Troubleshooting Tips for Truck Mechanics: Solving Common Problems
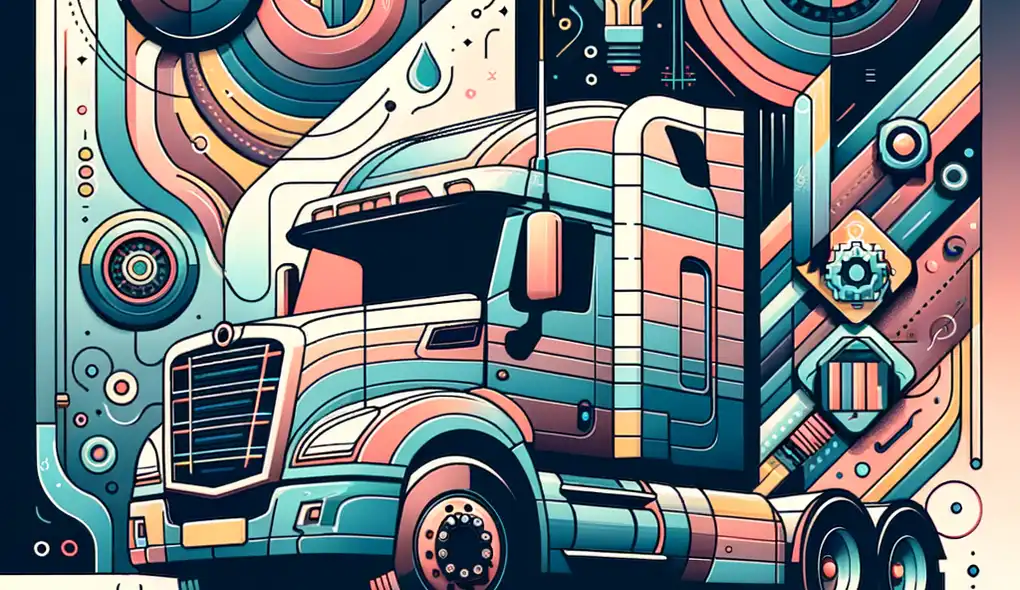
Truck mechanics face a myriad of challenges daily, as the robust nature of semi-trucks and other heavy vehicles entail complex mechanical and electrical systems. From engine malfunctions to faulty brake systems, a truck mechanic's job is to ensure that these heavy-duty vehicles remain in top condition for safe and efficient operation. To help mechanics address the common issues they encounter, this article compiles a range of troubleshooting tips that combine industry knowledge with practical strategies.
Understanding the Problem
The first step in troubleshooting is to gain a complete understanding of the problem. Listening to the driver's description and conducting a thorough visual inspection of the affected area can provide valuable clues. Look for signs of wear and tear, damage, or leaks. Observing how the truck behaves during operation - such as unusual noises, vibrations, or smoke - can also lead to quicker diagnostics.
Engine Issues
- Power Loss: When a truck experiences power loss, check for clogged fuel filters, air intake issues, or exhaust blockages. Scan for codes using diagnostic tools to pinpoint the area needing attention.
- Overheating: To address overheating, inspect the cooling system for leaks, check coolant levels, and ensure that the radiator and fan are functioning correctly. Cleaning out any build-up of dirt and debris in the radiator can help improve airflow and cooling efficiency.
- Engine Misfires: Engine misfires may be due to faulty spark plugs, damaged fuel injectors, or a malfunctioning ignition system. Use an OBD-II scanner to identify any fault codes that could guide the repair process.
Electrical Problems
Electrical issues in trucks are often related to battery and alternator problems. Start by testing the battery's voltage and inspecting cables for corrosion. The alternator should be checked for proper output, and all associated electrical connections should be secure and free from corrosion.
Brake Challenges
Brake problems can be particularly dangerous. For air brake systems, check for air leaks, worn out brake pads, and malfunctioning valves. Hydraulic brakes require attention to fluid levels and the quality of brake lines. If there is a problem with stopping power or brake responsiveness, the brake system may need to be bled to remove air from the lines.
Transmission and Drivetrain Issues
When the transmission or drivetrain is suspect, check for the correct level of fluid and its condition. Look for leaks and damage to the transmission casing. Don't overlook the importance of the clutch adjustment and operation in manual transmission trucks.
Suspension and Steering Problems
Truck suspension and steering systems bear heavy loads, making them prone to wear. Regularly inspect suspension components for damage or wear, particularly air suspension systems which can suffer from air leaks. For steering, ensure there's no excessive play or stiffness, and that all linkages are tight and lubricated.
HVAC Complications
In-cab comfort is crucial for drivers. If the HVAC system is not performing optimally, check for refrigerant levels, inspect hoses and connections for leaks, and test the compressor for proper operation. Keeping the cabin filters clean can also improve air quality and system performance.
