Understanding Quality Standards and Compliance: Essentials for Supplier Quality Engineers
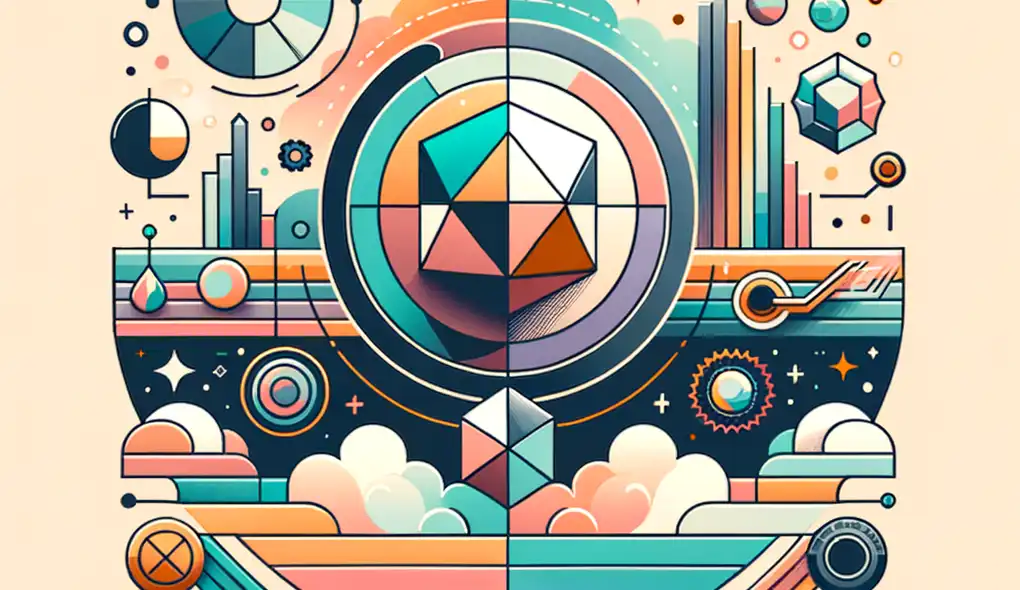
For supplier quality engineers, maintaining high standards of quality and ensuring compliance with relevant regulations is crucial. In the intricate world of supply chain management, quality and compliance go hand-in-hand, influencing everything from production efficiency to customer satisfaction and beyond. This article delves deep into understanding the core principles of quality compliance, which are vital for meeting industry standards and fulfilling customer expectations.
Defining Quality in the Supply Chain
Quality is a multifaceted concept that pervades every aspect of supply chain management. It defines the standard against which products and services are measured, ensuring that they fulfill customer demands reliably. For suppliers, it's about delivering products that are free from defects, meet specified performance criteria, and are produced in a sustainable and ethical manner.
Quality extends beyond physical products to include processes—the sequences of activities and procedures that produce the final product. A robust quality management system, therefore, not only focuses on the outputs but also thoroughly evaluates and optimizes each step taken to produce them.
Understanding Compliance
Compliance in supply chain management refers to the adherence to laws, regulations, standards, and ethical practices that apply to various sectors of the industry. For supplier quality engineers, it encompasses environmental laws, safety regulations, labor standards, and quality assurance protocols. Non-compliance can result in legal penalties, brand damage, and a loss of customer trust, making it imperative for businesses to stay updated and rigorously adhere to relevant standards.
International Standards and Frameworks
Internationally recognized standards such as ISO 9001 (Quality Management), ISO 14001 (Environmental Management), and ISO 45001 (Occupational Health and Safety) serve as benchmarks for companies striving to achieve excellence in their operations. These standards provide a systematic approach to managing quality, ensuring consistent products and services, reducing environmental impacts, and safeguarding worker safety.
Adopting these standards helps supplier quality engineers create a consistent approach to quality management across global supply chains, fostering continuous improvement and operational excellence.
The Role of Audits and Certifications
Regular audits are a central element in maintaining compliance and quality standards. These audits can be internal or external, with the latter often being mandatory for certification. During an audit, processes and products are scrutinized to ensure standards are being met. Supplier quality engineers play a significant role in preparing for these audits, addressing any non-conformities, and implementing corrective actions.
Certifications like ISO 9001 not only offer proof of a company's commitment to quality but also provide a market advantage. They demonstrate to customers and stakeholders that the supplier is dedicated to providing high-quality goods and services in a compliant and responsible manner.
Risk Management and Continuous Improvement
Supply chain management carries risks—be it from raw materials shortages, machinery breakdowns or fluctuating demand. A key responsibility of supplier quality engineers is to implement effective risk management strategies. This involves identifying potential risks, assessing their impact, and developing contingency plans to mitigate them.
