Overcoming Common Challenges as a Warehouse Supervisor
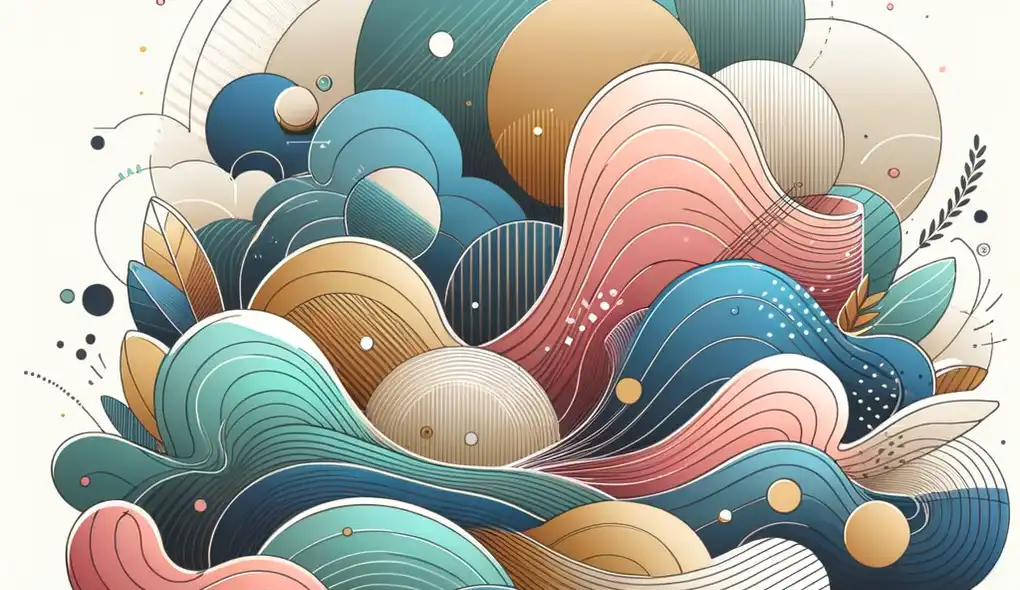
In the dynamic world of warehousing and logistics, a Warehouse Supervisor's role is crucial to ensure the smooth operation of supply chains across various industries. Supervisors are tasked with managing staff, coordinating logistics, overseeing safety, and maintaining inventory accuracy. However, this role comes with its unique set of challenges that can test the skills and resilience of even the most seasoned professionals. This article aims to explore some of these common hurdles and offer strategies to overcome them effectively.
Balancing Efficiency with Safety
One of the primary challenges for Warehouse Supervisors is maintaining a balance between efficient operations and ensuring workplace safety. Due to the physical nature of warehouse work, there is always a risk of injury, and speeding up operations can increase these risks. To tackle this, supervisors must prioritize safety protocols by providing comprehensive training and enforcing the use of personal protective equipment (PPE). They should also stay updated with Occupational Safety and Health Administration (OSHA) regulations and incorporate safety considerations into all operational plans.
Regular safety meetings and drills can help reinforce safe practices, while an open-door policy can encourage workers to report potential hazards without fear of reprisal. By integrating safety as a core value rather than a checkbox activity, supervisors can help build a culture of safety that complements operational efficiency.
Managing a Diverse Workforce
Warehouse teams often consist of individuals from varied backgrounds with different levels of experience and expertise. A Warehouse Supervisor must navigate these differences to foster an inclusive and productive work environment. Key to this is effective communication. Supervisors should take time to understand the unique strengths and needs of their team members, adapting their management style as necessary.
Investing in regular training and professional development can also help bridge the skill gaps and empower employees to take on new challenges. By recognizing and valuing diversity, supervisors can tap into a wider range of perspectives and skills, which can be advantageous when solving complex problems.
Handling Inventory Management and Accuracy
Inventory management is the backbone of warehousing, and mistakes can lead to significant financial losses. Supervisors must constantly seek ways to improve inventory accuracy, which includes implementing inventory control systems, conducting regular stock takes, and investigating and resolving discrepancies swiftly.
Technology can be a powerful ally in this regard. The adoption of Warehouse Management Systems (WMS) can streamline inventory tracking and reduce errors. Educating the team on the benefits of such systems and ensuring proper use can maximize the potential for improved accuracy and productivity.
Dealing with Technological Changes
The rapid pace of technological change presents another challenge for supervisors, who must keep up with the latest trends and tools. This could range from the introduction of automation to the use of advanced data analytics for better decision-making. To stay ahead, supervisors should actively seek training and stay curious about new technologies that could benefit their operations.
