Staying Ahead: Emerging Trends in Manufacturing Engineering
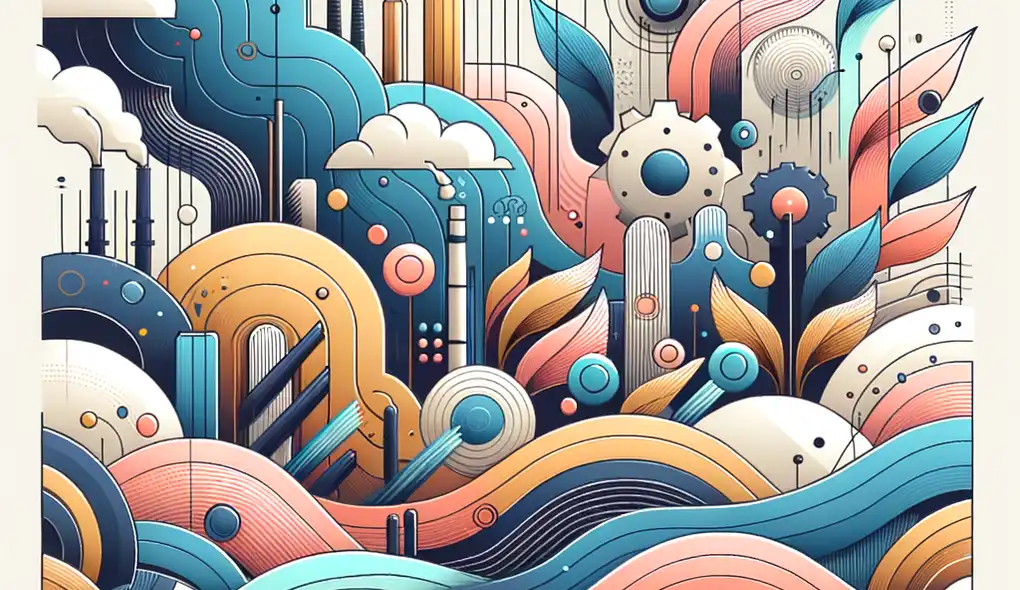
The landscape of manufacturing engineering is changing at an unprecedented rate. Driven by a combination of technological innovation, shifts in global markets, and the impact of environmental concerns, manufacturing engineers need to stay ahead of emerging trends to remain competitive and effective. This article delves into some of the most significant trends that are shaping the field of manufacturing engineering today and how professionals can adapt to these changes.
Advances in Automation and Robotics
Automation has been revolutionizing manufacturing for decades, but recent advancements in robotics and artificial intelligence (AI) have significantly accelerated this trend. Robots are becoming increasingly sophisticated, capable of performing complex tasks with a high degree of precision. Collaborative robots, or cobots, work alongside human workers, enhancing productivity and safety. AI-driven systems are enabling predictive maintenance, reducing downtime by anticipating equipment failures before they occur. Manufacturing engineers need to embrace these technologies, which can streamline production processes and lead to significant cost savings.
Additive Manufacturing and 3D Printing
Additive manufacturing, commonly known as 3D printing, is transforming the way products are designed and produced. It allows for rapid prototyping, customization, and the production of complex geometries that were once impossible to manufacture using traditional methods. Engineers must familiarize themselves with 3D printing technologies to push the boundaries of design and production efficiency. Moreover, the ability to produce parts on-demand can lead to inventory reduction and associated cost savings.
Sustainable Manufacturing
With an increasing focus on sustainability, manufacturing engineering is pivoting towards greener practices. There is a growing emphasis on using renewable energy sources, minimizing waste, and reducing the carbon footprint of manufacturing operations. Life-cycle assessments and eco-friendly materials are becoming more prevalent. Engineers will need to integrate sustainability into their workflow, balancing environmental concerns with economic viability.
The Internet of Things (IoT)
The integration of IoT technology into manufacturing processes, often referred to as the Industrial Internet of Things (IIoT), is enabling greater connectivity and data exchange between equipment and systems. This interconnectivity facilitates real-time monitoring and control, leading to improved efficiency and decision-making. Engineers should be adept at harnessing the potential of IoT to optimize production lines and supply chains.
Advanced Materials
New materials with enhanced properties are being developed at a rapid pace. These materials can offer superior strength, durability, and functionality while being lighter and more cost-effective. Engineers must stay current with these advancements to incorporate cutting-edge materials into their designs and processes.
Digitization and Smart Factories
The concept of smart factories, where everything is connected and automated, is becoming a reality thanks to advancements in digitization. Manufacturing engineers must understand digital tools and platforms that enable the analysis of large datasets, often referred to as big data, to drive efficiency and productivity. Machine learning algorithms can analyze these datasets to optimize manufacturing processes, reduce waste, and increase quality.
Customization and Mass Personalization
Consumers are increasingly seeking personalized products. The ability to customize items on a large scale, known as mass customization or mass personalization, is a growing trend. This requires flexible manufacturing systems and a deep understanding of customer preferences. Engineers need to design production processes that are both flexible and scalable to accommodate these demands.
Global Supply Chain Integration
In a globalized world, manufacturing is no longer confined to local or national borders. Engineers must consider the complexity of global supply chains when designing and optimizing manufacturing processes. The integration of advanced communication systems and transportation technologies is crucial for efficient global operations. Risk management and contingency planning are also becoming more essential due to the uncertain nature of international politics and trade.
