Overcoming Common Challenges in a QC Specialist Career
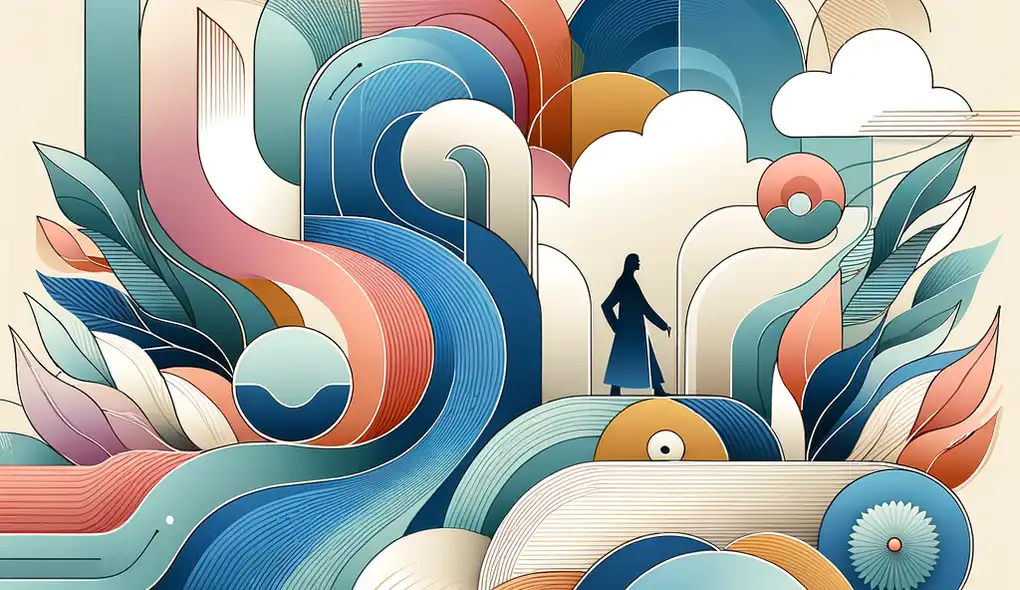
Quality Control (QC) Specialists play a crucial role in ensuring that products and services meet established standards of quality before they reach the market. As the guardians of excellence, their work has a significant impact on customer satisfaction, brand reputation, and the overall success of a company. However, pursuing a career in quality control presents a unique set of challenges that can test even the most diligent and committed professionals. In this article, we will explore the most common hurdles faced by Quality Control Specialists and discuss strategies to successfully navigate them, drawing on insights from industry experts and best practices in the field.
Identifying Subtle Quality Issues
One of the first challenges QC Specialists encounter is the detection of subtle quality issues that are not immediately apparent. These can range from slight inconsistencies in product dimensions to minor variations in color or texture. These issues, while seemingly inconsequential, can escalate into significant problems if not addressed early on. To overcome this hurdle, QC Specialists must adopt a keen eye for detail and develop superior observational skills. Continuous training in defect recognition, familiarity with the latest quality control technology, and a methodical approach to inspection processes can all contribute to enhanced detection capabilities.
Strategies for improving detection include:
- Participating in ongoing education and training programs.
- Staying abreast of industry standards and technological advancements.
- Implementing systematic inspection strategies that include comprehensive checklists and quality metrics.
Handling Increasingly Complex Products and Processes
As industries evolve, so do the products and processes that QC Specialists must oversee. Dealing with increasingly complex items and intricate manufacturing procedures can become overwhelming. To remain effective, QC Specialists must commit to lifelong learning and adaptability. They should gain an understanding of new materials, technologies, and methods to ensure they maintain their capability to assess product quality accurately.
Proactive ways to manage complexity in QC include:
- Attending workshops and courses relevant to the industry and advancements in QC techniques.
- Collaborating with engineering and production teams to understand new processes.
- Utilizing sophisticated QC tools and software to manage and analyze data.
Navigating Regulatory Compliance
Another significant challenge for QC Specialists is keeping up with and implementing various regulatory requirements. Regulations often differ by region and industry, and staying compliant can be a daunting task. This necessitates an ongoing effort to understand and interpret regulations correctly, as well as to integrate them into QC protocols.
Strategies to ensure compliance include:
- Regularly reviewing updates to regulations and standards.
- Engaging in training sessions focused on regulatory compliance.
- Establishing a compliance roadmap, and periodically auditing QC systems to ensure adherence.
Maintaining Objectivity and Independence
Quality Control Specialists are expected to provide unbiased assessments, but this can be compromised by internal pressures from production teams to meet quotas or deadlines. Maintaining professional objectivity is essential to uphold the integrity of the QC process. To meet this challenge, QC Specialists must assert their commitment to quality standards and advocate for their importance within the organization.
To maintain objectivity, QC Specialists can:
- Regularly communicate the importance of quality standards to other departments.
- Advocate for a corporate culture that prioritizes quality over quantity.
