Staying Ahead: Trends in Maintenance Technology and Practices
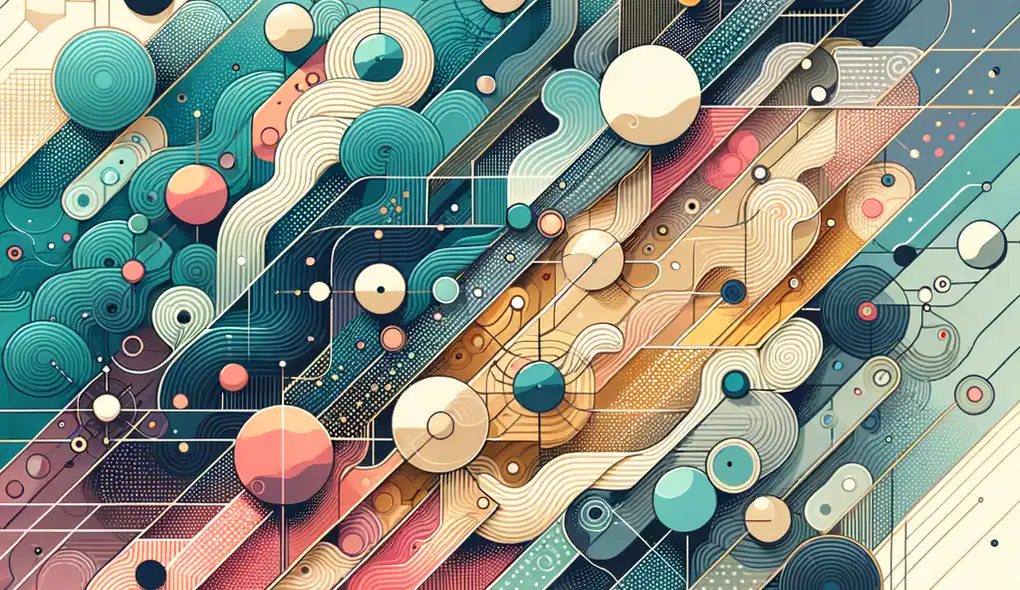
In the ever-evolving world of industry and technology, maintenance practices have come a long way from the simple 'fix it when it breaks' approach. Today, the maintenance industry is witnessing a profound transformation propelled by technological advancements and innovative practices designed to predict, prevent, and quickly address equipment failures and inefficiencies. This comprehensive article will explore some of the most significant trends and technologies impacting the maintenance sector today.
Predictive Maintenance
One of the most significant shifts in maintenance methodology is the move from reactive to predictive maintenance. Predictive maintenance involves using data analysis tools and techniques to detect anomalies, trends, and patterns that predict equipment failure. By using Internet of Things (IoT) sensors and advanced analytics, maintenance teams can monitor real-time conditions of machinery and act before a system breakdown occurs. This not only reduces downtime but also extends the lifespan of equipment.
For instance, vibration analysis, infrared thermography, ultrasonic leak detectors, and oil analysis are technologies now commonly used in predictive maintenance strategies. These tools provide early warning signs of wear and tear or impending problems, allowing businesses to schedule maintenance during planned downtime rather than in response to an unexpected breakdown.
Maintenance Software and AI
Maintenance management software, also known as Computerized Maintenance Management Systems (CMMS), has evolved significantly. Modern CMMS platforms integrate with IoT devices, allowing for seamless data flow and enabling more informed decision-making. Many of these systems are now powered by artificial intelligence (AI) and machine learning algorithms that can learn from historical data to optimize maintenance schedules and procedures.
AI can also help prioritize maintenance tasks based on potential impact on operations and predict spare parts inventory needs. Smart algorithms can even diagnose issues and suggest the most effective repair solutions, saving valuable time and resources.
Augmented Reality (AR) for Training and Repair
Augmented reality is revolutionizing how technicians are trained and assisted. AR applications in the maintenance industry allow workers to visualize the inner workings of a machine without disassembling it. This is particularly useful in training new technicians who can learn about complex equipment and repair procedures in a highly interactive and engaging way.
Moreover, AR can overlay digital information onto real-world environments, supporting maintenance staff by providing step-by-step repair instructions or indicating areas of concern. When used in conjunction with remote assistance technologies, a senior technician can guide a less experienced technician through repairs from a different location, greatly expanding the reach of expertise.
3D Printing for Part Replacement
3D printing technology, also known as additive manufacturing, has the potential to simplify the supply chain for spare parts. Maintenance departments can now print certain high-quality replacement parts on-demand rather than hold large inventories. This reduces lead times and storage costs while also enabling customization of parts for specific repair work or enhancements.
Energy Monitoring and Sustainability
As industries become more conscious of their energy consumption and the broader goal of sustainability, energy monitoring has become an integral part of maintenance operations. By integrating energy management systems, maintenance teams can track, analyze, and optimize energy use across equipment and facilities. This data-driven approach not only minimizes wastage but also helps facilities comply with environmental regulations and achieve sustainability goals.
