Essential Safety Practices Every Chemical Operator Should Know
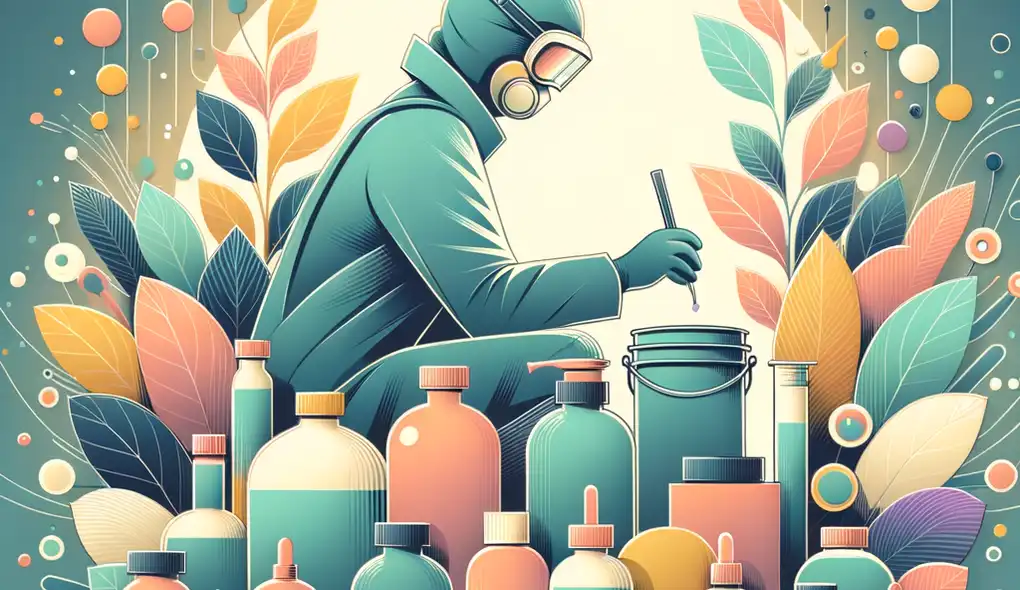
When it comes to working with chemicals, safety is of paramount importance. For chemical operators, understanding and implementing essential safety practices are not just a regulatory requirement but also a key element in preserving life, health, and the environment. This comprehensive guide will delve into the key safety practices and protocols crucial for chemical operators to prevent accidents and maintain a safe work environment.
Understand Chemical Properties and Hazards
Every chemical operator must be acquainted with the specific properties and associated hazards of the chemicals they handle. This includes understanding the chemical's reactivity, compatibility with other substances, flashpoints, toxicity levels, and environmental impact. Material Safety Data Sheets (MSDS) or Safety Data Sheets (SDS) provide essential information and should be reviewed and understood prior to handling any chemicals.
Personal Protective Equipment (PPE)
The use of appropriate PPE is critical. Chemical operators should be equipped with gloves, safety glasses or goggles, lab coats, and, if necessary, respiratory protection. Every piece of PPE must meet the required safety standards and be suitable for the type of chemical and the nature of the work being done. It is also crucial that PPE is regularly inspected and replaced when damaged or worn out.
Engineering Controls
Engineering controls, such as proper ventilation systems, fume hoods, and spill containment measures, should be in place to minimize exposure to hazardous chemicals. Regular maintenance and inspection of these systems are important to ensure they function correctly and effectively minimize risks.
Emergency Procedures and Training
Chemical operators must be trained in emergency response procedures. This includes knowledge of evacuation routes, spill response tactics, and the use of emergency showers and eyewash stations. Regular drills should be conducted to ensure that all workers know how to react swiftly and appropriately in the event of an accident.
Proper Labeling and Storage
Proper labeling of chemicals is essential for safety. Labels should include hazard symbols, chemical names, and handling instructions. Chemical storage must be planned carefully, considering factors like temperature stability, chemical compatibility, and secure containment. Segregating incompatible chemicals and storing flammables in dedicated cabinets are basic practices for preventing dangerous reactions or fires.
Chemical Handling Procedures
Safe handling procedures for chemicals should be outlined clearly and followed rigorously. This includes using the correct tools and methods for transferring chemicals, avoiding cross-contamination, and ensuring that all containers are sealed properly after use. It's also essential to prohibit food and drink in areas where chemicals are handled to prevent ingestion of hazardous substances.
