Driving Innovation: Trends in Advanced Drivetrain Engineering
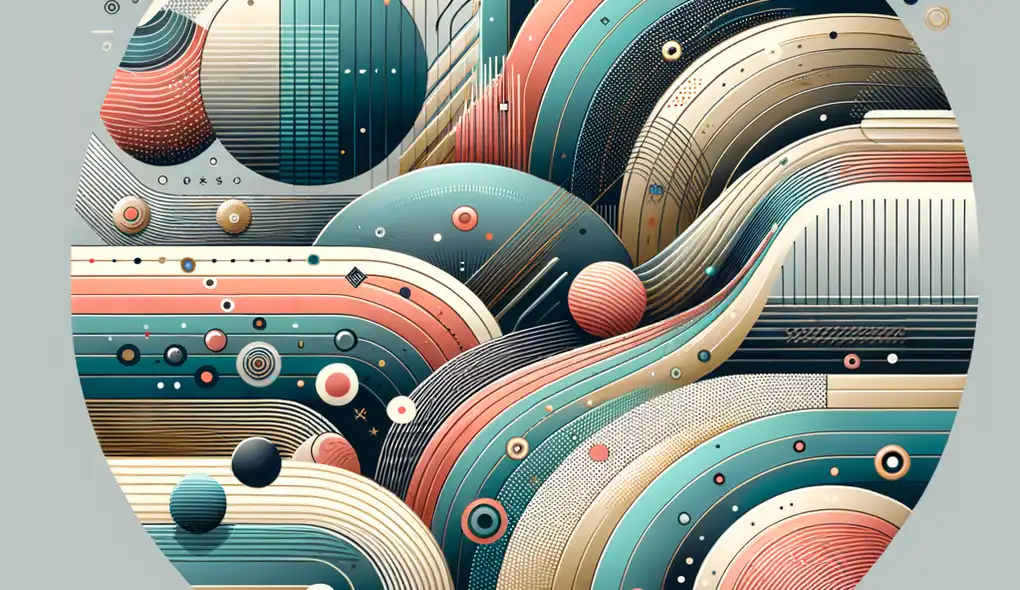
In the ever-evolving landscape of the automotive industry, the drivetrain has always been a critical cornerstone of vehicle design and performance. Today, as we stand at the cusp of a new transportation era marked by sustainability goals and technological advancements, there's a clear shift towards advanced drivetrain engineering. This transition is not just about enhancing performance but also about reducing environmental impact, ensuring energy efficiency, and providing a new level of driver experience. By delving into the latest trends and innovations in drivetrain technologies, we can glimpse the transformative changes that are driving the future of transportation.
Electrification of Drivetrains
One of the most significant shifts in drivetrain technology is the move towards electrification. Faced with increasingly stringent emissions regulations and a growing demand for sustainable mobility, manufacturers are focusing on electric vehicles (EVs) as the solution. This electrification trend has given rise to new designs for electric motors, power electronics, and battery systems that aim to increase range, decrease charging times, and improve overall vehicle efficiency. Innovative battery technologies, such as solid-state batteries, promise higher energy densities and improved safety over traditional lithium-ion batteries.
Integration of Powertrain and Vehicle Dynamics
Enhanced vehicle dynamics are now possible through the integration of powertrain technology with sophisticated chassis systems. This convergence enables more precise control over vehicle behavior and performance, contributing to safer and more enjoyable driving experiences. Systems like torque vectoring, which can distribute power variably between wheels, are no longer the preserve of high-end performance cars but are becoming more widespread across various vehicle segments. Advanced software and predictive algorithms are increasingly utilized to optimize these systems for diverse driving conditions.
Use of Lightweight Materials
A significant trend in drivetrain innovation is the use of lighter materials that can improve fuel efficiency and driving dynamics. Advanced materials such as carbon fiber, high-strength steel, and aluminum alloys have made their way into drivetrain components. The result is not just a reduction in vehicle weight but also an enhancement in the strength and durability of these components. The use of these materials can lead to a reduction in energy consumption as lighter vehicles require less energy to move.
Additive Manufacturing Techniques
Additive manufacturing, or 3D printing, is revolutionizing the way drivetrain components are designed and produced. By enabling the creation of complex shapes that are difficult or impossible to achieve with traditional manufacturing processes, 3D printing offers the potential for optimized component design with minimal waste. This not only has implications for cost and efficiency but also for customization, as it allows for small-scale production runs tailored to specific performance requirements.
Hybridization and Variable Transmissions
Hybrid drivetrains that combine internal combustion engines with electric motors are becoming more advanced with intelligent energy management systems that can switch between or combine power sources for optimal efficiency. Similarly, continuously variable transmissions (CVTs) and dual-clutch transmissions (DCTs) are growing in popularity due to their ability to deliver smooth power delivery and improved fuel economy. These technologies reflect a trend towards drivetrains that can adapt in real-time to driving conditions and driver inputs.
