Staying Ahead: Quality Systems Management Trends and Innovations
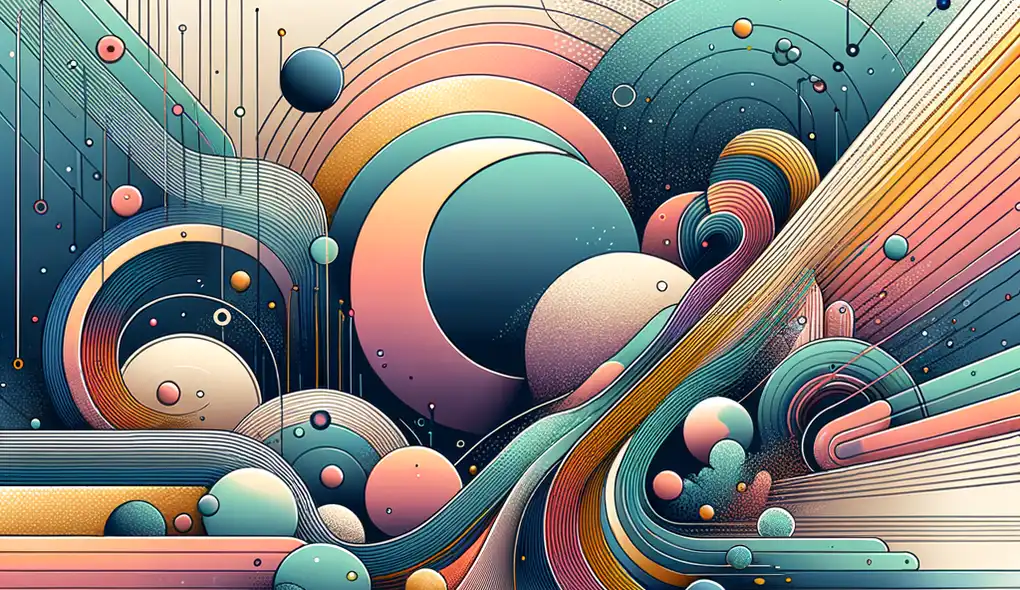
In today's fast-paced and ever-evolving business environment, staying ahead of the curve in Quality Systems Management (QSM) is crucial for organizations aiming to maintain a competitive edge. Quality Systems Management encompasses the strategies and tools used to ensure that products, services, and processes meet consistent standards and customer expectations. The field is continuously influenced by technological advancements, regulatory changes, and new management theories, making it vital for quality professionals to keep up with the latest trends and innovations.
Harnessing Technology to Improve Quality Systems
One significant trend is the increasing use of technology to enhance quality systems. Software solutions that automate and integrate various aspects of quality management are becoming more advanced and accessible. For example, AI and machine learning algorithms can now predict potential quality issues before they occur, allowing for proactive measures to be taken. Similarly, Big Data analytics can be leveraged to analyze vast amounts of quality-related data, leading to more informed decision-making.
Real-time monitoring systems are another technological innovation gaining traction. These systems use sensors and Internet of Things (IoT) devices to continuously collect data from the production floor, supply chain, or customer interactions. The instant feedback allows for immediate corrective actions, thus reducing the risk of quality failures and improving overall efficiency.
Embracing ISO Standards and Regulatory Shifts
Adherence to international standards, such as those set forth by the International Organization for Standardization (ISO), remains a cornerstone of robust quality systems. Recent updates to standards like ISO 9001 emphasize a greater focus on risk management and leadership engagement. Companies that stay up-to-date with these standards not only meet compliance requirements but also align with best practices in quality management.
Furthermore, regulatory shifts across various industries dictate the need for agile quality systems that can quickly adapt to new regulations. Healthcare, pharmaceuticals, and food industries, in particular, face stringent quality controls and frequent regulatory updates, pressing the need for adaptable and responsive management systems.
Lean and Six Sigma: Continuous Improvement Culture
The integration of Lean management and Six Sigma methodologies continues to play an essential role in QSM. These philosophies focus on reducing waste and enhancing process efficiency while striving for near-perfect quality. By fostering a culture of continuous improvement, organizations can not only streamline their operations but also improve customer satisfaction and employee engagement.
The Rise of Quality 4.0
The concept of Industry 4.0 has extended into the realm of quality, giving rise to 'Quality 4.0'. It refers to the transformation of quality management through digitalization. This includes the use of advanced technologies like augmented reality (AR) for training and process verification, and blockchain for secure and transparent documentation. Quality 4.0 initiatives lead to more intelligent quality control processes that are predictive, adaptive, and fully integrated into the digital supply chain.
Sustainability and Corporate Social Responsibility
Sustainability has become a significant aspect of modern QSM, as customers and stakeholders increasingly demand environmentally and socially responsible operations. Quality systems that incorporate sustainability metrics not only demonstrate corporate social responsibility but also help in identifying areas where resource efficiency can be improved. In the long term, sustainable practices contribute to the reliability and resilience of quality systems.
