The Impact of Technology on Quality Management
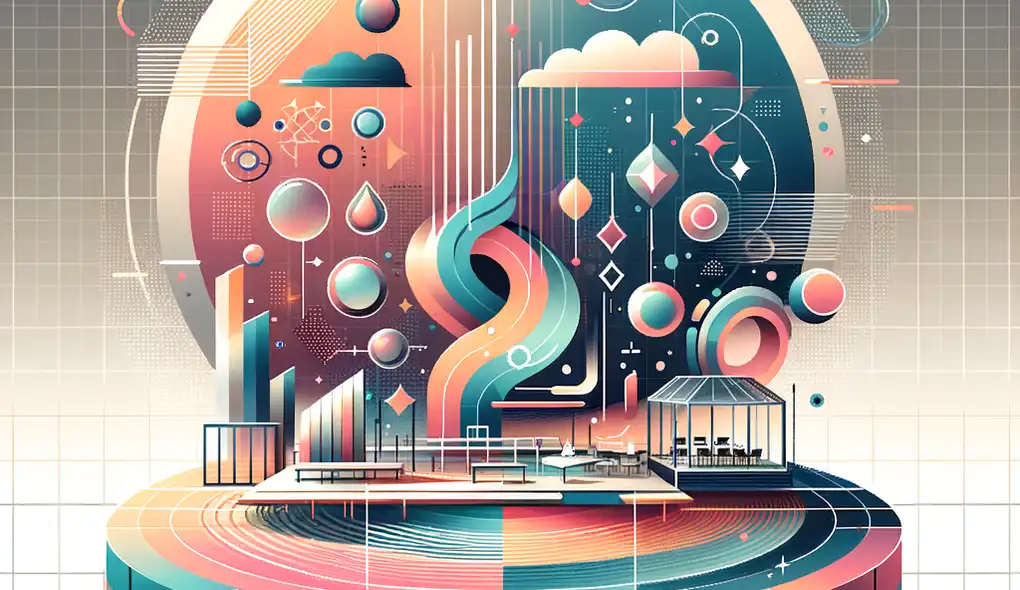
In the transformative landscape of modern business, technology plays an inexorable role not just in production and service delivery but also in the meticulous realm of quality management (QM). Quality Assurance (QA) Managers, hence, find themselves at the crossroads of traditional processes and high-tech solutions designed to ensure excellence and consumer satisfaction. The integration of innovative technologies into quality management systems (QMS) is not only reshaping the duties and possibilities of QA Managers but also redefining the horizons of product excellence and reliability.
The Evolution of Quality Management and Technology
Quality management has historically represented the gatekeeping function for product and service standards. In its embryonic stages, QA depended heavily on manual inspection and feedback mechanisms. However, the advent of technology has revolutionized this domain. Advanced software, automated systems, and data analytics have elevated QM from a reactive, inspection-based approach to a more proactive, preventative strategy. This evolution reflects in not only increased efficiency but also in the enhanced scope of QA Managers who now leverage sophisticated tools to diagnose and predict quality issues before they escalate into full-blown crises.
The Digital Toolbox for QA Managers
Forward-thinking organizations invest in a range of technologies to enhance their QMS. Data analysis tools, statistical software, and collaborative platforms enable QA Managers to track and analyze quality indicators across the entire production cycle. Automation and AI have introduced machine learning models that predict faults and facilitate preventive measures. Digital twins, which create virtual replicas of physical products or systems, allow for extensive testing without the constraints of real-world trials. In this high-tech era, the QA Manager’s toolbox is constantly expanding, necessitating a versatile understanding of these digital instruments.
Standardization and Compliance in the Technological Age
Regulatory compliance and standardization are critical components of QM. Modern technology facilitates a smoother process of adherence to international standards such as ISO 9001. Automated compliance systems ensure that every part of the production meets stringent guidelines and provides audit trails for transparency. QA Managers are thus charged with the critical role of integrating these systems into the workflow, ensuring compliance, and maintaining records with an unprecedented level of accuracy.
Big Data and Predictive Analytics
One of the most significant impacts on QM is big data analytics. QA Managers use data-driven insights to improve product designs, enhance customer satisfaction, and streamline operations. Predictive analytics, a subset of big data, offers potential algorithms for identifying the probability of future defects or failures. This proactive approach to quality allows for adjustments in real-time and reduces waste, delivering a more robust final product.
Enhanced Communication and Collaboration
Technology facilitates better communication and collaboration across various departments involved in QM. Shared databases and synchronization tools promote transparency and coherence, enabling various teams to work together seamlessly toward the singular goal of quality. QA Managers thus become the orchestrators of cross-functional teams, fostering an integrated approach to quality.