Autonomous and Connected Drivetrains
The rise of autonomous vehicles has given impetus to the development of drivetrains that can be more precisely controlled by computer systems. This has led to innovations in sensor technologies and actuators that allow drivetrains to respond to inputs from advanced driver-assistance systems (ADAS) and fully autonomous driving systems. This trend goes hand in hand with the connectivity revolution, where vehicles communicate with each other and with infrastructure to optimize driving patterns and energy usage.
Advanced Simulation and Testing
Improvements in computer simulation and virtual testing have drastically reduced the time it takes to develop and refine drivetrain systems. High-fidelity simulation allows engineers to experiment with various configurations and operating conditions before physical prototypes are ever built. This not only accelerates the innovation process but also helps ensure that the final products are thoroughly tested and refined.
Conclusion
These trends in advanced drivetrain engineering reflect a broader movement towards smarter, cleaner, and more adaptive vehicles. As technology continues to progress, the way we understand and interact with the drivetrain is fundamentally changing. Whether it's through the electrification of components, the integration of sophisticated control systems, the adoption of novel materials and manufacturing techniques, or the application of simulation technology, innovation in drivetrain engineering is redefining the performance and sustainability of tomorrow's vehicles. For automotive engineers, OEMs, and consumers alike, staying informed about these developments is essential to navigate the future of mobility.
Frequently Asked Questions
Frequently Asked Questions
1. What are the main benefits of electrifying drivetrains in vehicles?
Electrifying drivetrains in vehicles brings several advantages, including reduced emissions, increased energy efficiency, and overall improved performance. Electric vehicles (EVs) offer environmental benefits by eliminating tailpipe emissions and reducing dependence on fossil fuels. Additionally, electric motors provide instant torque, enhancing acceleration and driving dynamics.
2. How do lightweight materials contribute to drivetrain innovation?
The use of lightweight materials in drivetrain components helps improve fuel efficiency and driving dynamics. Materials such as carbon fiber, high-strength steel, and aluminum alloys reduce vehicle weight, leading to lower energy consumption. Additionally, these materials enhance the strength and durability of drivetrain components, ensuring optimal performance and longevity.
3. What role does additive manufacturing play in drivetrain design?
Additive manufacturing, also known as 3D printing, revolutionizes drivetrain component design by enabling the creation of complex shapes and structures. This technology allows for optimized designs with minimal waste, enhancing efficiency and customization. Manufacturers can produce unique components tailored to specific performance requirements, leading to innovative solutions in drivetrain engineering.
4. How do hybrid drivetrains and variable transmissions improve vehicle efficiency?
Hybrid drivetrains combine internal combustion engines with electric motors to optimize energy management and enhance efficiency. These systems can switch between power sources for optimal performance and fuel economy. Variable transmissions, such as continuously variable transmissions (CVTs) and dual-clutch transmissions (DCTs), offer smooth power delivery and improved fuel efficiency by adapting to driving conditions and driver inputs.
5. What impact do autonomous and connected drivetrains have on vehicle technology?
Autonomous and connected drivetrains enable precise control by computer systems, integrating sensor technologies and actuators for advanced driver-assistance and autonomous driving systems. These technologies allow vehicles to communicate with each other and infrastructure, optimizing energy usage and driving patterns. The rise of autonomous vehicles drives innovation in drivetrain engineering towards smarter and more adaptive vehicles.
Resources
Further Resources
For readers interested in exploring more about advanced drivetrain engineering and the future of transportation, the following resources provide in-depth insights and valuable information:
- Society of Automotive Engineers (SAE) International: SAE offers a wealth of technical papers, standards, and events focused on drivetrain innovations and automotive technology. Visit their website here.
- IEEE Xplore Digital Library: A comprehensive repository of research papers and articles on electric drivetrains, vehicle dynamics, and additive manufacturing in the automotive industry. Access IEEE Xplore here.
- Automotive Engineering: Online Magazine: Stay updated with the latest trends in automotive engineering, including drivetrain technologies, lightweight materials, and autonomous driving. Subscribe to the magazine here.
- National Renewable Energy Laboratory (NREL): NREL conducts research on advanced vehicle technologies, including electrification and lightweight materials, providing valuable insights for sustainable transportation. Explore NREL's research here.
- The Institution of Engineering and Technology (IET): IET's automotive network offers webinars, publications, and events covering a wide range of topics in drivetrain engineering and vehicle electrification. Learn more about IET here.
- Additive Manufacturing Society of India (AMSI): For enthusiasts of 3D printing and additive manufacturing in automotive applications, AMSI provides resources, workshops, and networking opportunities. Visit AMSI's website here.
- Automotive Testing Technology International: A source of information on the latest testing and simulation technologies for drivetrains and vehicle systems. Access their articles and reports here.
- The Future of Mobility - McKinsey & Company: Explore McKinsey's insights on the future of mobility, including trends in autonomous driving, connectivity, and energy efficiency. Read more here.
These resources offer a diverse range of perspectives and research findings to support your exploration of advanced drivetrain engineering and the transformative shifts in the automotive industry. Dive deeper into the world of drivetrain innovations and stay informed about the latest developments shaping the future of transportation.