Communication and Signage
Effective communication and clear signage are vital for preventing accidents. Safety signs should be prominently displayed, indicating potential hazards and reminding workers of the necessary safety precautions. All chemical operators should be aware of the significance of these signs and follow the instructions they convey.
Regular Safety Audits
Conducting regular safety audits is a proactive approach to identifying potential risks before they result in an incident. Audits should assess the conditions of work areas, the state of PPE and engineering controls, and the adherence to safety protocols. Any weaknesses in safety practices must be addressed immediately to uphold the highest standards of safety.
Health Monitoring
Regular health monitoring of chemical operators can identify early signs of exposure to harmful substances. Monitoring may include medical examinations, blood tests, and other relevant screenings. This practice helps in the early detection of occupational illnesses and ensures that safety measures are adequate and effective.
Continuous Education and Improvement
Finally, safety is an evolving field, and continuous education is necessary. Chemical operators should stay informed about the latest safety practices, equipment innovations, and industry regulations. Organizations should foster a culture of safety where feedback and suggestions for improvements are welcomed and implemented.
In conclusion, effective safety practices in chemical operations are multifaceted, requiring a combination of knowledge, vigilance, and organizational support. By following these essential practices and continuously striving for improvement, chemical operators can create a safer work environment that protects themselves, their colleagues, and the world around them.
Frequently Asked Questions
Frequently Asked Questions
1. What are the key safety practices every chemical operator should follow?
Chemical operators should prioritize understanding chemical properties and hazards, using appropriate PPE, implementing engineering controls, and being trained in emergency procedures. Proper labeling and storage, adherence to handling procedures, effective communication, regular safety audits, health monitoring, and continuous education are also crucial.
2. How important is PPE in chemical operations?
Personal Protective Equipment (PPE) is vital in chemical operations to protect operators from exposure to hazardous substances. PPE includes gloves, safety glasses, lab coats, and respiratory protection when necessary. Ensuring that PPE meets safety standards, is regularly inspected, and replaced when damaged is essential for operator safety.
3. Why is it important to understand chemical properties and hazards?
Understanding chemical properties and hazards is critical for chemical operators to prevent accidents and protect themselves, their colleagues, and the environment. Knowing the reactivity, toxicity, and environmental impact of chemicals helps in safe handling and storage practices.
4. What should be considered when storing chemicals?
Chemical storage requires careful planning considering temperature stability, chemical compatibility, and secure containment. It is essential to label chemicals correctly, segregate incompatible substances, and store flammables in designated cabinets to prevent dangerous reactions or fires.
5. How often should safety audits be conducted in a chemical facility?
Regular safety audits should be conducted in chemical facilities to proactively identify potential risks. These audits assess work area conditions, the state of PPE and engineering controls, and overall adherence to safety protocols. Any shortcomings in safety practices should be promptly addressed to maintain a high standard of safety.
Resources
Further Resources for Chemical Operator Safety
For further reading and resources on chemical operator safety, here are some valuable links:
- Occupational Safety and Health Administration (OSHA): OSHA provides detailed guidelines and regulations for chemical safety in the workplace.
- National Institute for Occupational Safety and Health (NIOSH): NIOSH offers extensive resources on chemical hazards, exposure assessments, and PPE recommendations.
- American Chemical Society (ACS) Safety Guidelines: ACS provides safety guidelines specific to chemical laboratories and operations.
- Chemical Safety Board (CSB): CSB investigates chemical accidents to improve safety and prevent future incidents.
- Center for Chemical Process Safety (CCPS): CCPS offers tools and resources for chemical process safety excellence.
- Chemical Emergency Preparedness and Prevention Office (CEPPO): CEPPO provides resources for chemical emergency preparedness and response planning.
- Chemical Watch: A source for global regulatory news and expert insights on chemical safety and compliance.
- European Chemicals Agency (ECHA): ECHA offers guidance on the safe use of chemicals in the European Union.
- American Industrial Hygiene Association (AIHA): AIHA provides resources and training for industrial hygiene and chemical exposure monitoring.
- Chemical Safety Manual by the University of Rhode Island : A comprehensive manual covering chemical safety protocols and best practices.
These resources cover a wide range of topics related to chemical safety, from regulations and guidelines to practical tools for implementing safe practices in chemical operations. Continual learning and staying updated with industry standards are crucial for maintaining a safe work environment for chemical operators.