Staying Ahead of the Curve: Top Trends in Corrosion Engineering
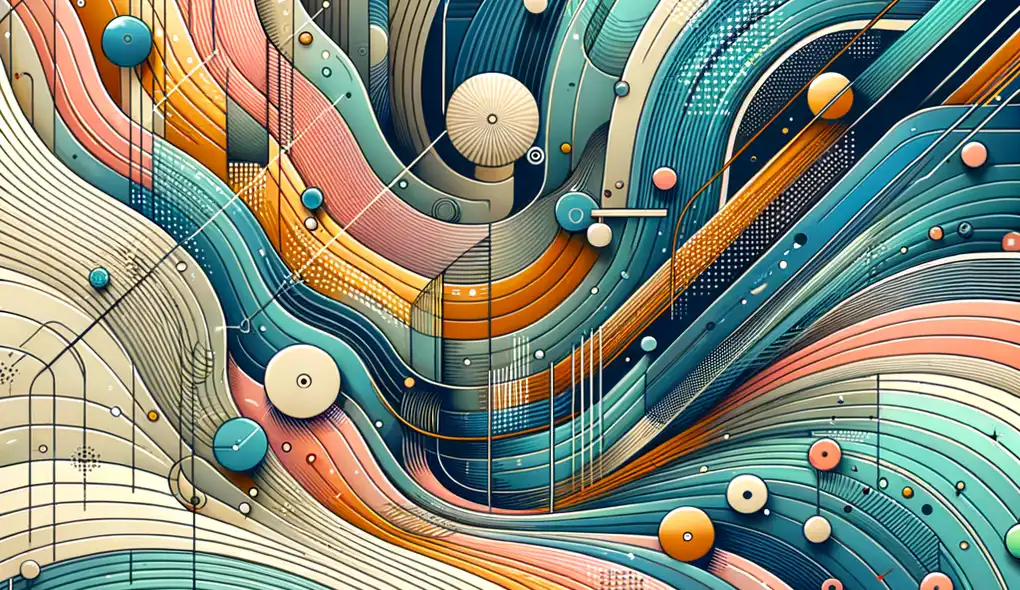
Corrosion engineering, a critical field that impacts a wide range of industries from infrastructure and transportation to energy and manufacturing, is constantly evolving with advancements in technology and materials science. Staying ahead of the curve in this domain is not just beneficial; it's imperative for the safety, efficiency, and longevity of facilities and structures. In this article, we'll explore the leading trends and innovations shaping the future of corrosion engineering.
Advancements in Protective Coatings
Protective coatings have always been a staple in combating corrosion. However, the new generation of coatings goes beyond traditional epoxy or polyurethane systems. One of the significant trends is the development of smart coatings that can respond to environmental changes and heal themselves when damaged. These coatings contain microcapsules filled with a healing agent that is released upon the formation of cracks or scratches, thereby autonomously repairing the damage and preventing corrosion.
Another innovative approach is the use of nanocoatings which comprise nanoparticles that can provide superior adhesion, durability, and corrosion resistance compared to conventional coatings. Companies are also developing bio-based coatings derived from renewable sources which are not only environmentally friendly but also offer excellent anti-corrosive properties.
Corrosion Monitoring and Predictive Maintenance
Modern corrosion engineering is increasingly moving towards real-time monitoring and predictive maintenance. The integration of sensors and IoT (Internet of Things) technology allows for continuous monitoring of structures for signs of corrosion. Data gathered from these sensors can be analyzed using machine learning algorithms to predict when and where corrosion is likely to occur, enabling preemptive maintenance and replacement activities.
This trend is particularly important in hard-to-access or critical areas where failure due to corrosion could have severe consequences. For instance, oil and gas pipelines, which are often located in remote areas, are now being fitted with smart pigging devices equipped with sensors that can detect corrosion and other forms of damage as they travel through the pipeline.
Advanced Materials
The quest for new materials that exhibit superior resistance to corrosion continues. Alloys with high entropy are emerging as a novel material class. These alloys consist of multiple principal elements rather than one, resulting in a complex microstructure that offers enhanced corrosion resistance. Corrosion-resistant superalloys, which are already used extensively in the aerospace industry, are finding new applications in other fields where extreme environments are commonplace.
Moreover, composite materials which use a combination of fibers and a matrix are being increasingly used for their excellent strength-to-weight ratios and resistance to corrosion. Carbon fiber reinforced polymers (CFRPs) and glass fiber reinforced polymers (GFRPs) are examples where the use of composites is expanding, particularly in the marine and automotive industries.
Environmentally Sustainable Practices
With increasingly stringent environmental regulations and a growing emphasis on sustainability, corrosion engineers are seeking out more eco-friendly approaches to design and maintenance. An obvious trend is the phasing out of harmful corrosion inhibitors, such as chromates, in favor of green inhibitors that provide adequate protection without the associated environmental risks.
