Mastering Injection Molding Techniques: A Guide for Operators
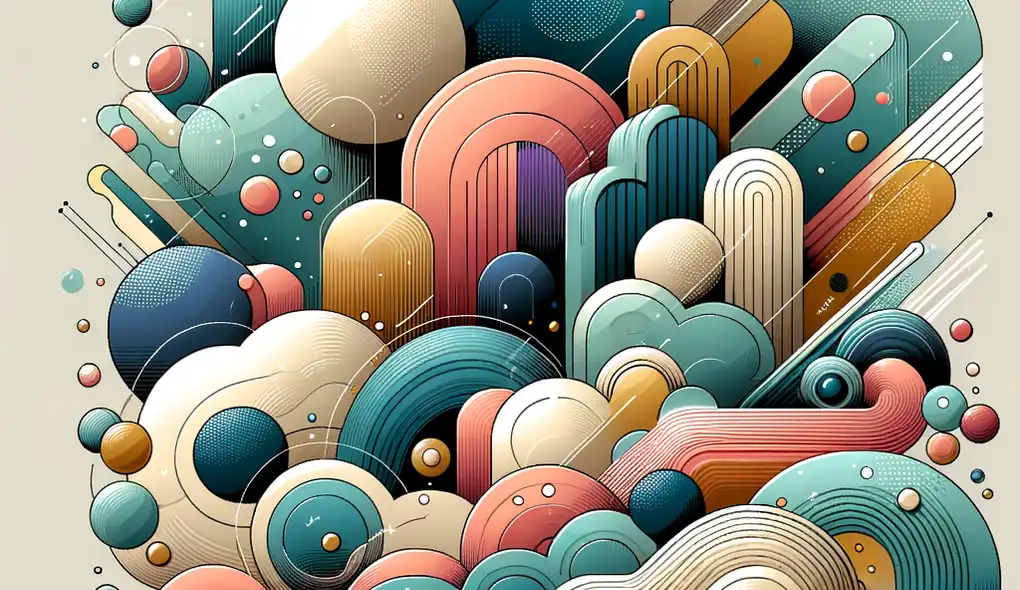
Injection molding is a versatile and widely-used manufacturing process that has become indispensable in the production of a vast range of products, from tiny electronic components to substantial automotive parts. Mastering injection molding techniques is critical for operators who wish to deliver consistent quality, optimize production efficiency, and minimize waste. This comprehensive guide will navigate through the essential techniques and best practices that can help injection molding operators achieve mastery in their field.
Understanding Injection Molding
Injection molding is a process in which molten plastic material is injected into a mold cavity under high pressure, where it cools and solidifies, taking on the shape of the mold. There are several key components in the process:
- The Injection Molding Machine: This consists of an injection unit, which heats and prepares the plastic material, and a clamping unit that opens and closes the mold.
- The Mold: Typically made from steel or aluminum, it is precision-engineered to form the desired product.
- The Raw Material: Thermoplastic or thermosetting polymers that are suitable for the product being manufactured.
Essential Techniques for Injection Molding Operators
- Material Preparation: Masterful injection molding begins with proper material preparation. This includes drying the material adequately to prevent defects in the final product caused by moisture, such as splay or bubbles.
- Machine Setup: Successful injection molding depends on precise machine setup, including selecting the right machine size for the part, configuring the correct material feed and heating temperatures, and ensuring the mold is securely fastened and aligned in the machine.
- Process Optimization: Operators should continuously monitor the process and make adjustments to the molding parameters—such as injection speed, pressure, and cooling time—to obtain the best results. Understanding the material’s behavior under different conditions is essential for this.
- Quality Control: Establishing robust quality control procedures helps detect and rectify problems early, ensuring that every part meets the required standards. This includes visual inspections, dimensional measurements, and functional tests.
- Maintenance and Troubleshooting: Regular maintenance of the injection molding machine and mold is necessary to prevent unexpected downtime and defects. Operators should be skilled in diagnosing and troubleshooting common issues, such as short shots, burn marks, or warping.
Advanced Skills for Mastery
- Design for Manufacturing (DFM): Operators with DFM knowledge can collaborate effectively with product designers to make modifications that facilitate easier and more cost-effective production.
