Overcoming Challenges in Body-in-White Engineering
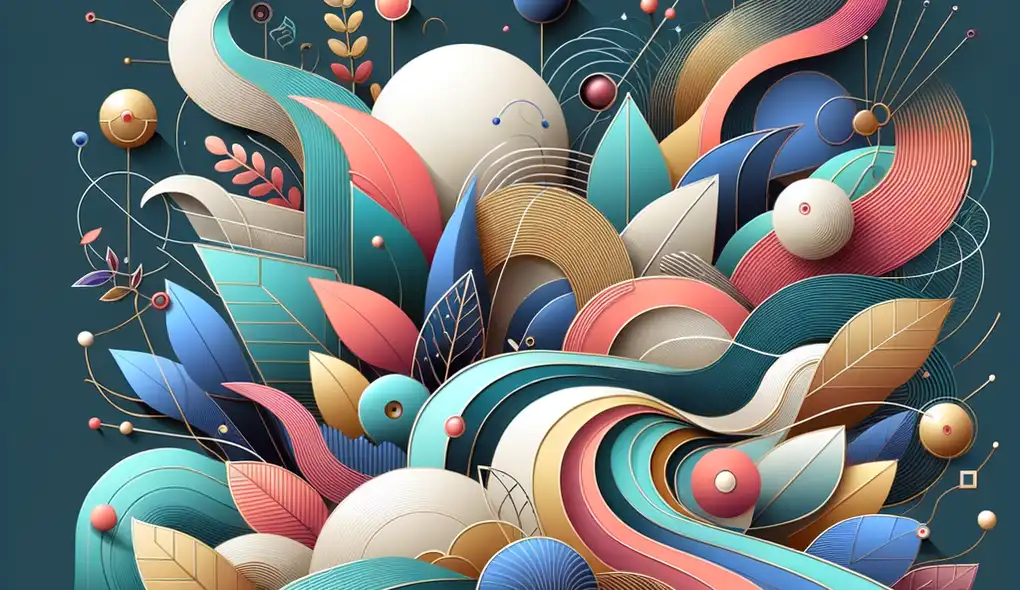
The realm of automotive design and manufacturing is renowned for intricacy and the relentless pursuit of perfection, particularly within the domain of Body-in-White (BIW) engineering. BIW refers to the stage in automotive design and manufacturing where the car's sheet metal parts have been welded together but before moving parts (like doors, hoods, and fenders), the engine, and the chassis are mounted. This stage is critical as it forms the structural core of the vehicle, setting the foundation for safety, durability, and performance standards that align with stringent industry regulations and customer expectations. The challenges faced by BIW engineers are multifaceted, and overcoming them necessitates a blend of technical acumen, strategic planning, and agile problem-solving skills.
Understanding the Stakes in BIW Engineering
The high stakes in BIW engineering stem from the weighty implications of every decision made. The BIW structure affects the vehicle's overall weight, which in turn influences fuel efficiency and emissions. It also impacts the vehicle's safety profile, with properly engineered crumple zones and structural integrity being crucial for absorbing and redirecting impact in the event of a collision. Furthermore, the BIW must be fashioned to accommodate not only current manufacturing techniques but also future innovations in automotive materials and assembly processes.
Common Challenges in BIW Engineering
Material Selection and Sustainability: BIW engineers often wrestle with material selection, striving for a balance between strength, weight, and cost. New materials like high-strength steel, aluminum, and carbon fiber composites present opportunities for lighter and stronger BIW structures but pose challenges in terms of cost and manufacturing complexity. Equally, there is an increasing demand for sustainability, compelling engineers to consider materials from a lifecycle perspective and to integrate recycling and circular economy concepts into their designs.
Manufacturing Precision and Quality Control: As the foundation for subsequent manufacturing stages, the BIW must be constructed with exceptional precision. Dimensional accuracy is crucial, and small errors can magnify throughout the assembly process, leading to fit and finish issues or even safety concerns. Quality control is paramount, with engineers employing advanced metrology tools and quality management systems to ensure that the BIW meets exacting standards.
Cost Constraints and Economic Pressures: Budgetary constraints are a constant in BIW engineering. Not only do materials and processes need to be cost-effective, but engineers also have to manage the economics of scale and return on investment for any new technologies or practices they wish to introduce. Operating within these financial parameters while still delivering innovative and robust BIW solutions is a delicate balancing act.
Integration with Other Systems: The BIW must seamlessly integrate with a multitude of other vehicle systems and components, necessitating close collaboration between multiple engineering disciplines. This integration challenge becomes even more complex with the rise of electric and hybrid vehicles, where the BIW has to accommodate battery packs and other new technologies without compromising on safety or performance.
Adaptability to Changing Regulations and Standards: Automotive regulations are constantly evolving, and BIW engineers must ensure their designs stay ahead of safety, emissions, and other regulatory benchmarks. This requires an ongoing process of monitoring, understanding, and adapting to new legislation, sometimes even before it becomes official.
Strategies for Overcoming BIW Engineering Challenges
Leveraging Technology and Simulation: One key strategy for addressing these challenges is leveraging cutting-edge computer-aided design (CAD) and simulation tools. Virtual prototyping and finite element analysis (FEA) allow engineers to test and refine their BIW designs extensively before any physical prototypes are built. These tools also enable engineers to anticipate and counteract potential issues related to materials, manufacturing, or interactions with other systems.
