Breaking Into Lean Management: A Guide for Aspirants
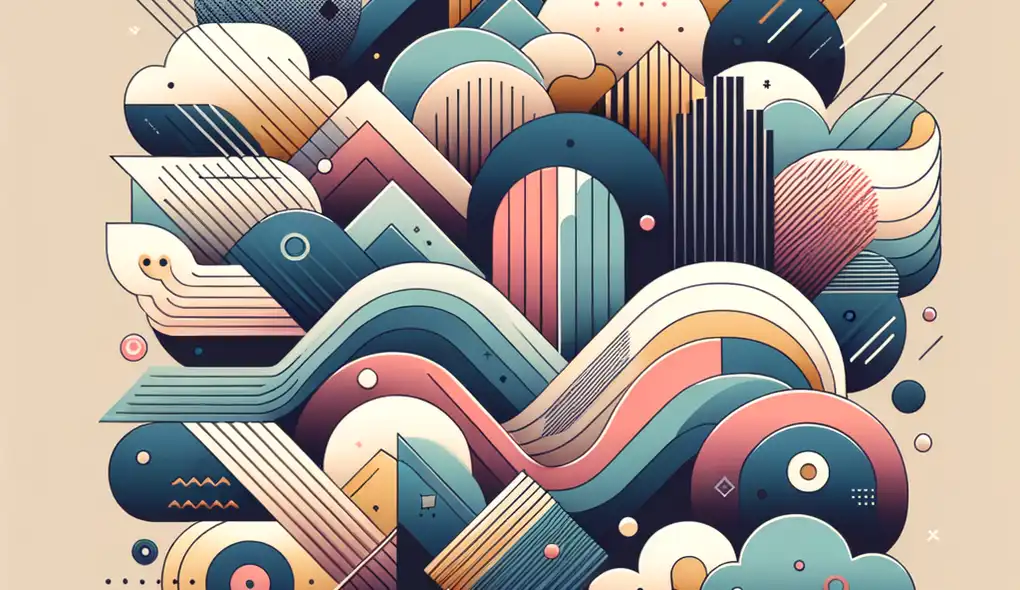
The concept of lean management has evolved significantly since its origins in the Japanese manufacturing industry, particularly within the automotive sector. It has become a universally sought-after practice for those looking to improve operational efficiency and waste reduction across various sectors. Lean management represents a systematic approach to identifying and eliminating waste through continuous improvement, thereby delivering value to customers. For aspirants looking to break into the dynamic world of lean management and coordination, a strategic approach is essential. This guide aims to equip you with the knowledge and steps necessary to build a career in this rewarding field.
Understanding Lean Principles
Before you embark on your lean journey, it's critical to fully understand the principles that underpin lean management. The core idea is to maximize customer value while minimizing waste. This means understanding the value stream for each product or service and eliminating any steps that do not add value. The five key principles of lean to grasp are defining value, mapping the value stream, creating flow, establishing pull, and pursuing perfection.
Defining Value: Understand what your customers truly value and are willing to pay for. This means having a deep insight into their needs and preferences.
Mapping the Value Stream: Identify all the steps in the process of delivering a product or service, and highlight which steps are non-value-adding, or 'waste.'
Creating Flow: After removing waste, ensure that the remaining steps flow smoothly without interruption, delay, or bottlenecks.
Establishing Pull: Rather than pushing products onto customers, a pull system ensures products are created in response to actual demand, preventing overproduction.
Pursuing Perfection: Lean is a continuous journey—not a destination. Always seek further improvements and engage in problem-solving.
Building a Lean Skill Set
While the theory behind lean principles is critical, practical skills are also essential in lean management. To make a mark in lean coordination, you should develop proficiency in the following areas:
Process Improvement: Gain expertise in identifying inefficiencies and reengineering processes to be more streamlined and cost-effective.
Project Management: Hone your ability to organize, plan, and execute lean projects with clear objectives and timelines.
Analytical Skills: Become adept at data analysis to measure performance and identify areas for improvement.
Teamwork and Communication: Learn how to effectively lead teams and communicate with stakeholders at all levels to drive lean initiatives.
Change Management: Prepare to navigate resistance and drive change across an organization by implementing lean techniques.
Gaining Relevant Experience
Hands-on experience is invaluable for breaking into the world of lean management. Consider these strategies to gain the necessary exposure:
Internship: Look for internships in organizations known for their lean practices. This provides an opportunity to observe lean management in action and contribute to real-world projects.
Volunteer Projects: Offer your skills to local businesses or non-profit organizations. This will allow you to practice lean methods and showcase your ability to produce tangible improvements.
Professional Networks: Join lean-focused groups or forums to connect with professionals in the field. Networking can lead to mentorship opportunities and potential job offers.