Collaborative Robotics
Robots have been a part of the industrial landscape for decades; however, the newer wave of collaborative robots (cobots) directly assists human workers. Cobots can be programmed to perform repetitive and hazardous tasks, allowing maintenance personnel to focus on more complex and strategic maintenance work. They enhance safety and productivity, and their intuitive programming and operational flexibility make them a valuable addition to the maintenance toolkit.
Blockchain for Maintenance Records and Contracts
Blockchain is increasingly being explored for its potential in maintaining secure, tamper-proof records. In the context of maintenance, blockchain could ensure the integrity of maintenance logs and service histories, which is crucial for safety, warranties, and resale. Smart contracts built on blockchain platforms could automate various aspects of maintenance operations, including payments and parts ordering, reducing the need for manual processing and record-keeping.
Professional Development and Skills Training
Finally, with the adoption of these new technologies, there's a growing need for maintenance personnel to develop new skills. Continued professional development and training programs now need to include topics such as data analysis, cybersecurity, and IoT device management. The maintenance workforce is evolving into a more tech-savvy ensemble, capable of handling the complexities of modern maintenance technologies.
The trends in maintenance technology and practices highlight a clear directive: the need to embrace innovation to ensure productivity, quality, and sustainability. By keeping up with these trends, maintenance professionals cannot only prevent costly downtimes but also contribute to the long-term success and resilience of their organizations.
Frequently Asked Questions
Frequently Asked Questions
1. What is predictive maintenance, and how does it differ from traditional maintenance methods?
Predictive maintenance involves the use of data analysis tools and techniques to predict equipment failure, allowing proactive maintenance actions to be taken before a breakdown occurs. This differs from traditional maintenance methods that are reactive in nature, where equipment is repaired after it has already failed.
2. How can maintenance software and AI improve maintenance practices?
Maintenance software, such as CMMS, integrated with AI and machine learning algorithms, can optimize maintenance schedules, predict spare parts needs, diagnose issues, and suggest repair solutions. AI technology enhances decision-making processes and helps prioritize maintenance tasks based on their impact on operations.
3. What is the role of augmented reality in maintenance training and repair?
Augmented reality enables technicians to visualize machine components and repairs without physical disassembly, making training more interactive and engaging. It also supports maintenance staff by providing step-by-step repair instructions and remote assistance, improving efficiency and accuracy in maintenance tasks.
4. How does 3D printing technology benefit maintenance departments?
3D printing, or additive manufacturing, allows maintenance departments to produce high-quality replacement parts on-demand, reducing lead times and storage costs. This technology also enables customization of parts for specific repair needs, offering more flexibility in maintaining equipment.
5. Why is energy monitoring important in maintenance operations?
Energy monitoring helps maintenance teams track and optimize energy usage across equipment and facilities, aligning with sustainability goals and regulatory requirements. By analyzing energy data, maintenance departments can identify areas for improvement, reduce waste, and ensure compliance with environmental standards.
6. What are collaborative robots (cobots) and how do they assist maintenance personnel?
Collaborative robots are designed to work alongside human technicians, performing repetitive or hazardous tasks to enhance safety and productivity. Cobots enable maintenance personnel to focus on complex maintenance work, increasing efficiency in maintenance operations.
7. How can blockchain be utilized in maintenance records and contracts?
Blockchain technology ensures secure and tamper-proof maintenance records, enhancing the integrity of service histories and warranty information. Smart contracts built on blockchain platforms automate maintenance processes, such as payments and parts ordering, streamlining maintenance operations.
8. What skills are essential for maintenance personnel in the era of advanced maintenance technologies?
With the rise of new maintenance technologies, maintenance personnel need to develop skills in data analysis, cybersecurity, and IoT device management. Professional development programs should focus on building a tech-savvy workforce capable of leveraging modern maintenance tools and practices for enhanced efficiency.
Resources
Further Resources
For readers interested in delving deeper into the evolving trends and technologies in the maintenance industry, here are some valuable resources to explore:
- Predictive Maintenance and IoT
- Artificial Intelligence in Maintenance
- Augmented Reality Applications
- [The Impact of AR in Maintenance and Repair](https://www.ptc.com/en/support/article?n=Technologies-How- Augmented-Reality-is-Transforming-Industrial-Maintenance)
- AR-Enhanced Training Programs for Maintenance Technicians
- Sustainability and Energy Management
- [Energy Monitoring and Efficiency Strategies](https://www.environmentalleader.com/2019/10/enhancing-energy- efficiency-in-manufacturing/) - Sustainable Practices in Maintenance Operations
- Robotics and Collaborative Automation
- Collaborative Robotics in Maintenance
- [Benefits of Cobots in Industrial Maintenance](https://www.robotics.org/content-detail.cfm/Industrial-Robotics-News/Benefits-of- Collaborative-Robots-in-Manufacturing-Maintenance/content_id/6827)
- Blockchain Technology and Maintenance Records
- Blockchain Applications in Maintenance Management
- [Secure Maintenance Records Using Blockchain](https://iot-internetofthings.com/2018/11/16/blockchain-and-iot-secure- asset-maintenance-and-geolocation-services/)
- Skills Development and Training Resources
These resources offer a wealth of knowledge and insights into the latest advancements shaping the maintenance industry. Whether you are a seasoned professional or just starting in the field, staying informed and continuously learning is key to staying ahead in this dynamic landscape.