Shaping the Future: Emerging Technology Trends in Mold Making
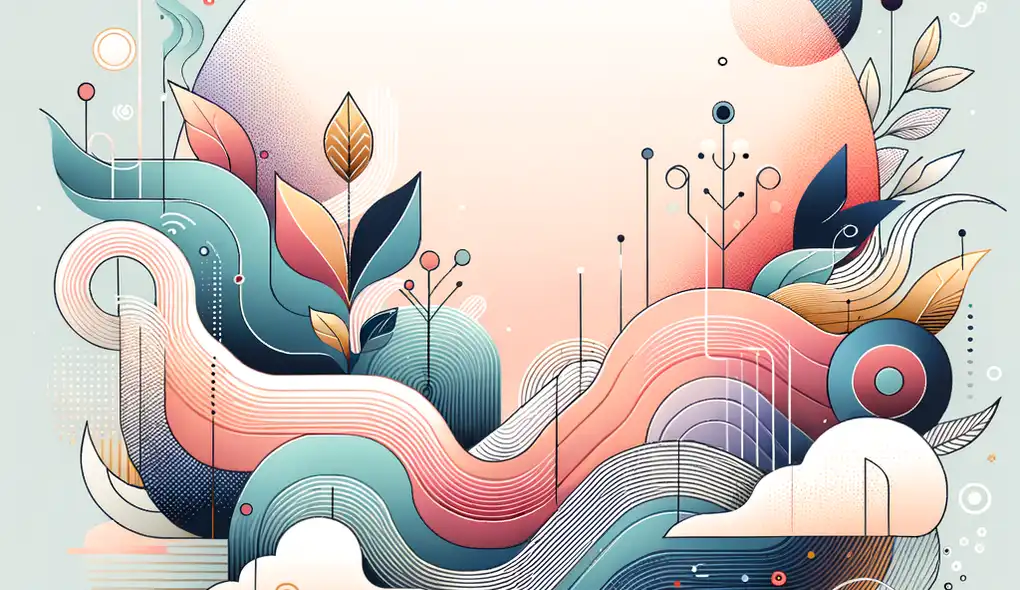
The mold making industry, a critical segment of modern manufacturing, has always been on the precipice of technological advancements. In a world constantly driven by demands for greater precision, speed, and cost-efficiency, mold makers are increasingly turning to emerging technologies to stay competitive. As we look to the future, several key trends have surfaced that are poised to not only shape the industry but to redefine it entirely. Here, we explore the most prominent of these trends and their implications for the future of mold making.
Integration of 3D Printing
Additive manufacturing, or 3D printing, has been making headway in various sectors, and mold making is no exception. The integration of 3D printing technology allows for the rapid prototyping of molds, enabling quicker turnaround times and the creation of more complex geometries that were previously impossible or costly with traditional methods. 3D-printed molds can be used for short runs or to test designs before mass production. The technology also supports the production of conformal cooling channels within molds, which can lead to more uniform product cooling, reduced cycle times, and improved overall part quality.
Advanced Materials
As the complexity of products increases, the need for advanced mold materials to withstand higher pressures and temperatures becomes paramount. Mold makers are exploring alternative materials such as high-performance polymers, composites, and new metal alloys that offer superior strength, durability, and thermal conductivity. Moreover, material innovations such as nanostructured metals can lead to molds with improved wear resistance, extending their life and reducing the need for frequent repairs or replacements.
Smart Molds with IoT Integration
The Internet of Things (IoT) heralds a new epoch for mold making, where smart molds equipped with sensors provide real-time data on their operational status. These sensors can measure various parameters such as temperature, pressure, and humidity, which are crucial for maintaining quality and efficiency. IoT-enabled molds can alert operators to potential issues before they become significant problems, optimizing maintenance schedules and minimizing downtime. Additionally, the data collected can be used for predictive analytics, allowing manufacturers to anticipate failures and plan interventions accordingly.
Automation and Robotics
Automation is not new to mold making, but advances in robotics and artificial intelligence (AI) are taking it to new levels. Robotic arms with enhanced precision are now capable of handling delicate tasks such as removing finished parts from molds or adding inserts during the molding process. AI algorithms can learn and adapt to production variances, automating quality control, and reducing the need for manual inspection. Automation increases productivity while ensuring consistent quality and reducing human error.
High-Precision Machining
CNC (Computer Numerical Control) machining continues to evolve, providing unprecedented levels of precision in mold manufacturing. High-speed machining techniques and precision cutting tools can now produce features with tolerances in the micron range. As a result, mold makers can achieve finer details and more accurate molds, which translates to better-fitting parts and less material waste. The combination of high-precision machining with advanced simulation software ensures that molds meet the exact specifications before they hit the production floor.
