The Future is Here: Emerging Trends in Chassis Engineering
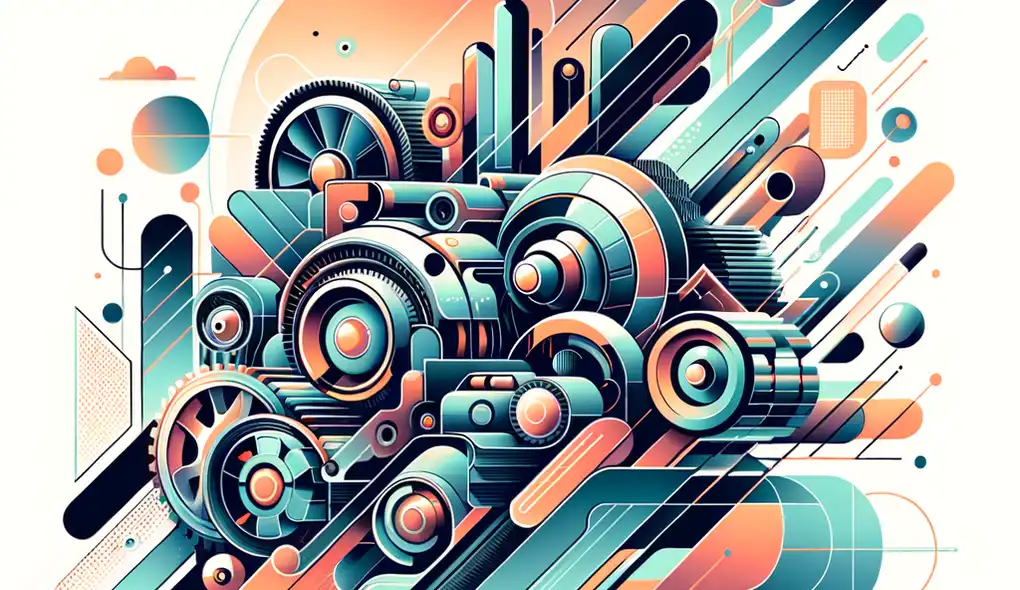
As we stand on the brink of unprecedented technological advances, the field of chassis engineering is experiencing a seismic transformation. Chassis, being the backbone of any vehicle, has historically been a focus for engineers seeking to balance strength, weight, and cost. However, emerging trends and technologies are reshaping this foundational component, promising vehicles that are not only more efficient and environmentally friendly but also deliver unprecedented performance and safety standards.
Advanced Materials and Composites
The quest for lighter, stronger, and more durable materials has ushered in an era of advanced composites in chassis engineering. Materials such as carbon fiber reinforced polymers (CFRP) are increasingly being used to create chassis that are substantially lighter than their metal counterparts, while still providing the requisite strength and rigidity. This weight reduction plays a crucial role in improving fuel efficiency and reducing emissions – vital considerations in the face of global climate change and stringent environmental regulations.
Magnesium and aluminum alloys are also at the forefront of this trend, offering a significant weight advantage over traditional steel. Research continues to evolve these alloys to enhance their performance characteristics, such as corrosion resistance and energy absorption in the event of a collision. Moreover, advancements in material science are leading to the creation of smart materials that can adapt their properties under different conditions, adding a new dimension to chassis functionality.
Adaptive and Active Chassis Systems
The concept of passive chassis has been replaced by active and adaptive systems that continuously adjust to driving conditions to provide optimal handling and ride comfort. These systems employ a variety of sensors and actuators that work in unison with the vehicle's electronic control unit (ECU) to modify suspension, steering, and other chassis-related functions in real-time.
Emerging from this is the predictive chassis technology that anticipates road conditions and driving situations to prepare the vehicle's response in advance. By integrating with advanced driver-assistance systems (ADAS) and vehicle-to-everything (V2X) communication, predictive chassis systems will provide a smoother, safer, and more controlled driving experience.
Electrification and Chassis Integration
The move towards electrification has been a game-changer for chassis engineering. Traditional internal combustion engine (ICE) powertrains are making way for electric motors that present unique opportunities for chassis design. The integration of battery packs within the chassis, known as a skateboard platform, allows for a flat floor and flexible interior space, creating a whole new paradigm for vehicle architecture.
This integration also aids in lowering the vehicle's center of gravity, which dramatically enhances handling and stability. Moreover, with the trend towards autonomous driving, the future chassis design will likely incorporate more space for onboard computers and sensors, further marrying technology with engineering in a seamless manner.
Modular Chassis Concepts
The automotive industry is witnessing a shift towards modular chassis platforms that can accommodate a wide range of models and body types. This approach not only reduces manufacturing complexity and costs but also allows for faster development cycles and easier updates to vehicle models. By sharing a common architecture, manufacturers can streamline production, cut down on resources, and adapt more swiftly to market demands or regulatory changes.
