Mastering Quality Control: Essential Skills for Production Quality Supervisors
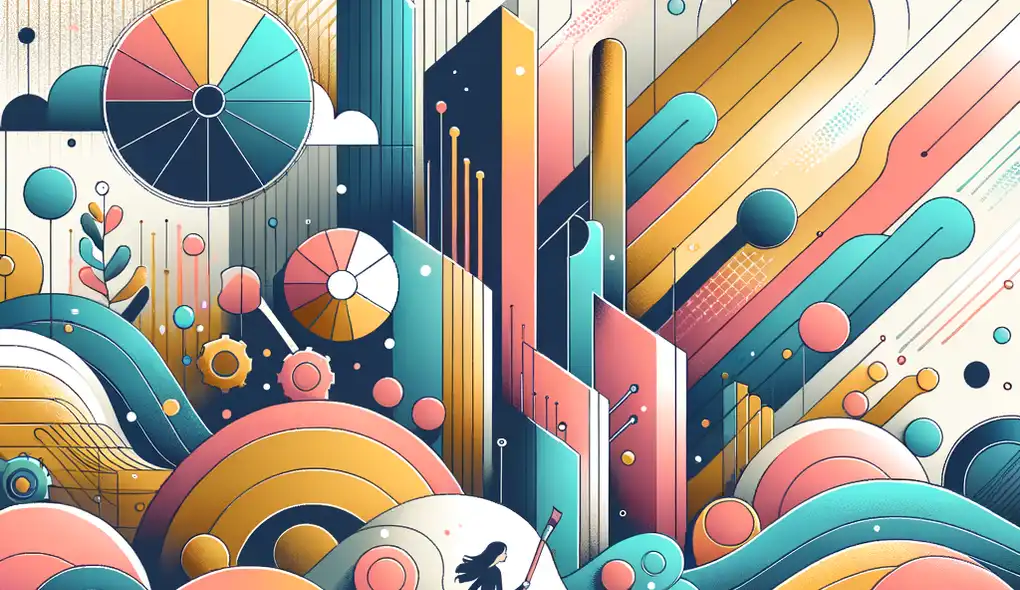
In the cosmopolitan landscape of industrial production, the role of a Production Quality Supervisor is as integral as it is demanding. Tasked with ensuring the apex of quality in products, these supervisors are the custodians of a company's reputation. As markets become increasingly competitive and consumer expectations soar, mastering the art of quality control becomes a lynchpin to not just surviving but thriving in manufacturing industries. In this detailed exploration, we’ll unravel the essential skills needed to succeed as a Production Quality Supervisor and provide insights on how to hone these skills to excellence.
Technical Comprehension and Application
First and foremost, a strong understanding of the technical aspects of the products and production processes is the cornerstone of any quality supervisory role. Familiarity with material properties, engineering principles, and manufacturing technology is essential. Production Quality Supervisors must decipher complex specifications, blueprints, and quality standards to ensure that the final products align perfectly with design intent.
Mastering this domain requires a blend of formal education, such as a degree in industrial engineering or a related field, and practical on-the-job experience. Continuous learning through workshops, seminars, and certifications in Six Sigma, Lean manufacturing, and ISO standards will solidify this foundational knowledge and keep you abreast of industry changes.
Meticulous Attention to Detail
Quality control is synonymous with precision. Supervisors must possess an eagle's eye for detail, spotting defects or deviations that could compromise product integrity. This includes conducting thorough inspections, audits, and reviews at various stages of the production process. It's not just about catching errors, but also about understanding their root causes and extrapolating what can prevent recurrence.
Developing a meticulous nature can be engrained through habit. Start by creating checklists for repetitive tasks, keep detailed records, and practice methodical problem-solving approaches like the "5 Whys" technique—an iterative question-asking method used to explore the cause-and-effect relationships underlying a particular problem.
Leadership and Team Management
Production Quality Supervisors do not work in isolation; they direct teams. Effective leadership skills, such as communication, decision-making, conflict resolution, and motivational techniques, are vital. It's about molding a team that shares a unified goal of quality.
To master these skills, supervisors should actively seek opportunities to lead projects, mentor junior staff, and engage in leadership courses. Joining professional organizations or forums can provide networking opportunities and expose supervisors to diverse management styles and strategies.
