Staying Ahead: Key Trends in CNC Machining You Should Know
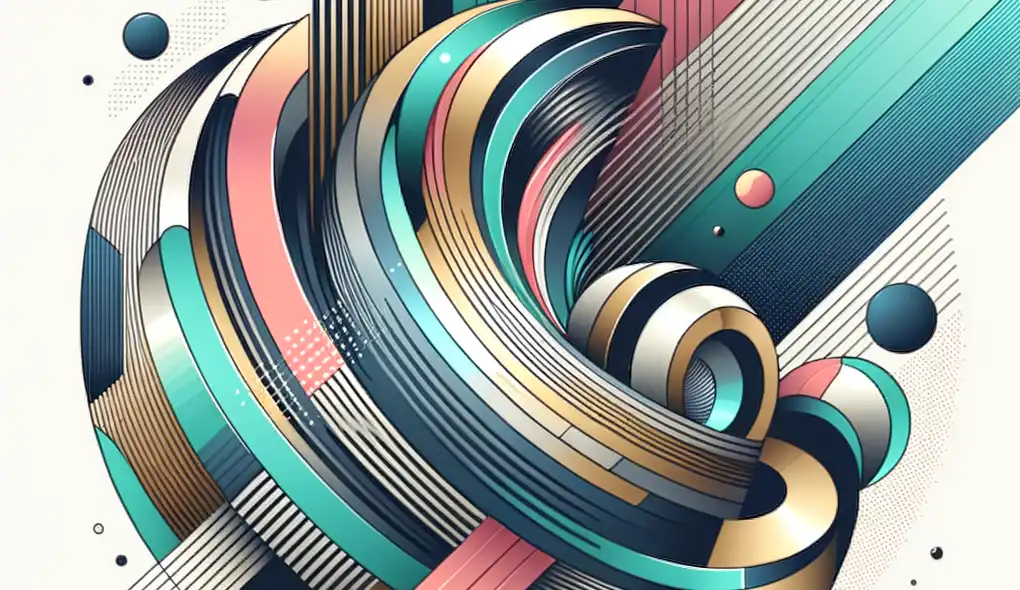
CNC (Computer Numerical Control) machining has long been a cornerstone in the manufacturing industry, enabling the precision creation of components for various applications, from aerospace to automotive to consumer electronics. As we tread further into the 21st century, technological advancements continue to push the boundaries of what is possible in CNC machining, inevitably affecting the roles and skillsets required from CNC machinists. In this article, we delve into the key trends in CNC machining and explore how they could impact the job of a CNC machinist.
Automation and Robotics
One of the most significant trends in CNC machining is the increasing use of automation and robotics. Automated tool changers, robotic arms, and fully autonomous CNC cells are becoming more commonplace. These advancements enable continuous operations, improving throughput and consistency while reducing manual intervention. As a machinist, embracing automation means focusing on programming, supervision, and maintenance of these systems, rather than manual operation of the machines.
Advanced Software and Simulation
The ability to simulate CNC machining processes in advance is becoming a game-changer. High-fidelity software can model and predict chip formation, tool paths, and potential collisions before a single cut is made. This allows for optimization of the machining process, saving time and material. Machinists now must be adept with this software, understanding how to interpret simulations and make appropriate adjustments.
Additive Manufacturing Integration
Traditionally separate disciplines, CNC machining and additive manufacturing are increasingly converging. Hybrid machines that can both subtractively machine and additively build up material open new possibilities for complex geometries and in-situ repairs. Machinists must understand the principles of both technologies to effectively operate these hybrid systems.
High-Speed Machining
Advancements in tool materials, coatings, and machining strategies have led to the rise of high-speed machining. This involves operating at higher speeds and feeds than previously thought practical. It can significantly reduce cycle times and produce finer finishes. CNC machinists need to comprehend the dynamics of high-speed operations to capitalize on these benefits.
Data Analytics and Machine Learning
Modern CNC machines generate a wealth of data. By harnessing machine learning algorithms, this data can be analyzed to predict machine failures, plan maintenance, and optimize processes. Machinists today are expected to engage with this data and contribute to decision-making processes informed by these advanced analytics.
Sustainability and Energy Efficiency
As global emphasis on sustainability grows, energy efficiency in CNC machining is attracting more attention. Innovations in this area include the use of renewable energy sources, resource-efficient coolant systems, and materials that reduce environmental impact. Machinists should be aware of these trends and understand how to operate machinery in a more sustainable manner.
Internet of Things (IoT) and Connectivity
The integration of IoT in CNC machining means machines are increasingly connected and communicative. This can streamline operations, allowing for remote monitoring and control. The role of the machinist evolves towards someone who is not only a machine operator but also a network technician, ensuring the seamless interaction of connected devices.