Workforce Development
As new technologies emerge, there is a demand for a skilled workforce capable of operating, maintaining, and improving these systems. Manufacturing engineers should invest in continuous learning and development to keep their skills relevant. Additionally, they must play a role in educating and training the next generation of workers to ensure a seamless transition into these new technological paradigms.
Conclusion
Staying ahead in manufacturing engineering means continually adapting to new technologies and trends. By embracing automation, additive manufacturing, sustainable practices, IoT, advanced materials, digitization, mass customization, and global supply chain integration, engineers can ensure they are at the forefront of industry innovation. Moreover, investing in workforce development is essential to maintaining the momentum of progress. The future of manufacturing is exciting and full of challenges, but with a proactive approach, manufacturing engineers can thrive in this evolving landscape.
Frequently Asked Questions
Frequently Asked Questions
1. What are the key trends shaping the field of manufacturing engineering today?
The field of manufacturing engineering is currently experiencing significant transformation driven by technological advancements, sustainability initiatives, and the integration of digital technologies. Key trends include advances in automation and robotics, additive manufacturing, sustainable practices, IoT integration, the development of advanced materials, digitization of factories, customization trends, global supply chain integration, and the importance of workforce development.
2. How are automation and robotics impacting manufacturing engineering?
Automation and robotics play a crucial role in modern manufacturing engineering by streamlining production processes, enhancing productivity, and improving safety. The advancements in robotics and AI have led to the deployment of sophisticated robots, including collaborative robots (cobots), which work alongside human workers. These technologies enable predictive maintenance, reduce downtime, and lead to cost savings.
3. What is the significance of additive manufacturing (3D printing) in the manufacturing industry?
Additive manufacturing, particularly 3D printing, has revolutionized manufacturing by enabling rapid prototyping, customization, and the production of complex geometries. Engineers can leverage 3D printing technologies to push the boundaries of design and production efficiency, reduce inventory costs, and create novel products that were previously impossible using traditional manufacturing methods.
4. How important is sustainability in modern manufacturing practices?
Sustainability is a critical aspect of modern manufacturing practices as industries worldwide are shifting towards greener and eco-friendly operations. Manufacturing engineers are increasingly focusing on renewable energy sources, waste minimization, and reducing carbon footprints. Integrating sustainable practices into manufacturing workflows is essential to balance environmental concerns with economic viability.
5. What role does the Internet of Things (IoT) play in manufacturing processes?
The integration of IoT technologies, specifically the Industrial Internet of Things (IIoT), allows for enhanced connectivity and data exchange within manufacturing processes. IoT enables real-time monitoring, control, and data-driven decision-making, leading to improved efficiency, predictive maintenance, and optimized supply chains. Manufacturing engineers need to harness IoT to drive productivity and innovation.
6. How do advanced materials impact the field of manufacturing engineering?
The development of advanced materials with enhanced properties has significant implications for manufacturing engineering. These materials offer superior strength, durability, and functionality while being lightweight and cost-effective. Engineers need to stay updated on new material developments to incorporate cutting-edge options into their designs and manufacturing processes.
7. What are smart factories, and how do they contribute to manufacturing efficiency?
Smart factories are manufacturing facilities where automation, digitization, and data analytics are integrated to optimize production processes. Through digitization and the use of big data analytics and machine learning algorithms, smart factories can enhance efficiency, reduce waste, and improve product quality. Manufacturing engineers must understand and utilize digital tools to drive productivity and competitiveness.
8. How is mass customization changing the manufacturing landscape?
The trend of mass customization, or mass personalization, is reshaping the manufacturing landscape by catering to the growing demand for personalized products. Manufacturing engineers need to design flexible and scalable production systems to accommodate individual customer preferences on a large scale. Adapting to the customization trend requires a deep understanding of customer needs and the ability to tailor production processes accordingly.
9. What challenges arise from global supply chain integration in manufacturing?
Global supply chain integration presents complexities and challenges for manufacturing engineers due to the diverse nature of international operations. Engineers need to consider factors such as communication systems, transportation technologies, risk management, and contingency planning to ensure efficient global operations. The uncertain political and trade landscape emphasizes the importance of robust supply chain strategies.
10. How crucial is workforce development in the context of evolving manufacturing technologies?
Workforce development is essential for manufacturing engineers to navigate the evolving technological landscape and ensure optimal operation and maintenance of advanced systems. Continuous learning, upskilling, and training programs are necessary to keep pace with new technologies and innovations. Engineers play a pivotal role in educating and mentoring future generations to facilitate a seamless transition into the era of modern manufacturing.
Resources
Further Resources
For readers interested in delving deeper into the emerging trends in manufacturing engineering and staying ahead in this rapidly evolving field, the following resources provide valuable insights and information:
- Automation and Robotics
- Additive Manufacturing and 3D Printing
- Sustainable Manufacturing
- Internet of Things (IoT)
- Advanced Materials
- Digitization and Smart Factories
- Customization and Mass Personalization
- Global Supply Chain Integration
- Workforce Development
Explore these resources to stay informed, connected, and inspired in the evolving landscape of manufacturing engineering.