Customer Focus and Business Acumen
Having a customer-centric approach is crucial. Quality control isn't just about meeting standards; it’s about exceeding customer expectations. A deep understanding of what the customer needs and how those needs evolve ensures that quality remains relevant.
Additionally, understanding the broader business context is important. A supervisor who can correlate quality with business outcomes such as customer satisfaction, repeat business, and cost savings, becomes a valuable asset to an organization. This dual skill can be honed through engaging with sales and customer service departments and by participating in business strategy meetings.
Analytical Skills and Decision Making
The ability to collect, analyze, and interpret data to make informed decisions is core to the role. Proficiency in data analysis tools and quality management software will facilitate identifying trends, predicting potential faults, and guiding strategic quality enhancements.
Certifications in analytics, hands-on use of statistical analysis software, and involvement in cross-functional teams that work on solving complex problems can help sharpen these analytical skills. Furthermore, scenario planning and decision-making exercises can improve the ability to anticipate and mitigate risks.
Adaptability and Continuous Improvement
The industrial sector is ever-evolving, and so are the techniques and tools for quality assurance. Embracing change and being adaptable are indispensable traits for a Quality Supervisor. The commitment to continuous improvement, both personally and process-wise, will ensure that quality standards keep pace with innovation.
Engaging in regular training, staying updated with the latest industry trends through journals and trade shows, and encouraging innovation within the team are ways to foster an adaptive and progressive mindset.
Effective Communication
None of the aforementioned skills matter if they cannot be effectively communicated. Supervisors must articulate quality metrics, procedures, and improvements clearly to both their teams and upper management. They must also listen attentively to feedback and concerns, acting as a bridge between the production floor and the boardroom.
Building communication skills can be done through active participation in meetings, public speaking engagements, writing detailed reports, and practicing active listening.
Conclusion
The synthesis of technical prowess, meticulous observation, leadership finesse, customer sensitivity, analytical acuity, adaptability, and communication fluency is what makes a masterful Production Quality Supervisor. By consciously developing these skills through education, practice, and reflection, individuals can rise to meet the challenges of this dynamic field and lead their organizations toward a future where quality is not just an aim, but a guarantee.
Frequently Asked Questions
Frequently Asked Questions
What are the primary responsibilities of a Production Quality Supervisor?
A Production Quality Supervisor is responsible for ensuring the quality of products through the implementation of quality control measures. This includes conducting inspections, audits, and reviews at various stages of the production process, identifying defects, analyzing root causes, and implementing preventive measures to uphold product integrity.
What are the essential skills required to succeed as a Production Quality Supervisor?
Key skills for a Production Quality Supervisor include technical comprehension, attention to detail, leadership, team management, customer focus, business acumen, analytical skills, decision-making abilities, adaptability, and effective communication.
How can one improve their attention to detail in quality control?
To enhance attention to detail, supervisors can create checklists for tasks, maintain detailed records, practice systematic problem-solving techniques like the "5 Whys", and conduct thorough inspections throughout the production process.
What certifications or training programs are beneficial for a Production Quality Supervisor?
Certifications in Six Sigma, Lean manufacturing, and ISO standards are valuable for enhancing technical knowledge. Additionally, training in data analysis tools, quality management software, and leadership development programs can further equip supervisors for their role.
How important is customer focus in quality control?
Maintaining a customer-centric approach is vital in quality control to not only meet but exceed customer expectations. Understanding evolving customer needs and aligning quality processes to deliver value to customers is essential for sustained success.
How can a Production Quality Supervisor stay updated with industry trends?
Supervisors can stay informed about the latest industry trends by attending workshops, seminars, and trade shows, subscribing to industry journals, participating in professional forums, and engaging with sales and customer service departments to align quality initiatives with business goals.
Resources
Further Resources
For further exploration and enhancement of your skills as a Production Quality Supervisor, here are some valuable resources:
- Courses and Certifications:
- Books:
- Professional Organizations:
- Online Platforms:
- LinkedIn Learning - Offers various courses on quality control and leadership
- Coursera - Provides specialized courses from top universities on quality management
- Industry Journals and Publications:
- Workshops and Conferences:
- Software Tools:
- Blogs and Online Communities:
By leveraging these resources, you can deepen your expertise, stay updated with industry trends, and network with professionals in the field. Continuous learning and exploration of new tools and techniques will further solidify your position as a proficient and successful Production Quality Supervisor.