GMP Auditor
A GMP Auditor is responsible for examining and ensuring compliance with Good Manufacturing Practices within production facilities, often related to pharmaceuticals, food, or medical devices.
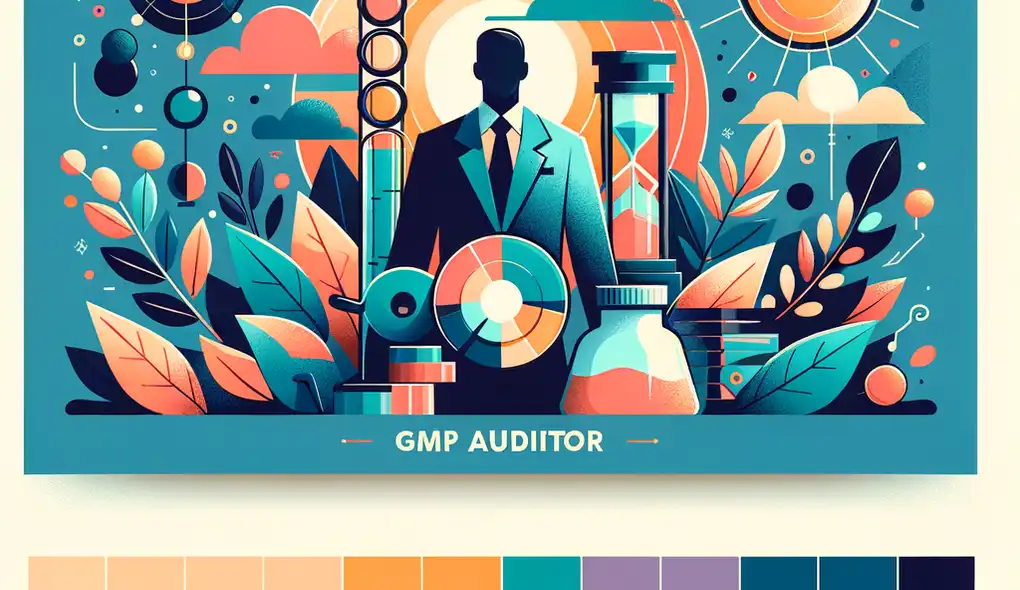
Top Articles for GMP Auditor
Sample Job Descriptions for GMP Auditor
Below are the some sample job descriptions for the different experience levels, where you can find the summary of the role, required skills, qualifications, and responsibilities.
Junior (0-2 years of experience)
Summary of the Role
A Junior GMP Auditor is responsible for conducting internal and supplier audits to ensure compliance with Good Manufacturing Practices (GMP) and other quality standards in the manufacturing and packaging of products within the pharmaceutical, food, or cosmetics industries.
Required Skills
- Attention to detail
- Critical thinking
- Time management
- Data analysis
- Report writing
Qualifications
- Bachelor's degree in science, engineering, or a related field.
- Understanding of GMP guidelines and relevant quality standards.
- Strong analytical and problem-solving skills.
- Excellent written and verbal communication skills.
- Ability to work independently and as part of a team.
Responsibilities
- Assist in planning and conducting regular GMP audits of internal processes and supplier facilities.
- Ensure compliance with company policies, industry standards, and regulatory requirements.
- Prepare audit reports, document findings, and follow up on corrective actions.
- Contribute to the continuous improvement of quality systems and GMP practices.
- Participate in the training of company personnel on GMP requirements and quality issues.
- Work with cross-functional teams to resolve compliance issues.
- Assist with the preparation for external regulatory audits.
Intermediate (2-5 years of experience)
Summary of the Role
The GMP Auditor is responsible for ensuring that manufacturing processes comply with the Good Manufacturing Practice (GMP) guidelines. The role involves regular inspections, auditing production processes, documenting findings, and making recommendations for improvements to ensure quality and compliance with industry regulations.
Required Skills
- Excellent analytical and problem-solving skills.
- Strong attention to detail and the ability to identify non-compliance issues.
- Professional communication and report-writing skills.
- Ability to work independently as well as part of a team.
- Proficiency in using quality management software and systems.
- Solid understanding of production processes and product lifecycle.
- Demonstrated ability to train and guide staff on GMP-related matters.
- Effective time management skills with the ability to handle multiple audits simultaneously.
Qualifications
- Bachelor's degree in a relevant field such as Biology, Chemistry, Pharmacy, or a related scientific discipline.
- 2-5 years of experience in quality assurance or a related GMP-regulated environment.
- Strong knowledge of GMP guidelines and regulatory requirements for pharmaceuticals, biotechnology, or food and beverages.
- Certification in GMP auditing or a related quality assurance certification is preferred.
- Experience in conducting audits and inspections, with a track record of identifying and resolving compliance issues.
Responsibilities
- Conducting thorough audits of manufacturing facilities to ensure compliance with GMP standards.
- Preparing detailed reports of audit findings and presenting them to senior management.
- Identifying non-compliance issues and potential risks within the production process.
- Recommending corrective actions and improvements to manufacturing protocols.
- Training and guiding staff on GMP requirements and best practices.
- Staying updated with changes in GMP regulations and industry standards.
- Collaborating with quality assurance and production teams to enhance quality control measures.
- Participating in the development and revision of standard operating procedures (SOPs).
- Leading and participating in continuous improvement initiatives within the organization.
Senior (5+ years of experience)
Summary of the Role
A senior GMP Auditor is responsible for ensuring that manufacturing processes meet the established Good Manufacturing Practices (GMP) standards. This role involves conducting audits, providing guidance on quality assurance, and ensuring compliance with regulatory requirements.
Required Skills
- Auditing and compliance enforcement
- Analytical thinking
- Attention to detail
- Report writing and documentation
- Regulatory knowledge
- Quality assurance methodologies
- Leadership and team management
- Communication and training
- Risk assessment and management
- Project management
Qualifications
- Bachelor's degree in a related science or engineering field.
- Minimum of 5 years' experience in GMP auditing within the pharmaceutical or related regulated industry.
- Proven track record of successful audit management and compliance enforcement.
- In-depth knowledge of GMP guidelines and relevant regulatory requirements.
- Certification in GMP auditing is highly desirable.
- Strong analytical and problem-solving skills.
- Effective communication and interpersonal skills.
- Ability to lead and motivate a team.
- Willingness to travel extensively to perform audits at various sites.
Responsibilities
- Conduct thorough GMP audits of manufacturing facilities to ensure compliance with all regulations and standards.
- Prepare detailed audit reports and present findings to senior management.
- Collaborate with quality assurance teams to develop corrective action plans for identified issues.
- Train and mentor junior auditors and quality assurance staff.
- Stay up-to-date with changes in GMP regulations and inform relevant departments.
- Participate in the development and revision of company SOPs reflecting current GMP.
- Ensure proper documentation of all audits and follow-up actions are maintained.
- Lead cross-functional teams to implement GMP best practices throughout the organization.
- Facilitate external regulatory inspections and act as the point of contact for regulatory agencies.
- Assist in reducing compliance risks and enhancing the overall quality of products.
See other roles in Science and Technology and Pharmaceutical