Common Challenges in Quality Control and Strategic Solutions
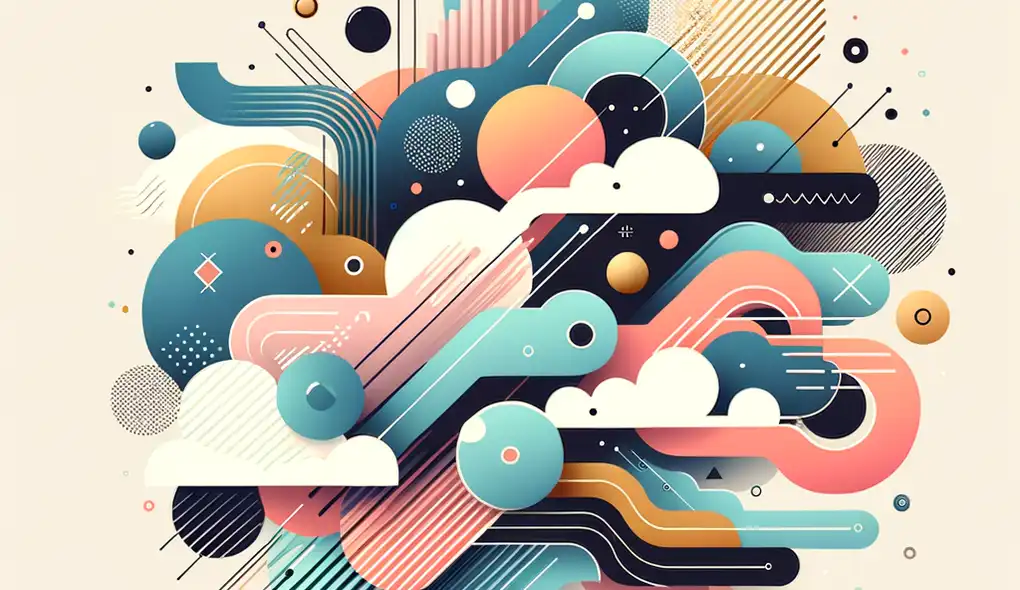
In the ever-evolving landscape of production and services, Quality Control (QC) remains a cornerstone for maintaining excellence. Known for its stringent processes and attention to detail, QC ensures that products and services meet or exceed customer expectations. However, QC professionals face numerous challenges that can affect efficiency, reliability, and effectiveness. This article explores common challenges encountered in the realm of Quality Control and provides strategic solutions to overcome them.
The Evolution of Quality Standards
Quality standards have significantly evolved over time, becoming more comprehensive to fit the varying needs of different industries. International frameworks such as ISO have created benchmarks that guide organizations in maintaining a high standard of quality. However, with greater standards comes greater complexity, creating challenges for QC professionals who must navigate these rigorous requirements while ensuring that their organizations keep pace with the competitive market.
Challenge: Keeping up with ever-changing quality standards.
Solution: Implement a continuous learning culture within the organization. Regular training programs and updates on the latest standards must be a priority. Furthermore, engaging a specialized compliance officer or team can keep all processes up-to-date with current regulations.
The Integration of New Technologies
The integration of new technologies into QC processes introduces both opportunities and challenges. Advanced equipment and software can dramatically improve the efficiency and accuracy of quality assessments but require significant investment and adaptation.
Challenge: Adapting to new technology and integrating it into existing systems.
Solution: Develop a strategic technology adoption plan that includes pilot testing, comprehensive training, and gradual implementation. Quality teams should collaborate with IT departments to ensure seamless integration without disrupting ongoing operations.
Managing Supplier Quality
A common issue in QC is managing the quality of components or materials received from suppliers. The diversity and global nature of supply chains can make it difficult to maintain consistent quality standards.
Challenge: Ensuring supplier compliance with quality standards.
Solution: Forge strong relationships with suppliers through regular communication and mutual agreements on quality expectations. Conduct audits and provide feedback to promote continuous improvement. Implementing supplier development programs can also enhance supplier performance.
Data Management and Analysis
The vast quantities of data generated during QC processes can be overwhelming. Extracting meaningful insights from this data is critical for informed decision-making.
Challenge: Handling large sets of complex quality data.
Solution: Invest in robust data management systems that facilitate data collection, storage, and analysis. Employing specialized data analysts or utilizing advanced data analytics tools can help QC professionals turn data into actionable intelligence.
Handling Quality Issues and Recalls
When defects or non-compliance issues arise, the response of the QC department is pivotal. Inadequate handling can lead to recalls, brand damage, and financial loss.
Challenge: Managing and mitigating quality issues effectively.
Solution: Develop a comprehensive crisis management plan that includes quick identification, communication protocols, and corrective action strategies. Regular scenario planning and response drills will help the QC team act decisively when real issues arise.
Workforce Skills and Expertise
With the diversification of products and services, QC demands a workforce with specialized skills and expertise.