Continuous improvement, a principle advocated by the Total Quality Management (TQM) philosophy, is about making ongoing efforts to improve products, services, or processes. These efforts can seek "incremental" improvement over time or "breakthrough" improvement all at once. Quality engineers need to foster an environment where feedback is actively sought and changes are implemented systematically to enhance quality and compliance.
Supplier Development and Relationship Management
In a globalized economy, it's not enough to simply monitor supply chain partners for compliance; it's also crucial to help them develop and improve. Providing guidance and training to suppliers strengthens the entire supply chain, resulting in better product quality and more reliable compliance.
Strong relationships with suppliers, built on transparency and mutual respect, enable more effective communication and problem-solving. Supplier quality engineers often serve as the mediators to resolve quality issues and ensure that suppliers understand and meet the required standards.
Technology's Role in Enhancing Quality and Compliance
As technology continues to advance, supplier quality engineers must leverage new tools and solutions to stay at the forefront of quality and compliance. Software for supply chain management, real-time monitoring systems, and automated quality control are becoming increasingly integral to modern supply chains. These technologies help to more efficiently track compliance, manage risks, and analyze data for improved decision-making.
Conclusion
Quality and compliance are not static targets but evolving challenges that require constant attention and adaptability by supplier quality engineers. By fully understanding the fundamentals of quality standards and compliance, professionals in the field can ensure that their companies not only meet but exceed the expectations set by customers, regulators, and the market at large. The synergy of robust frameworks, ongoing education, technological innovation, and strong supplier relationships is the key to a resilient and successful supply chain.
Frequently Asked Questions
Frequently Asked Questions
1. What are the key responsibilities of a supplier quality engineer?
Supplier quality engineers are responsible for ensuring that products meet defined quality standards, implementing quality control measures, conducting audits, managing supplier relationships, and continuously improving processes to enhance quality and compliance.
2. How important is compliance in supply chain management?
Compliance is critical in supply chain management as it ensures adherence to laws, regulations, standards, and ethical practices. Non-compliance can lead to legal consequences, damage to the brand reputation, and loss of customer trust.
3. What are some common international standards in quality management?
Some common international standards in quality management include ISO 9001 (Quality Management), ISO 14001 (Environmental Management), and ISO 45001 (Occupational Health and Safety). These standards provide guidelines for companies to achieve operational excellence.
4. Why are audits essential for maintaining quality and compliance?
Audits are essential for evaluating processes and products to ensure that they meet quality standards and comply with regulations. Regular audits help identify areas for improvement, address non-conformities, and demonstrate a commitment to quality to stakeholders.
5. How can technology support quality and compliance in supply chain management?
Technology plays a crucial role in enhancing quality and compliance by offering tools for real-time monitoring, data analysis, automated quality control, and supply chain management software. These technological solutions help streamline processes and ensure efficient compliance.
6. Why is supplier development important in supply chain management?
Supplier development is vital in fostering strong relationships, improving product quality, and enhancing compliance. By providing guidance and training to suppliers, companies can strengthen the entire supply chain and ensure consistent quality standards are met.
Resources
Further Resources
For further exploration of the topics covered in this article and to enhance your understanding of quality standards and compliance for supplier quality engineers, here are some valuable external resources:
1. ISO (International Organization for Standardization)
- Website: ISO Official Website
- Description: Access official information on a wide range of international standards relating to quality, environmental management, and occupational health and safety.
2. ASQ (American Society for Quality)
- Website: ASQ Official Website
- Description: ASQ offers certifications, training, and resources for quality professionals seeking to enhance their knowledge and skills in quality management.
3. ILO (International Labour Organization)
- Website: ILO Official Website
- Description: Explore global labor standards, safety regulations, and ethical practices set by the ILO to ensure fair treatment of workers worldwide.
4. Supply Chain Dive
- Website: Supply Chain Dive
- Description: Stay updated with the latest news, trends, and insights in the supply chain industry, including articles on quality management and compliance.
5. Quality Digest
- Website: Quality Digest
- Description: A source of quality-related articles, news, and resources catering to professionals interested in quality assurance and continuous improvement.
6. Lean Six Sigma Institute
- Website: Lean Six Sigma Institute
- Description: Learn about Lean Six Sigma principles and methodologies to drive quality improvements and operational efficiency in supply chain processes.
7. LinkedIn Learning
- Website: LinkedIn Learning - Quality Management Courses
- Description: Access online courses and tutorials on quality management, compliance, and risk mitigation strategies to enhance your professional skills.
8. Supply Chain Management Review
- Website: Supply Chain Management Review
- Description: Dive into in-depth articles, research papers, and case studies focused on supply chain management practices, including quality control and supplier development.