Lean Coordinator
A Lean Coordinator is responsible for streamlining operations by applying lean methodologies to improve efficiency and reduce waste in the production or service process.
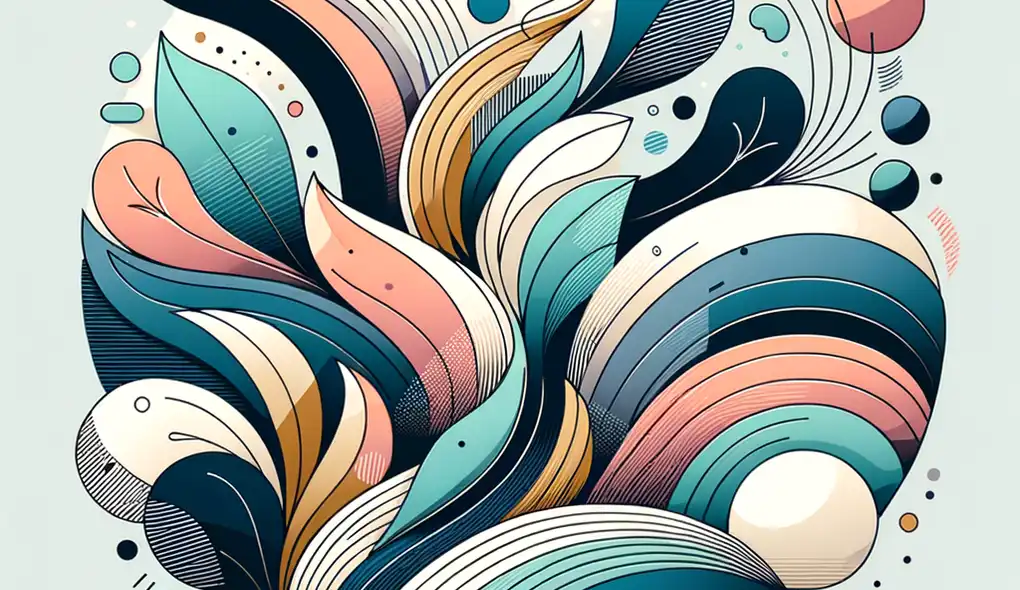
Top Articles for Lean Coordinator
Sample Job Descriptions for Lean Coordinator
Below are the some sample job descriptions for the different experience levels, where you can find the summary of the role, required skills, qualifications, and responsibilities.
Junior (0-2 years of experience)
Summary of the Role
The Lean Coordinator is an entry-level role focused on supporting the implementation and maintenance of lean manufacturing principles within an organization. The position entails assisting with the identification and elimination of waste, streamlining processes, and contributing to continuous improvement initiatives to enhance operational efficiency and quality.
Required Skills
- Knowledge of lean tools such as 5S, Kanban, and Value Stream Mapping.
- Time management and organizational skills.
- Basic project management capabilities.
- Assertiveness and ability to influence without direct authority.
- Flexibility to adapt to a dynamic work environment.
- Self-motivated with a strong desire to learn and grow professionally.
Qualifications
- Bachelor's degree in Engineering, Business Administration, or related field.
- Basic understanding of lean manufacturing principles and continuous improvement techniques.
- Strong analytical and problem-solving skills.
- Ability to communicate effectively with all levels of the organization.
- Proficient in Microsoft Office Suite, especially Excel.
- Ability to work collaboratively in a team environment.
Responsibilities
- Assist in implementing lean strategies and tools in the production environment.
- Support cross-functional teams in the identification and resolution of issues affecting efficiency and quality.
- Contribute to the maintenance of documentation related to lean processes and standard operating procedures.
- Help facilitate training sessions on lean principles and practices for employees.
- Participate in kaizen events and other continuous improvement activities.
- Analyze processes and data to identify areas for improvement and suggest actionable solutions.
- Collaborate with the Lean Manager and other team members to ensure coherent application of lean methodologies.
- Monitor the performance of lean initiatives and report on progress to management.
Intermediate (2-5 years of experience)
Summary of the Role
The Lean Coordinator is responsible for facilitating and leading continuous improvement initiatives in a manufacturing or service environment. This role involves identifying areas of waste, proposing innovative solutions to improve processes, and working closely with teams to implement changes that enhance productivity and efficiency.
Required Skills
- Proficient in Lean Six Sigma tools and techniques.
- Ability to lead and motivate teams.
- Knowledge of process mapping and value stream mapping.
- Proficient in data analysis and performance metrics.
- Excellent project management skills.
- Comfortable with change management processes.
Qualifications
- Bachelor's degree in Business Administration, Engineering, or related field.
- 2+ years of experience in a Lean or continuous improvement role.
- Demonstrated success in implementing Lean methodologies and achieving measurable results.
- Experience facilitating group workshops and training.
- Strong analytical and problem-solving skills.
- Excellent communication and interpersonal skills.
Responsibilities
- Drive continuous improvement initiatives using Lean methodologies.
- Collaborate with cross-functional teams to analyze processes, identify inefficiencies, and design solutions.
- Facilitate Lean workshops and training sessions to educate employees on Lean principles.
- Monitor and report on the progress of Lean projects, ensuring that objectives are met.
- Develop and maintain documentation related to process improvements and Lean activities.
- Serve as a change agent, encouraging a culture of continuous improvement throughout the organization.
- Work with leadership to align Lean initiatives with strategic business goals.
Senior (5+ years of experience)
Summary of the Role
The Lean Coordinator is responsible for leading and managing continuous improvement initiatives using Lean methodologies to enhance manufacturing and operational efficiency within the organization. This role calls for an experienced professional who can foster a culture of continuous improvement and work closely with various teams to identify areas of waste and develop strategies to improve processes and workflows.
Required Skills
- Lean methodologies
- Continuous improvement
- Process optimization
- Statistical analysis
- Project management
- Workshop facilitation
- Cross-functional collaboration
- KPI monitoring and control
Qualifications
- Bachelor's degree in Business, Engineering, or a related field.
- 5+ years of experience in Lean methodologies and continuous improvement.
- Proven track record of leading successful Lean transformation projects.
- Strong analytical skills and experience with statistical process control.
- Experience with Lean Six Sigma tools and techniques.
- Excellent project management and leadership skills.
- Ability to facilitate group workshops and trainings.
- Certification in Lean, Six Sigma, or continuous improvement is preferred.
Responsibilities
- Lead Lean strategy development and deployment across the organization.
- Execute Lean projects to improve process efficiency, reduce waste, and optimize performance.
- Facilitate Lean workshops and training sessions for staff at all levels.
- Monitor and report on Lean initiatives' progress and impact.
- Collaborate with cross-functional teams to identify process improvement opportunities.
- Develop and maintain standard work documentation and process maps.
- Drive sustainability of improvements by implementing control plans and monitoring KPIs.
- Guide and mentor team members in Lean principles and practices.
See other roles in Industrial, Construction, and Energy and Manufacturing