Sustainable Practices
Sustainability is increasingly becoming a consideration in all manufacturing sectors, and mold making is no different. There is a growing emphasis on using recyclable or biodegradable materials for molds, especially when producing disposable consumer goods. Energy-efficient machinery and practices that minimize waste are also gaining traction. By adopting more sustainable methods, mold makers not only reduce their environmental impact but also can often realize cost savings over time.
Customization and Personalization
With consumer demands for personalized products on the rise, the ability to create custom molds quickly is crucial. Advanced software and flexible manufacturing systems allow mold makers to switch between product runs with minimal downtime. Moreover, digital inventory and on-demand manufacturing mean that designs can be stored virtually and produced as needed, reducing the storage requirements for physical molds.
Collaborative Ecosystems
Finally, the future of mold making lies in building collaborative ecosystems where designers, engineers, manufacturers, and material suppliers work closely together. This collaboration drives innovation as insights and feedback throughout the production cycle help refine mold designs and manufacturing processes. Such ecosystems leverage digital platforms for communication and data sharing, ensuring all stakeholders are aligned and can contribute effectively to the development of cutting-edge molds.
In conclusion, the future of mold making is both exciting and transformative. The convergence of these technology trends has the potential to revolutionize the industry, leading to faster production times, increased customization, and improvements in both product quality and sustainability. For mold makers, staying ahead of the curve means embracing these developments, investing in new capabilities, and fostering a culture of innovation. By doing so, they can secure their place in a rapidly evolving industry landscape and continue to meet the ever-growing and changing demands of manufacturing.
Frequently Asked Questions
Frequently Asked Questions
1. What is the significance of 3D printing in mold making?
3D printing revolutionizes mold making by enabling rapid prototyping, complex geometries, and conformal cooling channels, leading to quicker turnaround times and enhanced part quality.
2. How do advanced materials impact mold making?
Advanced materials like high-performance polymers and nanostructured metals offer superior strength, durability, and thermal conductivity, catering to the increasing complexity of products and extending the lifespan of molds.
3. What are smart molds with IoT integration?
Smart molds equipped with IoT sensors provide real-time data on temperature, pressure, and humidity, optimizing maintenance schedules, minimizing downtime, and enabling predictive analytics for proactive interventions.
4. How are automation and robotics transforming mold making?
Automation powered by robotics and AI enhances productivity, quality control, and consistency in mold manufacturing by handling delicate tasks and automating quality inspection.
5. What role does high-precision machining play in mold making?
High-precision machining techniques driven by CNC technology ensure micron-level precision, finer details, and accurate molds, resulting in better-fitting parts and reduced material waste.
6. Why is sustainability important in mold making?
Sustainability considerations in mold making focus on recyclable or biodegradable materials, energy-efficient practices, and waste reduction, aligning with global trends towards environmental responsibility.
7. How does customization and personalization impact mold making?
The demand for personalized products drives the need for custom molds produced swiftly through advanced software and flexible manufacturing systems, reducing downtime and storage requirements.
8. What is the significance of collaborative ecosystems in mold making?
Collaborative ecosystems foster innovation through close collaboration among designers, engineers, manufacturers, and suppliers, leveraging digital platforms for communication and data sharing to refine mold designs and processes effectively.
Resources
Further Resources
For readers interested in delving deeper into the evolving landscape of mold making and the integration of emerging technologies in the industry, the following resources provide valuable insights and information:
- Society of Manufacturing Engineers (SME): The SME offers a range of publications, webinars, and events focused on advanced manufacturing techniques, including mold making and additive manufacturing. Society of Manufacturing Engineers
- Additive Manufacturing Industry Reports: Stay updated with the latest trends in additive manufacturing and its applications in mold making through industry reports and white papers. Additive Manufacturing Reports
- IoT in Manufacturing Webinars: Explore the integration of IoT in manufacturing processes, including smart molds and predictive maintenance strategies, by attending webinars hosted by experts in the field. IoT in Manufacturing Webinars
- Precision Machining Associations: Join precision machining associations and forums to connect with professionals in the field, share best practices, and stay informed about the latest advancements in CNC machining for mold manufacturing. Precision Machining Association
- Green Manufacturing Practices Guide: Learn about sustainable practices and green manufacturing initiatives that can be implemented in mold making to reduce environmental impact and improve operational efficiency. Green Manufacturing Guide
- Collaborative Design Software: Explore collaborative design software solutions that facilitate seamless communication and data exchange between stakeholders involved in mold making projects. Collaborative Design Tools
- Industry Trade Shows: Attend industry trade shows and exhibitions focused on mold making, automation, and additive manufacturing to network with industry experts, discover new technologies, and stay informed about market trends. Industry Trade Shows Calendar
- Continuous Learning Platforms: Enroll in online courses or training programs that cover topics such as materials science, robotics, and sustainable manufacturing to enhance your skills and stay competitive in the evolving mold making industry. Online Learning Platforms
These resources serve as valuable repositories of knowledge and insights for professionals and enthusiasts looking to explore the future of mold making through the lens of cutting-edge technologies and sustainable practices.