Remote Monitoring and IoT
The rise of the Internet of Things (IoT) and remote monitoring tools has seen quality assurance extend beyond the confines of a single location. QA Managers can now oversee production quality from virtually anywhere, with IoT devices providing real-time data on the performance of products and machinery. This capability has been especially beneficial in global operations, and during instances where physical presence is not viable.
Continuous Improvement and Agile Methodologies
Incorporating agile methodologies into QM processes allows for continuous improvement and adaptation. In sprints, smaller segmented operations can be monitored for quality, fostering a dynamic rather than static approach. For QA Managers, this translates to an ongoing process of learning and adapting technologies and methodologies to keep pace with the ever-changing demands of quality assurance.
Training and Development in Quality Management
With the increasing reliance on technological tools, QA Managers must also focus on the training and continuous professional development of their teams. This includes familiarizing them with new tools and systems, reinforcing a mindset of continuous improvement, and nurturing adaptability to change.
Challenges and Opportunities
The integration of technology in QM presents both challenges and opportunities. While it can improve accuracy and productivity, it also raises questions about cybersecurity, cost, and the potential loss of human elements in quality management. However, the opportunities for enhanced quality, efficiency, and customer satisfaction are profound.
Conclusion
The impact of technology on quality management is far-reaching and multifaceted. QA Managers stand at the vanguard of implementing innovative solutions that promise greater effectiveness and precision in quality assurance. The challenge lies in harmonizing technological advancements with the fundamental human insight that has always been at the core of quality management. In doing so, QA Managers will continue to play a pivotal role in defining the standards of excellence in an increasingly digital world.
Frequently Asked Questions
Frequently Asked Questions
1. How has technology changed the role of Quality Assurance Managers?
Technology has transformed the role of Quality Assurance (QA) Managers by shifting them from reactive, inspection-based approaches to proactive, preventative strategies. Advanced software, automated systems, and data analytics have enhanced efficiency and expanded the scope of QA Managers to diagnose and predict quality issues before they escalate.
2. What technologies are essential for QA Managers in modern quality management systems?
Forward-thinking organizations invest in data analysis tools, statistical software, automation, AI, digital twins, and collaborative platforms to enhance their Quality Management Systems (QMS). These technologies enable QA Managers to track quality indicators, predict faults, conduct extensive testing, and ensure compliance with regulations.
3. How does big data and predictive analytics impact Quality Management?
Big data analytics provide QA Managers with data-driven insights to improve product designs, enhance customer satisfaction, and streamline operations. Predictive analytics offers algorithms for identifying future defects or failures, allowing real-time adjustments and waste reduction.
4. How does technology facilitate communication and collaboration in Quality Management?
Technology enables better communication and collaboration among departments involved in Quality Management. Shared databases, synchronization tools, and IoT devices promote transparency, coherence, and real-time data sharing, fostering an integrated approach to quality across teams.
5. What are the challenges and opportunities of integrating technology in Quality Management?
While technology can enhance accuracy, productivity, and customer satisfaction, it also poses challenges such as cybersecurity risks, cost implications, and potential loss of human elements in quality management. However, the opportunities for enhanced quality and efficiency are significant.
Resources
Further Resources
For readers interested in delving deeper into the impact of technology on quality management, here are some valuable resources:
- Books:
- Quality Management for Organizations Using Lean Six Sigma Techniques by Erick C. Jones
- The Lean Six Sigma Pocket Toolbook: A Quick Reference Guide to Nearly 100 Tools for Improving Quality and Speed by Michael L. George
- Online Courses:
- Coursera offers courses like Quality Engineering and Management by Georgia Tech
- LinkedIn Learning provides courses on Quality Management Foundations by Kelley O'Connell
- Webinars and Podcasts:
- Quality Digest hosts webinars on various quality management topics
- The ASQ Podcast covers quality-related discussions and best practices
- Professional Organizations:
- The American Society for Quality (ASQ) offers a wealth of resources, certifications, and networking opportunities for QA professionals
- The International Organization for Standardization (ISO) website provides access to standards and guidelines for quality management
- Research Papers:
- Scholarly articles on platforms like IEEE Xplore and ResearchGate can offer in-depth insights into the latest technological advancements in quality management
- Blogs and Industry Websites:
- Quality Magazine publishes articles on quality control, standards, and technology trends
- IndustryWeek covers topics related to quality management, technology, and manufacturing
- Forums and Discussion Groups:
- Join quality management forums on platforms like Reddit or LinkedIn to engage in discussions with industry professionals
- Case Studies and Whitepapers:
- Explore case studies and whitepapers from leading companies like Toyota, GE, and IBM to understand real-world implementations of technology in quality management
By exploring these resources, readers can deepen their understanding of how technology is reshaping quality management practices and stay informed about the latest trends and innovations in the field.