Mastering Compliance: A Guide for Laboratory Quality Managers
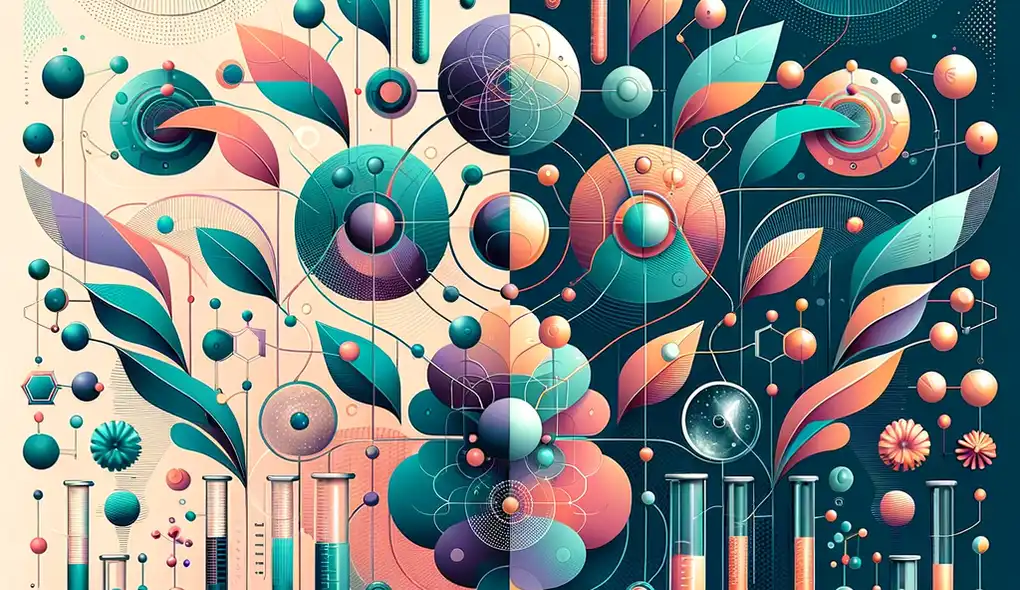
Laboratory compliance is an essential aspect of ensuring the integrity, safety, and quality of research and testing environments. For quality managers, mastering the numerous regulations that govern laboratories is crucial to maintaining high standards and fostering trust in their organization's work. This guide provides an in-depth look at the complexities of laboratory compliance and offers practical advice for quality managers seeking to excel in their role.
Understanding Laboratory Compliance
Compliance in the laboratory context refers to adhering to the set of standards, guidelines, and regulations that are required by governing bodies, industry standards, or internal quality policies. These can range from international standards like ISO/IEC 17025, which governs testing and calibration labs, to country-specific regulations like CLIA (Clinical Laboratory Improvement Amendments) in the United States, which focus on human health. The goal is to guarantee the credibility and reliability of laboratory results.
For quality managers, understanding the specifics of these regulations is the first step towards ensuring that the laboratory operates within legal and ethical boundaries. Compliance isn't just about following rules; it's a commitment to excellence and continual improvement that requires a deep understanding of the 'why' behind each protocol.
Key Components of Laboratory Compliance
Several key elements must be considered when assessing a laboratory's compliance status:
Regulatory Requirements
The type and scope of regulations depend on the laboratory's focus, such as medical, environmental, or forensic testing. Familiarize yourself with the applicable laws and agencies governing your laboratory, such as the FDA, EPA, or OSHA in the United States.
Quality Systems
A robust Quality Management System (QMS) is indispensable for compliance. It provides a formalized way of managing procedures, protocols, and documentation. Well-established QMS frameworks include ISO 9001 and the Good Laboratory Practices (GLP).
Documentation and Record Keeping
Accurate and comprehensive documentation is perhaps the most visible component of compliance. It provides evidence of adherence to processes and allows for traceability in case of audits or investigations.
Equipment and Calibration
Regular calibration and maintenance of laboratory equipment are vital to ensure accuracy and repeatability of test results. This lies at the heart of compliance, as unreliable equipment can lead to false results and non-compliance.
Personnel Training
Well-trained staff are the backbone of any compliant laboratory. Training programs should cover both the practical skills needed to perform laboratory tests and the regulatory knowledge to understand compliance requirements.
Audits and Assessments
Internal and external audits are critical for maintaining compliance. They provide an opportunity to identify areas for improvement and to fix any issues before they become significant problems.
Strategies for Mastering Compliance
To maintain and improve lab compliance, a quality manager should employ several strategies:
Stay Updated on Regulations
Regulations are frequently updated, and new ones are introduced. Regularly reviewing regulatory changes and assessing their impact on your laboratory's operations is essential.
Develop a Compliance Culture
Compliance should be a shared responsibility. Creating a culture where every team member understands the importance of compliance and is committed to maintaining it is key to long-term success.