Collaborative Engineering Approaches: Cross-disciplinary teamwork is vital in a field that intersects with so many other engineering domains. Embracing a collaborative approach can foster innovation and ensure that diverse perspectives are brought to bear on complex challenges. Tools like integrated product teams and concurrent engineering can facilitate synchronization and streamline communication across departments.
Continuous Learning and Skill Development: Given the dynamic nature of the automotive industry, BIW engineers must commit to continuous learning and skill development. This involves staying abreast of new materials, technologies, and methodologies, as well as honing soft skills, such as project management and communication, that are crucial for interdisciplinary and cross-functional work.
Emphasizing Quality from the Start: By integrating quality control measures early in the BIW design process, engineers can mitigate risks related to manufacturing errors and design flaws. This 'quality by design' ethos necessitates a thorough understanding of the end-to-end production process and the implementation of robust checks and balances at every stage.
Proactive Engagement with Regulatory Changes: To navigate the evolving regulatory landscape, BIW engineers need a proactive approach. Engaging with industry groups, participating in standard-setting bodies, and even influencing policy can ensure that regulatory changes are anticipated and incorporated into design and production practices. This also helps to minimize reactionary adjustments, which can be costlier and more disruptive than proactive compliance.
By integrating these strategies into their approach, BIW engineers can successfully navigate the complexities and pressures of their field. Ultimately, this will contribute to the production of safer, more efficient, and more sustainable vehicles, benefiting both consumers and the broader environment.
In conclusion, overcoming challenges in BIW engineering is as much about embracing innovation and continuous improvement as it is about problem-solving. As the automotive industry continues to evolve, driven by technological advancements and societal demands, the role of BIW engineers becomes ever more pivotal. With a combination of strategic foresight, technical expertise, and a commitment to excellence, they are shaping the vehicles of tomorrow and defining new benchmarks in automotive design and manufacturing excellence.
Frequently Asked Questions
Frequently Asked Questions
What is Body-in-White (BIW) engineering?
Body-in-White (BIW) engineering refers to the stage in automotive design and manufacturing where the car's sheet metal parts have been welded together but before moving parts (like doors, hoods, and fenders), the engine, and the chassis are mounted. This phase is crucial as it forms the structural core of the vehicle, establishing the foundation for safety, durability, and performance standards in compliance with industry regulations and customer expectations.
What are the key challenges faced by BIW engineers?
BIW engineers encounter various challenges, including:
- Material Selection and Sustainability: Balancing strength, weight, and cost.
- Manufacturing Precision and Quality Control: Ensuring dimensional accuracy and quality standards.
- Cost Constraints and Economic Pressures: Managing expenses while delivering innovative solutions.
- Integration with Other Systems: Collaborating with different engineering disciplines for seamless integration.
- Adaptability to Changing Regulations: Staying ahead of evolving safety and emissions standards.
How can BIW engineers overcome these challenges?
BIW engineers can overcome challenges by:
- Leveraging Technology and Simulation: Using CAD and FEA for virtual prototyping.
- Collaborative Engineering Approaches: Encouraging cross-disciplinary teamwork.
- Continuous Learning and Skill Development: Stay updated with new technologies and methodologies.
- Emphasizing Quality from the Start: Integrating quality control measures early in the design process.
- Proactive Engagement with Regulatory Changes: Being proactive in addressing regulatory shifts.
Why is BIW engineering important in the automotive industry?
BIW engineering is vital as it establishes the structural core of vehicles, impacting weight, safety, and performance. It sets the foundation for vehicle durability, efficiency, and compliance with industry standards.
How do BIW engineers ensure sustainability in their designs?
BIW engineers promote sustainability by considering materials from a lifecycle perspective, integrating recycling and circular economy concepts, and exploring new materials like high-strength steel, aluminum, and carbon fiber composites.
What role does quality control play in BIW engineering?
Quality control is paramount in BIW engineering to ensure that the constructed BIW meets exacting standards for safety, durability, and performance. Engineers use advanced metrology tools and quality management systems to maintain dimensional accuracy and manufacturing precision.
Resources
Further Resources
For further exploration of Body-in-White (BIW) engineering and related topics, here are some valuable resources:
- Society of Automotive Engineers (SAE): The SAE provides a wealth of information on automotive engineering, standards, and best practices, including BIW engineering.
- Automotive Body Engineering Journal: This journal covers research and developments in automotive body engineering, offering insights into the latest trends and innovations.
- International Council on Clean Transportation (ICCT): Explore resources on clean transportation technologies and regulations that impact BIW engineering for environmental sustainability.
- National Institute for Automotive Service Excellence (ASE): ASE offers certification programs and resources for automotive professionals, including BIW engineers looking to enhance their skills.
- American Society for Quality (ASQ): ASQ provides resources on quality management, tools, and techniques that can benefit BIW engineers in ensuring the quality of their processes and products.
- Automotive Testing Technology International: Stay updated on the latest testing technologies and methodologies relevant to BIW engineering in the automotive sector.
- JSAE Review: The JSAE Review offers technical papers and research insights from the Japan Society of Automotive Engineers, covering diverse topics including BIW.
- LinkedIn Learning Courses: Access online courses on CAD, FEA, quality management, and other relevant topics to enhance your skills as a BIW engineer.
- Automotive News: Stay informed about the latest trends, industry news, and developments in the automotive sector, including BIW engineering advancements.
- Automotive Research and Development Centre (ARDC): ARDC offers resources for R&D in the automotive industry, providing insights into cutting-edge technologies and processes in BIW engineering.