- Automation and Robotics: As automation becomes more prevalent, understanding how to operate and maintain robotic systems for tasks such as part removal or inserting components into the mold, can significantly enhance production efficiency.
- Data Analysis: Mastery of injection molding also means being proficient in analyzing production data to identify trends, improve processes, and implement preventive measures against defects.
Continuous Learning and Adaptation
Mastery in injection molding is not a one-time achievement but a continuous process involving constant learning and adaptation. Operators should stay updated on new materials, technologies, and industry best practices. Participating in professional courses, attending industry conferences, and obtaining certifications can also contribute to an operator’s expertise.
In conclusion, mastering injection molding techniques requires a deep understanding of the entire process, from material preparation to the complexities of the molding machine, and beyond. By focusing on essential techniques such as machine setup, process optimization, and quality control, and by developing advanced skills like DFM, automation, and data analysis, operators can achieve excellence in their craft. Furthermore, a commitment to continuous learning and staying abreast of technological advancements will ensure that injection molding operators remain invaluable assets in the manufacturing industry.
Frequently Asked Questions
Frequently Asked Questions
What are the common defects that operators may encounter in injection molding?
Common defects in injection molding include sink marks, flash, warping, short shots, and splay. These defects can occur due to issues with material flow, mold design, machine setup, or processing parameters.
How can operators prevent defects in injection molding?
Operators can prevent defects by ensuring proper material preparation, optimizing machine setup, monitoring and adjusting process parameters, implementing robust quality control measures, and conducting regular maintenance on the machine and mold.
What are some key considerations when selecting an injection molding machine?
When selecting an injection molding machine, operators should consider factors such as the machine size and tonnage capacity, the type of material being used, the required injection pressure and speed, the mold size and complexity, and the level of automation needed.
How important is training and certification for injection molding operators?
Training and certification are crucial for injection molding operators, as they provide a solid foundation of knowledge and skills, ensure compliance with industry standards and best practices, and enhance job opportunities and career progression in the field.
What role does quality control play in injection molding?
Quality control is essential in injection molding to ensure that every part produced meets the required specifications and standards. It involves thorough inspections, measurements, and testing procedures to detect and rectify any defects or deviations from the desired outcome.
How can operators stay updated on the latest trends and technologies in injection molding?
Operators can stay updated by participating in industry conferences, workshops, and training programs, joining professional associations, reading industry publications, and networking with experts in the field. Continuous learning and knowledge sharing are key to staying informed and implementing new advancements in injection molding processes.
Resources
Further Resources
For readers interested in further enhancing their knowledge and skills in injection molding, the following resources provide valuable information and learning opportunities:
- Online Courses:
- Injection Molding Fundamentals - A comprehensive online course covering the basics of injection molding techniques and processes.
- Advanced Injection Molding Techniques - Explore advanced techniques and best practices in injection molding for experienced operators.
- Industry Publications:
- Plastics Technology - Stay up-to-date with the latest trends, technologies, and innovations in the plastics and injection molding industry.
- Injection World - Access in-depth articles and case studies on injection molding processes and applications.
- Professional Organizations:
- Society of Plastics Engineers (SPE) - Join a global network of plastics professionals and benefit from educational resources, conferences, and networking opportunities.
- Injection Molding Division of the SPE - A specialized division focusing on advancing the knowledge and skills of injection molding professionals.
- Books:
- Injection Molding Handbook by D.V. Rosato and M.R. Gsell - A comprehensive guide covering all aspects of injection molding, from design to troubleshooting.
- Robots in Injection Moulding by P.R.J. Kerwin - Learn about the integration of robotics in injection molding processes for improved efficiency.
- Webinars and Seminars:
- Understanding Injection Mold Design - Participate in webinars to deepen your knowledge of mold design principles and optimization.
- Advanced Process Monitoring Techniques - Explore advanced monitoring techniques for injection molding processes to enhance quality and efficiency.
By utilizing these resources, injection molding operators can continue to expand their expertise, stay informed about industry advancements, and refine their skills for greater success in the dynamic field of injection molding.