Implement Continuous Training
Continuous education and training ensure that all personnel are aware of compliance requirements and competent in their roles.
Use Technology to Your Advantage
Leveraging laboratory information systems (LIS) and other software to automate and manage QMS tasks can significantly reduce errors and increase efficiency.
Prepare for Audits
Regular mock audits and self-assessments help prepare for real ones. They ensure that the laboratory is always ready for an inspector's visit, thereby reducing stress and potential issues.
Foster Open Communication
Encouraging open dialogue about compliance issues allows problems to be identified and addressed swiftly. This can also promote a collaborative environment where best practices are shared.
Counteracting Common Compliance Challenges
Quality managers often face challenges, including:
Resource Limitations
Limited budgets or staffing can constrain compliance efforts. Creative solutions like cross-training employees or reallocating funds are sometimes necessary to overcome these obstacles.
Resistance to Change
Some personnel may be resistant to new procedures or standards. It's crucial to communicate the benefits of compliance and involve the team in the process to minimize resistance.
Keeping Up with Technological Advances
As laboratory technologies evolve, so do compliance requirements. Staying abreast of new technologies and how they impact compliance is important.
Navigating International Standards
For labs that operate globally, navigating the complexities of international compliance can be daunting. Understanding the global landscape and ensuring consistency across locations is vital.
Conclusion
Compliance is not a destination but a continuous journey of improvement. For laboratory quality managers, this guide provides a roadmap for mastering compliance in order to sustain a reputable, ethical, and high-performing laboratory. By understanding the entirety of what compliance entails, developing robust strategies to meet challenges head-on, and fostering an environment where quality and compliance are cornerstones of the laboratory culture, quality managers can safeguard standards and contribute to the overall success of their organizations.
Frequently Asked Questions
Frequently Asked Questions
1. Why is laboratory compliance important?
Laboratory compliance is crucial as it ensures the credibility and reliability of testing results. It also helps in maintaining high standards, adhering to legal requirements, and fostering trust in the organization's work.
2. What are some common regulatory bodies governing laboratory compliance?
Regulatory bodies governing laboratory compliance vary depending on the industry focus. Examples include the FDA, EPA, OSHA in the United States, and international standards like ISO/IEC 17025.
3. How can quality managers ensure staff compliance with regulations?
Quality managers can ensure staff compliance by providing thorough training programs that cover both technical skills and regulatory knowledge. Implementing regular assessments and fostering a culture of compliance within the team are also effective strategies.
4. What are the consequences of non-compliance in a laboratory setting?
Non-compliance in a laboratory setting can lead to inaccurate results, compromised safety, legal issues, loss of credibility, and potential harm to individuals or the environment.
5. How can technology aid in laboratory compliance?
Technology, such as laboratory information systems (LIS), can help in automating tasks, managing documentation, ensuring data integrity, and facilitating regulatory compliance through enhanced efficiency and accuracy.
6. How often should audits be conducted to maintain compliance?
Internal and external audits should be conducted regularly to maintain compliance. The frequency may vary based on the type of laboratory, regulations, and internal policies, but typically, annual audits are recommended.
7. What role does communication play in maintaining compliance?
Open communication is essential in maintaining compliance as it allows for the identification of issues, prompt resolution of problems, and the sharing of best practices within the team.
Resources
Further Resources
For further exploration and enhancement of your knowledge on laboratory compliance and quality management, here are some valuable resources:
- International Laboratory Accreditation Cooperation (ILAC) - ILAC ILAC provides information on laboratory accreditation and the mutual recognition of test results to facilitate international trade.
- Clinical and Laboratory Standards Institute (CLSI) - CLSI CLSI offers standards and guidelines for medical laboratory testing to improve patient care around the world.
- U.S. Food and Drug Administration (FDA) - Laboratory Compliance - FDA The FDA website provides resources on laboratory compliance for facilities regulated by the FDA.
- American Society for Quality (ASQ) - Quality Management - ASQ ASQ offers resources and training on quality management, including certifications like Certified Manager of Quality/Organizational Excellence (CMQ/OE).
- National Environmental Laboratory Accreditation Program (NELAP) - NELAP NELAP sets standards for environmental laboratory accreditation to ensure accurate and reliable testing.
- Occupational Safety and Health Administration (OSHA) - Laboratory Safety - OSHA OSHA provides guidelines and resources for laboratory safety to protect workers from occupational hazards.
- American Association for Laboratory Accreditation (A2LA) - A2LA A2LA offers accreditation services and training programs for testing laboratories across various industries.
- European Committee for Standardization (CEN) - Laboratory Quality Standards - CEN CEN develops standards for laboratory quality management, ensuring consistency in testing practices across Europe.
These resources cover a broad spectrum of topics related to laboratory compliance, quality management, accreditation, and safety. Delve into these sources to deepen your understanding and stay updated on the latest developments in the field.