Continuous Learning: Stay updated with the latest lean methodologies by attending workshops, taking online courses, or earning certifications.
Pursuing Education and Certification
While it's possible to enter the field of lean management without a formal degree, education and certification can significantly enhance your credentials. Consider the following:
Degree Programs: Degrees in business management, industrial engineering, or operations research provide a strong foundation for a career in lean management.
Lean Certification: There are various lean certification programs available that cover essential skills and knowledge. Certifications from reputable organizations can set you apart from the competition.
Breaking into the Job Market
With a solid understanding of lean principles, a developed skill set, and relevant experience, you're ready to tackle the job market. Keep in mind these tips:
Tailored Resume: Ensure your resume highlights your lean management skills and experience. Use specific examples of how you've applied lean principles in practice.
Networking: Continue to expand your professional network. Attend industry events, join professional organizations, and engage on social media platforms.
Interview Preparation: Be ready to discuss your understanding of lean concepts and how you've applied them. Practicing case studies or problem-solving scenarios can be beneficial.
Staying on the Cutting Edge
The field of lean management is always evolving. Stay informed about new trends, tools, and technologies. Participate in continuous learning and be open to experimenting with innovative approaches to lean management. Keep the customer perspective central to your approach and always aim for a culture of continuous improvement within your organization.
Breaking into lean management is both challenging and rewarding. By following this guide, you have a roadmap to prepare yourself for success in this dynamic field. As you progress, remember that lean management is not just about tools and techniques; it's ultimately about people. Working with teams to cultivate a lean mindset will be pivotal in successfully coordinating and managing lean initiatives to drive value and efficiency.
Frequently Asked Questions
Frequently Asked Questions
What industries can benefit from implementing lean management?
Lean management principles can be applied across a wide range of industries, including manufacturing, healthcare, software development, construction, and service industries. Any sector that aims to improve operational efficiency, reduce waste, and deliver value to customers can benefit from implementing lean practices.
Is lean management only applicable to large organizations?
No, lean management principles can be implemented by organizations of all sizes. While large corporations often adopt lean practices to enhance their operations on a larger scale, small and medium-sized businesses can also benefit significantly from implementing lean techniques. The key is to tailor lean strategies to the specific needs and resources of the organization.
How long does it take to see tangible results from implementing lean management?
The timeline for seeing tangible results from implementing lean management can vary depending on factors such as the complexity of the organization, the extent of waste in processes, and the level of commitment to lean principles. In some cases, organizations may start seeing improvements in efficiency and quality within a few months of implementing lean practices, while significant transformations may take a year or more.
What are the common challenges faced when transitioning to lean management?
Transitioning to lean management can present several challenges, including resistance to change from employees accustomed to traditional methods, the need for extensive training and cultural shift within the organization, and ensuring sustained commitment from leadership. Overcoming these challenges requires clear communication, training programs, and a strong focus on continuous improvement.
How can individuals showcase their lean management skills during the job application process?
Individuals can showcase their lean management skills during the job application process by providing concrete examples of how they have applied lean principles to drive improvements in previous roles. These examples can be included in resumes, cover letters, and discussed during interviews to demonstrate practical understanding and experience in implementing lean methodologies.
Resources
Further Resources
For further exploration and in-depth understanding of lean management, here are some valuable resources to enhance your knowledge and skills:
- Lean Enterprise Institute: The Lean Enterprise Institute is a non-profit organization dedicated to advancing lean thinking and practice around the world. Explore their resources, workshops, and publications.
- Gemba Academy: Gemba Academy offers online lean and six sigma training, including videos, webinars, and certification programs. Enhance your lean knowledge through their practical courses.
- Toyota Production System: Beyond Large-Scale Production: This book by Taiichi Ohno, the father of the Toyota Production System, provides a deep insight into the principles and practices of lean management.
- Lean Thinking: Banish Waste and Create Wealth in Your Corporation: Written by James P. Womack and Daniel T. Jones, this book delves into the concepts of lean thinking and how to apply them in a business context.
- Harvard Business Review on Lean Management: Access a collection of articles from Harvard Business Review focusing on lean management practices and case studies. Learn from real-world examples of successful lean implementations.
- ASQ Lean Six Sigma Certification: The American Society for Quality offers comprehensive Lean Six Sigma certification programs for individuals looking to deepen their expertise in process improvement.
- Lean Construction Institute: If you are interested in lean principles applied to the construction industry, the Lean Construction Institute provides resources, events, and tools tailored to this sector.
- MIT OpenCourseWare - Lean Six Sigma Basics: Access free online course materials from MIT OpenCourseWare to learn the basics of Lean Six Sigma and its applications in various industries.
These resources offer a diverse range of insights and learning opportunities to further your journey into the world of lean management. Remember, continuous learning and application are key to mastering lean principles and driving sustainable improvement in organizations.