Safety First: Essential Safety Practices for Assembly Line Workers
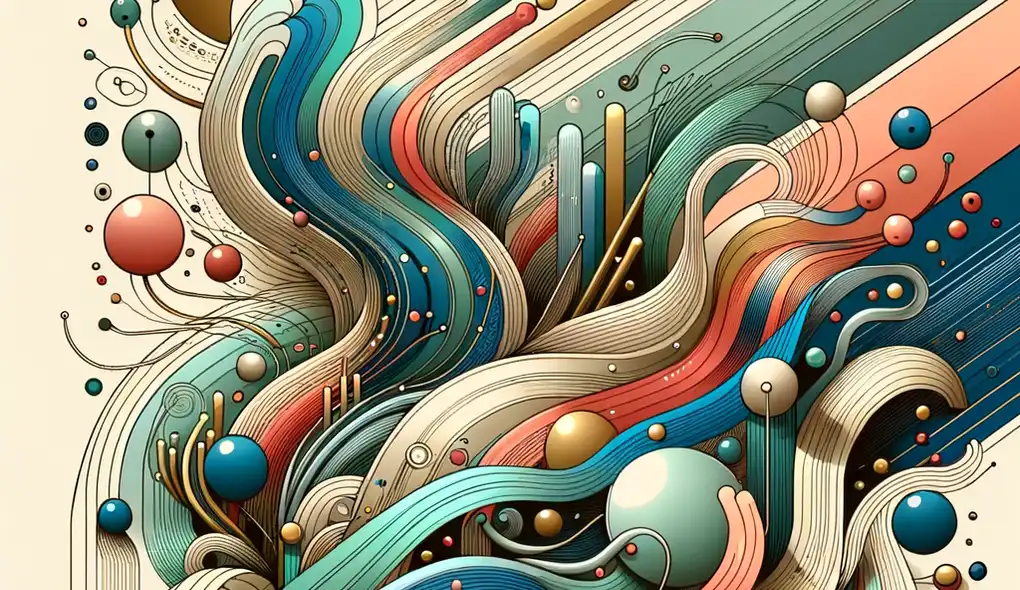
In the industrial landscape, assembly line work is known for its repetitive nature and fast-paced environment. Along with efficiency and productivity, safety is a paramount concern for workers and employers alike. In an assembly line setting, potential safety hazards range from ergonomic injuries due to repetitive motions to accidents involving machinery. Implementing essential safety practices and guidelines not only helps in preventing workplace injuries but also ensures that assembly line workers can operate in a secure and healthy work environment. Here's our comprehensive rundown of the most crucial safety practices for assembly line workers.
Understanding the Risks
The first step towards safety is understanding the risks inherent to assembly line work. The working environment can put assembly line workers at risk of various occupational hazards, including but not limited to:
- Repetitive Strain Injuries (RSIs): Activities that involve doing the same movements over and over can lead to strain and injury over time.
- Machine Entanglement: Workers can get clothing, jewelry, or parts of their body caught in machinery, resulting in severe injuries or fatalities.
- Slips, Trips, and Falls: Spills or irregularities on the floor can lead to accidental slips, trips, and falls.
- Hazardous Materials: Some assembly lines may involve exposure to hazardous materials, which can pose health risks.
- Noise Exposure: Chronic exposure to loud noise can result in long-term hearing damage.
Once the common risks are identified, both management and workers must take proactive steps to mitigate them.
Safety Training
Regular and comprehensive safety training is essential for keeping workers up-to-date with the latest safety protocols and responsive to potential dangers. Training sessions should cover:
- Correct operation of machinery and equipment.
- Proper lifting techniques to avoid back injuries.
- What to do in case of emergencies, including fire or chemical spills.
- Use of personal protective equipment (PPE).
- Identifying and reporting potential hazards.
Safety training should be continuous to refresh knowledge and cover new risks that may arise with changes in processes or technology.
Personal Protective Equipment (PPE)
PPE is vital in creating a barrier between the worker and potential hazards. Depending on the task and environment, PPE may include:
- Gloves: To prevent cuts or burns from handling materials.
- Safety Glasses or Goggles: To protect eyes from flying debris or chemical splashes.
- Ear Protection: To guard against noise-induced hearing loss.
- Respirators or Masks: To prevent inhalation of harmful dust, fumes, or vapors.
- Safety Shoes or Boots: To protect feet from falling objects or punctures.
Employers must provide the required PPE and ensure that workers are trained in their proper use and maintenance.
Ergonomics and Workstation Design
Considering ergonomics in the design of workstations can greatly reduce the risk of RSIs. Aspects to consider include:
- Adjustable workstations that fit the physical needs of individual workers.
- Tools and materials within easy reach to minimize excessive stretching or bending.
- Automation of excessively repetitive tasks wherever feasible.
- Frequent breaks to allow workers to rest and perform different movements.
Preventive Maintenance
Regular maintenance and inspections of assembly line machinery and tools prevent the occurrence of unexpected malfunctions that can lead to accidents. Maintenance protocols should ensure that:
- Machines are clean and in good working condition.
- Safety guards are in place and functional.
- All safety and emergency stops are easily accessible and operational.
