book covers the principles and practices of failure analysis in engineering structures with practical examples and case studies.
- Practical Fractography: A guide to understanding fractography techniques and interpreting fracture surfaces.
- Online Courses:
- Coursera - Failure Analysis in Engineering: A series of online courses offering in-depth knowledge on failure analysis techniques and methodologies.
- Udemy - Mastering Root Cause Analysis: Enhance your skills in root cause analysis with practical exercises and real-world examples.
- Industry Conferences:
- International Conference on Failure Analysis: An annual conference bringing together experts in failure analysis to discuss the latest research and advancements in the field.
- ASM International - Failure Analysis Society: Join this society to connect with professionals dedicated to advancing failure analysis practices.
- Professional Organizations:
- American Society for Nondestructive Testing (ASNT): Access resources, certifications, and networking opportunities in the field of nondestructive testing.
- Materials Research Society (MRS): Stay updated on materials research and advancements that impact failure analysis techniques.
- Journals and Publications:
- Journal of Failure Analysis and Prevention: A peer-reviewed journal publishing the latest research and case studies in failure analysis.
- Materials Performance and Characterization: Explore materials performance and characterization techniques that intersect with failure analysis.
- Online Forums and Communities:
- Eng-Tips Forums - Failure Analysis: Engage with engineers and experts in failure analysis to discuss challenges and share insights.
- Reddit - r/FailureAnalysis: Connect with a community of enthusiasts and professionals passionate about failure analysis.
- Laboratory Facilities:
- Visit local university or industrial laboratories that specialize in failure analysis to observe real-world applications of the discussed techniques.
By exploring these diverse resources, readers can enhance their understanding, refine their skills, and stay abreast of the latest developments in the field of failure analysis. Continuous learning and engagement with the broader failure analysis community will undoubtedly enrich one's expertise and contribute to becoming a proficient practitioner in this critical engineering discipline.