Training and Continuous Learning
Finally, with all the aforementioned trends, the demand for continuous learning is evident. CNC machinists must now commit to ongoing education to stay abreast of new techniques, software, and machinery innovations. The rapidly evolving industry landscape means that what was once cutting-edge knowledge can become obsolete in a matter of years.
In conclusion, the world of CNC machining is rapidly advancing, and CNC machinists must adapt to remain competitive in their field. Understanding and leveraging these key trends will not only ensure that machinists stay relevant but will also drive the manufacturing industry forwards, fostering innovation, efficiency, and quality in production. Staying ahead in the domain of CNC machining is a challenge but also an opportunity for those willing to learn and grow with the industry.
Frequently Asked Questions
Frequently Asked Questions
1. What is CNC machining?
Computer Numerical Control (CNC) machining is a manufacturing process that utilizes pre-programmed computer software to control the movement of machinery and tools in the manufacturing process. It enables the automatic and precise shaping of materials such as metal, plastic, wood, and composites to create intricate components and products.
2. How does automation impact CNC machining?
Automation in CNC machining involves the integration of robotic systems and automated processes to improve efficiency, consistency, and productivity in manufacturing operations. Automated tool changers, robotic arms, and CNC cells enhance the overall workflow by reducing manual intervention and enhancing precision.
3. What are the core skills required to become a CNC machinist?
To excel as a CNC machinist, fundamental skills in operating CNC machines, interpreting technical drawings, understanding machining processes, knowledge of CAD/CAM software, proficiency in tooling selection, and problem-solving abilities are essential. Additionally, adaptability to new technologies and continuous learning are key to staying relevant in the field.
4. How is additive manufacturing integrated into CNC machining?
Additive manufacturing integration in CNC machining combines subtractive and additive processes to create intricate geometries and functional parts. Hybrid machines capable of both machining and 3D printing offer versatility in material processing, allowing for complex designs and in-situ repairs.
5. What role does data analytics play in CNC machining?
Data analytics in CNC machining involves the collection, analysis, and interpretation of machine-generated data to optimize processes, predict maintenance needs, and improve efficiency. Machine learning algorithms enable predictive maintenance, real-time monitoring, and informed decision-making for CNC operations.
6. How can CNC machinists contribute to sustainability?
CNC machinists can contribute to sustainability by implementing energy-efficient machining practices, utilizing eco-friendly materials, recycling waste, and minimizing environmental impact. By adopting sustainable techniques and technologies, machinists play a crucial role in promoting environmentally conscious manufacturing.
7. What are the prospects for CNC machining in the future?
The future of CNC machining is promising, with continued advancements in automation, software integration, additive manufacturing, and connectivity. As industries evolve towards Industry 4.0, CNC machinists will play a vital role in driving innovation, enhancing production efficiency, and meeting the demands of a rapidly changing manufacturing landscape.
For more information and resources on CNC machining, refer to the following links:
Resources
Further Resources
For readers interested in delving deeper into the world of CNC machining and staying updated on the latest trends and technologies, the following resources provide valuable insights and learning opportunities:
- Modern Machine Shop: An online platform offering articles, videos, webinars, and case studies on CNC machining, automation, software, and industry trends.
- SME - Society of Manufacturing Engineers: SME provides a wealth of resources including training programs, certifications, events, and publications focused on manufacturing technologies, including CNC machining.
- FANUC CNC Training: Access specialized CNC training courses and resources directly from FANUC, a leading manufacturer of CNC systems and automation solutions.
- Makino Technology Webinars: Makino offers informative webinars on advanced machining technologies, high-speed machining, automation, and additive manufacturing integration.
- MIT OpenCourseWare - Manufacturing Courses: Explore free online courses from MIT covering topics such as manufacturing processes, automation, and digital manufacturing, providing a solid foundation for CNC machinists.
- Tooling U-SME: A comprehensive online training platform with courses tailored to CNC machining, tooling, programming, and maintenance skills.
- Industry Week: Stay updated on emerging CNC trends with in-depth articles, reports, and insights from experts in the manufacturing and technology sectors.
- Haas Automation Blog: Haas Automation's blog covers a range of topics including CNC programming, machine maintenance, and industry news, offering practical tips for CNC machinists.
- CNC Cookbook: An informative blog with resources on CNC machining techniques, software reviews, and machining productivity tips.
- American Machinist: Explore articles and insights on CNC machining, automation, tooling, and industry developments shared by industry professionals and experts.
These resources provide a blend of theoretical knowledge, practical insights, and industry updates essential for CNC machinists looking to stay abreast of the dynamic CNC machining landscape.