Challenge: Acquiring and retaining skilled QC personnel.
Solution: Invest in employee development with a focus on upskilling and reskilling. Create a compelling career path in QC by offering certifications, promotions, and incentives for continual improvement.
Sustainability and Environmental Compliance
Increasingly, QC practices are being scrutinized for their environmental impact.
Challenge: Aligning QC processes with sustainability guidelines.
Solution: Adopt eco-friendly production methods and materials. Implement an environmental management system that is incorporated into the QC process.
Cost Control
Balancing quality with cost effectiveness remains a fundamental challenge for QC teams.
Challenge: Controlling QC costs without compromising quality.
Solution: Use lean methodologies to eliminate waste and streamline processes. Engage in cost-benefit analysis when evaluating quality initiatives.
Conclusion
Quality Control is an integral part of any successful business strategy. Overcoming the challenges faced by QC professionals requires a strategic approach that blends adaptability, innovation, and collaboration. By employing the solutions outlined above, organizations can ensure that their QC processes are not only effective but also resilient to the dynamic demands of the global marketplace.
Frequently Asked Questions
Frequently Asked Questions
What are the common challenges faced by Quality Control professionals?
Quality Control professionals often encounter challenges such as keeping up with evolving quality standards, integrating new technologies, managing supplier quality, handling large sets of complex data, managing quality issues effectively, acquiring skilled workforce, aligning with sustainability guidelines, and controlling costs.
How can organizations keep up with ever-changing quality standards?
Organizations can implement a continuous learning culture by providing regular training programs and updates on the latest standards. Engaging specialized compliance officers or teams can also help in maintaining compliance with current regulations.
What is the importance of integrating new technologies into Quality Control processes?
Integrating new technologies can enhance the efficiency and accuracy of quality assessments. However, it requires a strategic adoption plan that includes pilot testing, comprehensive training, and collaboration with IT departments for seamless integration.
How can Quality Control professionals manage supplier quality effectively?
Managing supplier quality involves building strong relationships through regular communication, audits, and feedback mechanisms. Implementing supplier development programs can also improve supplier performance and maintain consistent quality standards.
Why is data management and analysis crucial in Quality Control?
Data management and analysis are vital for extracting meaningful insights from the vast quantities of data generated during QC processes. Investing in robust data management systems and employing specialized data analysts can help QC professionals make informed decisions based on actionable intelligence.
How can organizations handle quality issues and recalls efficiently?
Efficient handling of quality issues and recalls requires a comprehensive crisis management plan that includes quick identification, communication protocols, and corrective action strategies. Regular scenario planning and response drills can help the QC team act decisively during real issues.
What strategies can be employed to acquire and retain skilled QC personnel?
Organizations can invest in employee development by offering upskilling and reskilling opportunities. Creating a compelling career path in QC with certifications, promotions, and incentives for continual improvement can help in acquiring and retaining skilled QC personnel.
How can organizations align Quality Control processes with sustainability guidelines?
Aligning QC processes with sustainability guidelines involves adopting eco-friendly production methods and materials. Implementing an environmental management system that is integrated into the QC process can ensure compliance with sustainability practices.
What approaches can be used to balance quality with cost effectiveness in QC?
To balance quality with cost effectiveness, QC teams can utilize lean methodologies to eliminate waste and streamline processes. Engaging in cost-benefit analysis when evaluating quality initiatives can help in controlling QC costs without compromising quality.
Resources
Further Resources
For readers interested in delving deeper into the realm of Quality Control and seeking additional insights, resources, and tools to enhance their knowledge and skills, the following resources are highly recommended:
- American Society for Quality (ASQ)
ASQ is a global community of quality professionals dedicated to promoting excellence in quality practices, offering certifications, training programs, webinars, and publications that cover various aspects of Quality Control.
ASQ Website - International Organization for Standardization (ISO)
The ISO is a leading international standard-setting body that provides guidelines and frameworks for quality management systems used worldwide. Visit their website to access the latest quality standards and publications.
ISO Website - Quality Digest
Quality Digest is an online publication that features articles, news, and insights on quality management, best practices, tools, and techniques. Readers can benefit from a range of resources to stay updated on industry trends.
Quality Digest Website - MIT OpenCourseWare - Quality Control Courses
Massachusetts Institute of Technology (MIT) offers free online courses on quality control, covering topics such as statistical quality control, process improvement, and quality management systems. These courses are ideal for professionals seeking to deepen their understanding of QC principles.
MIT OpenCourseWare - Quality Control Courses - Lean Six Sigma Institute
Lean Six Sigma Institute provides training and certification programs in Lean Six Sigma methodology, a powerful approach to process improvement and quality management. Explore their resources to enhance your skills in QC and efficiency optimization.
Lean Six Sigma Institute Website - National Institute of Standards and Technology (NIST)
NIST offers resources on measurement science, standards, and technology that are essential for quality assurance and compliance. Access their publications and tools to strengthen your QC practices.
NIST Website