Failure to maintain equipment can result in catastrophic failures and accidents.
Housekeeping
Good housekeeping is essential to prevent slips, trips, and falls. Immediate cleaning of spills, regular floor maintenance, and keeping walkways clear of obstructions are all part of a safe working environment.
Stressing the Importance of Reporting
A culture of safety is fostered when workers are encouraged to report hazards or near-misses without fear of repercussion. Quick responses to such reports can prevent accidents and improve overall safety.
Emergency Preparedness
Being prepared for emergencies is crucial. Drills should be conducted regularly, and clear evacuation routes and plans should be in place and known to all employees.
Teamwork and Communication
Safety is a team effort. Clear communication about safety protocols and changes, as well as peer support and vigilance, can make a substantial difference in maintaining a safe working environment. It also fosters a climate where safety is everyone's responsibility.
Continuous Improvement
Adopting a mindset of continuous improvement with regard to safety procedures means that practices are regularly reviewed and updated according to new information, technology changes, or process adjustments.
Conclusion
Safety in assembly lines is an ongoing commitment and requires the concerted efforts of both employees and employers. The guidelines provided are not exhaustive but offer a robust foundation for ensuring that assembly line workers are protected from risks. Remember, a safe workplace is a more effective and efficient one – safety always comes first.
Frequently Asked Questions
Frequently Asked Questions
1. What are the most common safety hazards for assembly line workers?
Assembly line workers are most commonly at risk of repetitive strain injuries (RSIs), machine entanglement, slips, trips, and falls, exposure to hazardous materials, and noise-induced hearing damage.
2. How important is safety training for assembly line workers?
Safety training is essential for assembly line workers to stay updated on safety protocols, emergency procedures, proper equipment usage, and hazard identification. Regular and comprehensive training is crucial for preventing workplace accidents.
3. What type of personal protective equipment (PPE) is typically required for assembly line work?
Depending on the task and environment, assembly line workers may need gloves, safety glasses or goggles, ear protection, respirators or masks, and safety shoes or boots to protect them from various hazards.
4. How can ergonomics and workstation design help reduce the risk of injuries?
Designing workstations with ergonomics in mind, including adjustable features, easy access to tools, automation of repetitive tasks, and regular breaks, can significantly reduce the occurrence of repetitive strain injuries among assembly line workers.
5. Why is preventive maintenance important for assembly line machinery?
Regular maintenance and inspections of assembly line machinery ensure that equipment is in good working condition, safety features are functional, and emergency stops are accessible. Preventive maintenance helps prevent unexpected malfunctions that could lead to accidents.
6. How does good housekeeping contribute to a safe working environment?
Maintaining good housekeeping practices, such as immediate cleaning of spills, regular floor maintenance, and keeping walkways clear, helps prevent slips, trips, and falls in the workplace, ensuring a safe environment for assembly line workers.
7. Why is it essential to foster a culture of reporting hazards?
Encouraging workers to report hazards or near-misses creates a safety-conscious workplace where issues can be addressed promptly, preventing accidents and improving overall safety for assembly line workers.
8. What should be included in emergency preparedness plans for assembly line facilities?
Emergency preparedness plans should include regular drills, clear evacuation routes, and communication of emergency procedures to all employees to ensure they are prepared to respond effectively in case of emergencies.
9. How can teamwork and communication promote a safe working environment?
Effective teamwork and clear communication about safety protocols and changes among assembly line workers help create a collaborative environment where everyone is responsible for maintaining safety standards, leading to a safer workplace.
10. Why is continuous improvement crucial for safety procedures?
Continuous improvement in safety procedures ensures that practices are regularly reviewed and updated to reflect new information, technological advancements, or process changes, enhancing the overall safety of assembly line operations.
Resources
Further Resources
For further information on safety practices for assembly line workers and to delve deeper into this crucial aspect of industrial work, here are some recommended resources:
- Occupational Safety and Health Administration (OSHA): OSHA provides comprehensive guidelines and resources for workplace safety, including specific regulations for assembly line operations. Visit OSHA's website for detailed information.
- National Institute for Occupational Safety and Health (NIOSH): NIOSH offers research and recommendations on occupational safety, including ergonomic practices and hazard prevention in assembly line work. Explore NIOSH's resources here.
- American Society of Safety Professionals (ASSP): ASSP is a professional organization that focuses on occupational safety and health. Their resources include articles, webinars, and conferences on safety practices. Learn more on the ASSP website.
- Safety+Health Magazine: This publication covers a wide range of safety topics, including articles specifically related to assembly line safety. Access their articles and archives on the Safety+Health website.
- Toolbox Talks for Workers: Toolbox talks are short safety meetings that are typically held at the start of a shift. They cover specific safety topics relevant to the work environment. Find toolbox talk resources and templates on Safety Toolbox Talks.
- Safety Equipment Suppliers: Consult with reputable safety equipment suppliers for the latest PPE and safety solutions tailored to assembly line work. Companies like 3M and Honeywell offer a wide range of safety products.
These resources provide valuable insights, tools, and guidance to enhance safety practices in assembly line operations. Stay informed and proactive in creating a safe working environment for all employees.