- Seek support from management when necessary to maintain independence.
Communicating Findings Effectively
A QC Specialist's ability to communicate their findings is critical. They must convey issues effectively to stakeholders who may have limited technical knowledge. To bridge the communication gap, QC Specialists should develop clear and concise reporting skills, using language that is accessible while still accurately representing the intricacies of quality issues.
Effective communication tactics include:
- Tailoring communication styles to the audience.
- Employing visual aids and examples to illustrate issues.
- Providing clear recommendations for corrective actions based on findings.
Balancing Speed and Accuracy
In fast-paced production environments, QC Specialists are under constant pressure to perform their inspections quickly without compromising on accuracy. This balance is often difficult to achieve, but it is crucial for timely deliveries and product launches. To manage this dual demand, QC Specialists should leverage technological tools that can streamline inspections and automate certain aspects of the QC process without sacrificing attention to detail.
Tips for balancing speed and accuracy:
- Invest in real-time quality control systems that provide immediate feedback.
- Develop proficiency in the use of QC software that speeds up routine tasks.
- Optimize inspection workflows to eliminate unnecessary steps without cutting corners.
Staying Motivated in a Repetitive Role
QC work can sometimes become monotonous due to the repetitive nature of inspections and tests. Maintaining motivation and drive over the long term is crucial for career success and personal satisfaction. This involves setting personal goals, seeking variety in tasks, and understanding the broader impact of QC work on company success and customer safety.
Strategies to stay motivated include:
- Setting clear professional milestones and working towards them in a structured way.
- Pursuing opportunities for cross-training in different QC areas.
- Connecting with a community of QC professionals to share experiences and advice.
Conclusion
Quality Control Specialists face a multitude of challenges that require a comprehensive set of skills and strategies to overcome. By focusing on continuous improvement, regulatory compliance, effective communication, speed, accuracy, and self-motivation, these professionals can navigate the complexities of their roles and excel in their careers. As the demand for quality continues to grow in various industries, the role of the Quality Control Specialist will only become more vital, underscoring the importance of mastering these challenges to achieve long-term success in this field.
Frequently Asked Questions
Frequently Asked Questions About Overcoming Common Challenges in a QC Specialist Career
Q: How can QC Specialists improve their ability to detect subtle quality issues?
A: QC Specialists can enhance their detection skills by participating in ongoing education and training programs, staying updated on industry standards, and implementing systematic inspection strategies with comprehensive checklists and quality metrics.
Q: What are some proactive ways for QC Specialists to manage complexity in dealing with increasingly complex products and processes?
A: To handle complexity, QC Specialists should attend relevant workshops and courses, collaborate with engineering and production teams, and utilize sophisticated QC tools and software for data management and analysis.
Q: How can QC Specialists ensure compliance with regulatory requirements?
A: Ensuring compliance involves regularly reviewing regulations, engaging in training sessions on compliance, and establishing a compliance roadmap while periodically auditing QC systems for adherence.
Q: What strategies can QC Specialists employ to maintain objectivity and independence in their assessments?
A: QC Specialists can maintain objectivity by communicating the importance of quality standards, advocating for a quality-focused corporate culture, and seeking management support when needed to uphold independence.
Q: How can QC Specialists effectively communicate their findings to stakeholders with limited technical knowledge?
A: QC Specialists should tailor their communication styles to the audience, use visual aids and examples to illustrate issues, and provide clear recommendations for corrective actions based on their findings.
Q: What tips can help QC Specialists balance speed and accuracy in their inspections?
A: To balance speed and accuracy, QC Specialists should invest in real-time quality control systems, develop proficiency in QC software, and optimize inspection workflows for efficiency without compromising accuracy.
Q: How can QC Specialists stay motivated in a role that may become repetitive?
A: To maintain motivation, QC Specialists should set professional goals, seek variety in tasks through cross-training, and connect with a community of QC professionals to share experiences and advice.
For more resources on overcoming challenges in a QC Specialist career, refer to the following:
Resources
Further Resources
For additional insights and information on excelling in a Quality Control Specialist career, the following resources are recommended:
- American Society for Quality (ASQ): ASQ offers a wide range of certification programs, training courses, and resources for quality control professionals. Visit their website here.
- Quality Digest: An online publication that covers quality management, standards, and best practices. Access articles, webinars, and whitepapers here.
- National Association for Healthcare Quality (NAHQ): Ideal for those in the healthcare industry, NAHQ provides education, networking opportunities, and certifications for quality specialists. Learn more here.
- International Society of Pharmaceutical Engineering (ISPE): Specifically focused on pharmaceutical quality control, ISPE offers training, conferences, and publications. Explore their resources here.
- LinkedIn Learning: A platform with numerous courses on quality control, statistical process control, and related topics. Browse courses here.
- Quality Management and Statistics Resources: Access a collection of articles, tools, and resources provided by the U.S. Food and Drug Administration (FDA) here.