Partnerships with tech providers for training and support can ease the transition for the team, and an incremental approach to adopting new technologies can minimize disruption to daily operations.
Coping with Seasonal Fluctuations
Demand can vary widely in a warehouse setting, with peak seasons requiring significantly more labor and resources. Supervisors must plan for these fluctuations in advance, perhaps through hiring temporary workers or adjusting shifts to match demand. This also requires clear communication with both the existing staff, to prepare them for increased workloads, and the supply chain partners to ensure that inventory levels are adequate.
Developing Leadership and Problem-Solving Skills
Effective Warehouse Supervisors are not just managers; they are leaders who inspire their team and solve problems creatively. Developing these skills takes time and experience. Supervisors should welcome opportunities to lead cross-functional projects, seeking feedback to refine their leadership style. Regular training in problem-solving methodologies can also provide supervisors with tools to tackle issues systematically and with confidence.
Conclusion
In conclusion, Warehouse Supervisors face a diverse array of challenges, from safety and diversity management to technological change and seasonal demands. By maintaining a commitment to safety, embracing technology, and investing in their team's development, supervisors can not only overcome these obstacles but also drive their operations to new heights of success. The role is demanding but offers the opportunity for growth and achievement in the fast-paced world of logistics.
Frequently Asked Questions
Frequently Asked Questions
1. How can Warehouse Supervisors prioritize both efficiency and safety?
Warehouse Supervisors can prioritize both efficiency and safety by implementing comprehensive safety protocols, providing regular training, enforcing the use of personal protective equipment, and incorporating safety considerations into all operational plans. By creating a culture of safety and conducting regular safety meetings, supervisors can maintain a balance between efficient operations and workplace safety.
2. How can Warehouse Supervisors effectively manage a diverse workforce?
Warehouse Supervisors can effectively manage a diverse workforce by practicing effective communication, understanding the unique strengths and needs of team members, and adapting management styles accordingly. Investing in regular training and professional development can help bridge skill gaps and empower employees from different backgrounds to contribute effectively to the team.
3. What strategies can Warehouse Supervisors use to improve inventory management and accuracy?
To improve inventory management and accuracy, Warehouse Supervisors can implement inventory control systems, conduct regular stock takes, and swiftly investigate and resolve discrepancies. Utilizing Warehouse Management Systems (WMS) and educating the team on their benefits can streamline inventory tracking and reduce errors, leading to improved accuracy and productivity.
4. How can Warehouse Supervisors cope with technological changes in the warehouse setting?
Warehouse Supervisors can cope with technological changes by staying informed about the latest trends and tools, actively seeking training, and partnering with tech providers for support. An incremental approach to adopting new technologies can minimize disruptions to daily operations while maximizing the benefits of automation and data analytics.
5. How should Warehouse Supervisors prepare for seasonal fluctuations in demand?
Warehouse Supervisors should plan for seasonal fluctuations by hiring temporary workers, adjusting shifts to match demand, and maintaining clear communication with existing staff and supply chain partners. By preparing in advance and ensuring adequate inventory levels, supervisors can effectively manage peak seasons and optimize resources.
6. What steps can Warehouse Supervisors take to develop leadership and problem-solving skills?
To develop leadership and problem-solving skills, Warehouse Supervisors should actively seek opportunities to lead cross-functional projects, welcome feedback to refine their leadership style, and undergo regular training in problem-solving methodologies. By honing these skills, supervisors can inspire their teams, solve issues systematically, and drive operations to success.
Resources
Further Resources
For further deep diving into the world of warehouse supervision and tackling the challenges that come with it, here are some valuable external resources that can provide additional insights and guidance:
- Occupational Safety and Health Administration (OSHA) Warehouse Safety Guidelines: A comprehensive resource by OSHA outlining safety guidelines specifically tailored to warehouse environments.
- Warehouse Education and Research Council (WERC): WERC offers a wealth of resources, including webinars, whitepapers, and educational events focused on warehouse management and best practices.
- Institute of Supply Chain Management (IoSCM): IoSCM provides professional development and certification programs for those looking to enhance their skills in supply chain management, including warehouse supervision.
- Material Handling Industry of America (MHI): MHI is a resource hub for material handling and logistics professionals, offering research reports, industry insights, and networking opportunities.
- Supply Chain Dive: A digital publication covering the latest trends and news in the supply chain industry, including warehouse management and logistics.
- Warehouse Inventory Management: A Complete Guide: An in-depth guide covering strategies and best practices for effective warehouse inventory management.
These resources cover a wide range of topics, from safety regulations to inventory management techniques, and can serve as valuable references for Warehouse Supervisors looking to enhance their skills and overcome common challenges in the warehouse environment.