Skills Development and Quality Management Education
As the field of quality evolves, so does the need for skilled quality professionals. Continued education and skills development are crucial. Quality management certifications, workshops, and online courses allow professionals to stay informed about the latest strategies and tools. Additionally, soft skills like communication, problem-solving, and leadership are equally important for effectively implementing quality improvements.
The Customer-Centric Approach
Customer satisfaction is now more than ever the ultimate goal of quality management. Quality systems are being designed with a customer-centric approach, ensuring that customer feedback is integral to the quality improvement loop. By understanding customer needs and expectations, organizations can tailor their products and services to deliver a superior customer experience.
Conclusion
In summary, to stay relevant and effective in Quality Systems Management, professionals must be proactive in exploring and adopting the latest trends and innovations. From technological integration to embracing international standards, the dedication to continuous improvement and customer satisfaction, the future of quality management is both exciting and demanding. By staying informed and flexible, quality professionals can ensure that their organizations continue to deliver excellence while meeting the challenges of a dynamic global market.
Frequently Asked Questions
Frequently Asked Questions
What are the key trends shaping Quality Systems Management (QSM) today?
Quality Systems Management is influenced by various trends, including the harnessing of technology for automation and real-time monitoring, adherence to ISO standards, the integration of Lean and Six Sigma methodologies, the rise of Quality 4.0 through digitalization, a focus on sustainability and corporate social responsibility, skills development and education, and a customer-centric approach.
How can technology enhance quality systems in organizations?
Technology plays a significant role in improving quality systems by providing automation, predictive analytics, real-time monitoring, and data analysis capabilities. Software solutions, AI, machine learning, IoT devices, and Big Data analytics are some of the technologies utilized to streamline quality management processes.
Why is adherence to ISO standards crucial for quality systems?
Adherence to ISO standards, such as ISO 9001, is essential for establishing robust quality systems that meet international benchmarks. Compliance with ISO standards not only ensures quality consistency but also demonstrates a commitment to best practices in quality management.
What is the significance of Lean and Six Sigma in Quality Systems Management?
Lean and Six Sigma methodologies focus on continuous improvement, waste reduction, and process efficiency to achieve high-quality outputs. By embracing Lean and Six Sigma principles, organizations can enhance operational effectiveness, customer satisfaction, and employee engagement.
How does Quality 4.0 reshape quality management practices?
Quality 4.0 leverages digitalization and advanced technologies like AR and blockchain to transform quality control processes. Initiatives under Quality 4.0 aim to make quality management more predictive, adaptive, and integrated with digital supply chains for enhanced efficiency and transparency.
Why is sustainability important in modern Quality Systems Management?
Sustainability is integral to modern quality systems as it reflects a commitment to environmental and social responsibility. Incorporating sustainability metrics not only aligns with corporate social responsibility goals but also enhances resource efficiency and system resilience in the long run.
What skills are essential for professionals in Quality Systems Management?
Professionals in Quality Systems Management need a combination of technical and soft skills. Technical skills include knowledge of quality management tools and methodologies, while soft skills like communication, problem-solving, and leadership are crucial for effective implementation of quality improvements.
How does a customer-centric approach benefit quality management?
A customer-centric approach ensures that quality systems are designed to meet customer needs and expectations. By incorporating customer feedback into the improvement loop, organizations can enhance product and service offerings to deliver a superior customer experience.
Resources
Further Resources
For readers interested in delving deeper into Quality Systems Management trends and innovations, the following resources provide valuable insights and knowledge:
- American Society for Quality (ASQ) ASQ is a leading authority in quality management, offering resources, certifications, and training programs for quality professionals.
- International Organization for Standardization (ISO) The official website of ISO provides access to international standards and updates related to quality management.
- Lean Six Sigma Institute Learn more about Lean and Six Sigma methodologies, certification programs, and case studies on process improvement.
- Quality Digest Quality Digest is an online hub for quality news, articles, and insights from industry experts.
- Harvard Business Review - Quality Management Explore quality management articles and research from renowned business publication, Harvard Business Review.
- Deloitte Insights - Industry 4.0 Delve into the concept of Industry 4.0 and its impact on quality management with insights from Deloitte.
- Coursera - Quality Management Courses Access online courses on quality management topics, offered by universities and institutions on Coursera.
- Forbes - Sustainability and Corporate Social Responsibility Stay updated on sustainability trends and practices in quality systems with articles from Forbes.
- CustomerThink CustomerThink provides insights and resources on customer-centric approaches to quality management and improving customer satisfaction.
- LinkedIn Learning - Soft Skills Development Enhance your soft skills related to communication, problem-solving, and leadership through online courses on LinkedIn Learning.