Recycling and repurposing materials is another key aspect of sustainable practices in corrosion engineering. Innovations such as the development of recyclable thermoset composites, which were previously difficult to recycle, can significantly reduce the environmental footprint of materials used in corrosion-prone applications.
Digitalization and Computational Modeling
Digital technologies have become fundamental in the advancement of corrosion engineering. Computational modeling tools, such as finite element analysis (FEA), are used for simulating corrosion processes and assessing the integrity of materials and structures. These simulations can help in understanding complex corrosion mechanisms and in the development of more durable materials and protective systems.
Digital twins, virtual replicas of physical assets, enable engineers to simulate and analyze the behavior of these assets under various conditions without the need to perform costly and time-consuming experiments. This means better predictive capabilities and optimizations in design and maintenance programs.
Conclusion
Corrosion engineering is undergoing a transformation. Innovations in coatings technology, materials science, digitalization, and sustainable practices are setting new benchmarks for the management of corrosion. The adoption of these trends not only prolongs the life of assets and structures but also enhances safety and reduces the environmental impact. As we move further into the 21st century, the importance of staying ahead of the curve in corrosion engineering cannot be overstated, for it is the linchpin in ensuring the durability and success of a wide range of industries.
Frequently Asked Questions
Frequently Asked Questions
1. What are the common types of protective coatings used in corrosion engineering?
In corrosion engineering, some common types of protective coatings include epoxy coatings, polyurethane coatings, smart coatings with self-healing properties, nanocoatings for superior adhesion, durability, and corrosion resistance, and bio-based coatings derived from renewable sources.
2. How does corrosion monitoring help in predictive maintenance?
Corrosion monitoring through sensors and IoT technology enables real-time data collection on structural integrity, allowing for the prediction of potential corrosion areas. Machine learning algorithms analyze this data to forecast corrosion occurrences, facilitating timely maintenance actions to prevent structural damage.
3. What are high entropy alloys and their significance in corrosion resistance?
High entropy alloys are materials composed of multiple principal elements, offering enhanced corrosion resistance due to their complex microstructure. These alloys are increasingly sought after for applications requiring superior resistance to corrosive environments.
4. What eco-friendly practices are being adopted in corrosion engineering?
Corrosion engineers are shifting towards environmentally sustainable practices by replacing harmful inhibitors like chromates with green inhibitors. Additionally, recycling and repurposing materials, such as developing recyclable thermoset composites, are becoming prevalent in reducing environmental impact.
5. How do digitalization and computational modeling benefit corrosion engineering?
Digital technologies, including computational modeling tools like finite element analysis (FEA) and digital twins, aid in simulating corrosion processes, assessing material integrity, and optimizing design and maintenance practices. These tools improve predictive capabilities and efficiency in managing corrosion-related issues.
Resources
Further Resources
For readers interested in delving deeper into the world of corrosion engineering and staying updated on the latest trends and technologies, the following resources provide valuable insights and information:
- NACE International: The world's leading organization dedicated to corrosion prevention and control, NACE International offers a wealth of technical resources, training programs, and industry standards. Visit NACE International for access to a vast repository of corrosion-related content.
- Corrosionpedia: An online hub for corrosion professionals, engineers, and enthusiasts, Corrosionpedia hosts articles, guides, webinars, and a comprehensive glossary covering various aspects of corrosion science and mitigation strategies. Explore more at Corrosionpedia.
- Materials Performance: A trusted source of corrosion news, case studies, and product information, Materials Performance magazine offers in-depth coverage of corrosion control technologies and best practices. Check out their latest articles at Materials Performance.
- ASM International: Known for its expertise in materials science and engineering, ASM International provides resources on materials selection, processing, and performance in corrosive environments. Visit ASM International for access to technical publications and educational materials.
- Society for Protective Coatings (SSPC): As a leading organization in the protective coatings industry, SSPC offers training courses, certification programs, and industry standards to enhance knowledge and skills in corrosion protection. Explore more at SSPC.
- American Society of Civil Engineers (ASCE): For professionals involved in infrastructure and structural engineering, ASCE provides technical journals, conferences, and resources relevant to corrosion management in civil engineering projects. Visit ASCE for additional information.
- International Maritime Organization (IMO): Individuals interested in corrosion challenges specific to the maritime industry can benefit from the IMO's publications and guidelines on marine corrosion prevention and control. Access resources at IMO.
- LinkedIn Groups: Joining corrosion engineering and materials science groups on LinkedIn can facilitate networking with industry experts, sharing insights, and participating in discussions on the latest trends. Search for relevant groups on LinkedIn for community engagement.
By leveraging these resources and platforms, professionals, researchers, and enthusiasts can stay informed, collaborate with peers, and expand their knowledge in corrosion engineering for a sustainable and resilient future.