Preventive Maintenance
Preventive maintenance is the cornerstone of truck mechanics. Regular inspections, fluid changes, and parts replacements can prevent many issues from arising. By adhering to a maintenance schedule and using high-quality parts, many troubleshooting scenarios can be avoided entirely.
Investing in Quality Tools
High-quality diagnostic tools and equipment can make a substantial difference in accurately diagnosing and resolving issues. Investing in the latest technology for diagnostics can save time and prevent recurring problems.
Continuing Education
Lastly, remaining informed about the latest industry technologies and repair techniques is crucial. Continuous learning through workshops, certifications, and networking with other professionals can enhance troubleshooting skills and lead to more efficient and effective repairs.
By integrating these troubleshooting tips into their workflow, truck mechanics can approach common problems with confidence and expertise. With a methodical approach, an investment in tools and knowledge, and a focus on preventive maintenance, truck mechanics will be well-equipped to keep vehicles operating at their best.
Frequently Asked Questions
Frequently Asked Questions
What are the common challenges faced by truck mechanics?
Truck mechanics often encounter issues such as engine malfunctions, brake problems, electrical issues, transmission and drivetrain issues, suspension and steering problems, HVAC complications, and more. These challenges require a comprehensive understanding of the complex systems in heavy-duty vehicles.
How can truck mechanics troubleshoot engine problems?
When facing engine issues like power loss, overheating, or misfires, mechanics should inspect fuel filters, cooling systems, spark plugs, fuel injectors, and ignition systems. Utilizing diagnostic tools to scan for codes can help pinpoint the root cause of the problem.
What should truck mechanics check for in electrical systems?
Electrical problems in trucks are commonly related to battery and alternator issues. Mechanics should test the battery's voltage, inspect cables for corrosion, check the alternator's output, and ensure all electrical connections are secure. Proper maintenance of the electrical system is crucial for reliable truck operation.
How can brake challenges be addressed?
For both air and hydraulic brake systems, mechanics should check for air leaks, worn brake pads, malfunctioning valves, fluid levels, and brake line quality. Bleeding the brake system may be necessary to restore stopping power and responsiveness. Brake issues should be promptly addressed to ensure safety on the road.
What preventive maintenance practices are essential for truck mechanics?
Preventive maintenance plays a vital role in ensuring the longevity and performance of heavy vehicles. Regular inspections, fluid changes, parts replacements, and adherence to maintenance schedules are key practices to prevent common issues from arising. By prioritizing preventive maintenance, mechanics can avoid costly repairs and downtime.
How important is investing in quality tools for truck mechanics?
High-quality diagnostic tools and equipment are essential for accurate troubleshooting and efficient repairs. Investing in the latest technology can save time, improve diagnostic precision, and enhance the overall service quality. Quality tools contribute to better outcomes and customer satisfaction.
Why is continuing education crucial for truck mechanics?
Staying updated on industry advancements and repair techniques is vital for professional growth and proficiency. By participating in workshops, obtaining certifications, and networking with peers, mechanics can expand their knowledge base and enhance their problem-solving skills. Continuous education enables mechanics to deliver high-quality services and stay competitive in the industry.
Resources
Further Resources
For further learning and reference, here are some valuable external resources that can enhance your knowledge and skills in truck mechanics:
- National Institute for Automotive Service Excellence (ASE): Access industry-standard certifications and resources for automotive professionals, including truck mechanics.
- Truck Mechanics Online Forum: Engage with a community of truck mechanics to discuss common issues, share tips, and seek advice on troubleshooting.
- Truck Repair Guides from Mitchell 1: Explore detailed repair manuals and guides for various truck models, covering diagnostics, maintenance, and repair procedures.
- Society of Automotive Engineers (SAE): Stay updated on the latest advancements in automotive engineering and technology through publications, events, and standards from SAE.
- Heavy-Duty Truck Parts Catalog: Access a comprehensive catalog of truck parts, components, and accessories for maintenance and repair needs.
- Online Courses on Truck Diagnosis and Repair: Enroll in online courses on truck diagnosis, troubleshooting, and repair techniques to expand your skill set.
- Professional Truck Technician's Toolbox: Discover recommended tools and equipment for truck technicians, along with reviews and comparisons to aid in your tool selection.
- Truck Fleet Maintenance Software: Explore digital solutions for fleet maintenance management, including preventive maintenance scheduling and tracking for commercial truck operations.
- Truck Mechanic Podcasts: Listen to podcasts dedicated to truck maintenance, repair tips, and industry insights to stay up-to-date on trends and best practices.
These resources offer a wealth of information and support for truck mechanics looking to excel in their profession and tackle troubleshooting challenges with confidence.