Future-Proofing with Digital Twins
Another exciting development in chassis engineering is the use of digital twins – virtual replicas of physical systems that can be used for design, analysis, and optimization. These sophisticated models enable engineers to simulate and test chassis designs under various conditions, reducing the need for physical prototypes and accelerating the development timeline. Digital twins also support predictive maintenance strategies, ensuring that vehicles remain safe and reliable throughout their operational life.
Sustainability and Lifecycle Management
As sustainable practices become more ingrained in the industry, lifecycle management of chassis is becoming a critical consideration. From design and manufacturing to end-of-life recycling, the focus is on minimizing environmental impact. New designs are being developed with disassembly and recyclability in mind, ensuring that once a vehicle reaches the end of its useful life, its materials can be recovered and reused.
Conclusion
The convergence of advanced materials, active systems, electrification, and digital innovations is catapulting chassis engineering into a new realm of possibilities. With sustainability and adaptability as guiding principles, the coming years will likely see vehicles that not only push the boundaries of performance and comfort but also tread lightly on the environment. As engineers and technologists continue to collaborate across disciplines, the chassis – the very foundation of every vehicle – will become a testament to the extraordinary potential of human ingenuity and the relentless pursuit of progress.
Frequently Asked Questions
Frequently Asked Questions
1. What are the emerging trends in chassis engineering?
Emerging trends in chassis engineering include the use of advanced materials like carbon fiber reinforced polymers, magnesium, and aluminum alloys, adaptive and active chassis systems, electrification and chassis integration, modular chassis concepts, and the implementation of digital twins for design and analysis.
2. How do advanced materials impact chassis engineering?
Advanced materials such as carbon fiber reinforced polymers contribute to lighter chassis, improving fuel efficiency and reducing emissions. Magnesium and aluminum alloys offer weight advantages and performance enhancements like corrosion resistance and energy absorption. Smart materials are also evolving to adapt properties under varying conditions.
3. What are adaptive and active chassis systems?
Active and adaptive chassis systems use sensors and actuators to adjust suspension and other functions in real-time for optimal handling and ride comfort. Predictive chassis technology anticipates road conditions, integrating with driver-assistance systems and V2X communication for a safer driving experience.
4. How does electrification impact chassis engineering?
Electrification replaces traditional ICE powertrains with electric motors, allowing for battery integration within the chassis known as a skateboard platform. This integration lowers the center of gravity, improving handling and stability. Future chassis designs are likely to accommodate additional space for autonomous driving components.
5. What is the significance of modular chassis concepts?
Modular chassis platforms enable a wide range of vehicle models and body types, reducing manufacturing complexity and costs. Shared architectures streamline production processes, facilitate quicker development cycles, and support adaptability to market changes.
6. How are digital twins revolutionizing chassis engineering?
Digital twins are virtual replicas used for design, analysis, and optimization, reducing the reliance on physical prototypes and accelerating development timelines. They also support predictive maintenance strategies, ensuring vehicle safety and reliability throughout their operational life.
7. Why is sustainability crucial in chassis lifecycle management?
Sustainability in lifecycle management focuses on minimizing environmental impact from design to end-of-life recycling. New chassis designs prioritize recyclability and disassembly, enabling the recovery and reuse of materials at the vehicle's end-of-life.
Resources
Further Resources
For readers interested in delving deeper into the evolving landscape of chassis engineering and the exciting trends shaping the future of vehicles, the following resources provide valuable insights and additional information:
- SAE International: The Society of Automotive Engineers offers a wealth of technical papers, standards, and resources related to chassis engineering and vehicle design.
- Composite World: Explore the latest advancements in composite materials, including carbon fiber reinforced polymers (CFRP), and their applications in chassis manufacturing.
- IEEE Xplore: Access cutting-edge research articles and publications on adaptive chassis systems, predictive technology, and electrification in vehicle design.
- Automotive News: Stay updated on the latest industry news, trends, and developments in modular chassis concepts and sustainable practices within the automotive sector.
- Digital Engineering: Dive into the world of digital twins and simulation technology for enhancing chassis design, analysis, and lifecycle management strategies.
- Green Car Congress: Explore the intersection of sustainability and vehicle electrification, with a focus on the environmental impacts and advancements in electric chassis integration.
- Automotive Engineering Magazine: Subscribe to this publication for in-depth articles, case studies, and expert insights on the future of chassis engineering and the automotive industry.
These resources serve as valuable references for professionals, enthusiasts, and students looking to stay abreast of the dynamic changes and innovations in chassis engineering.